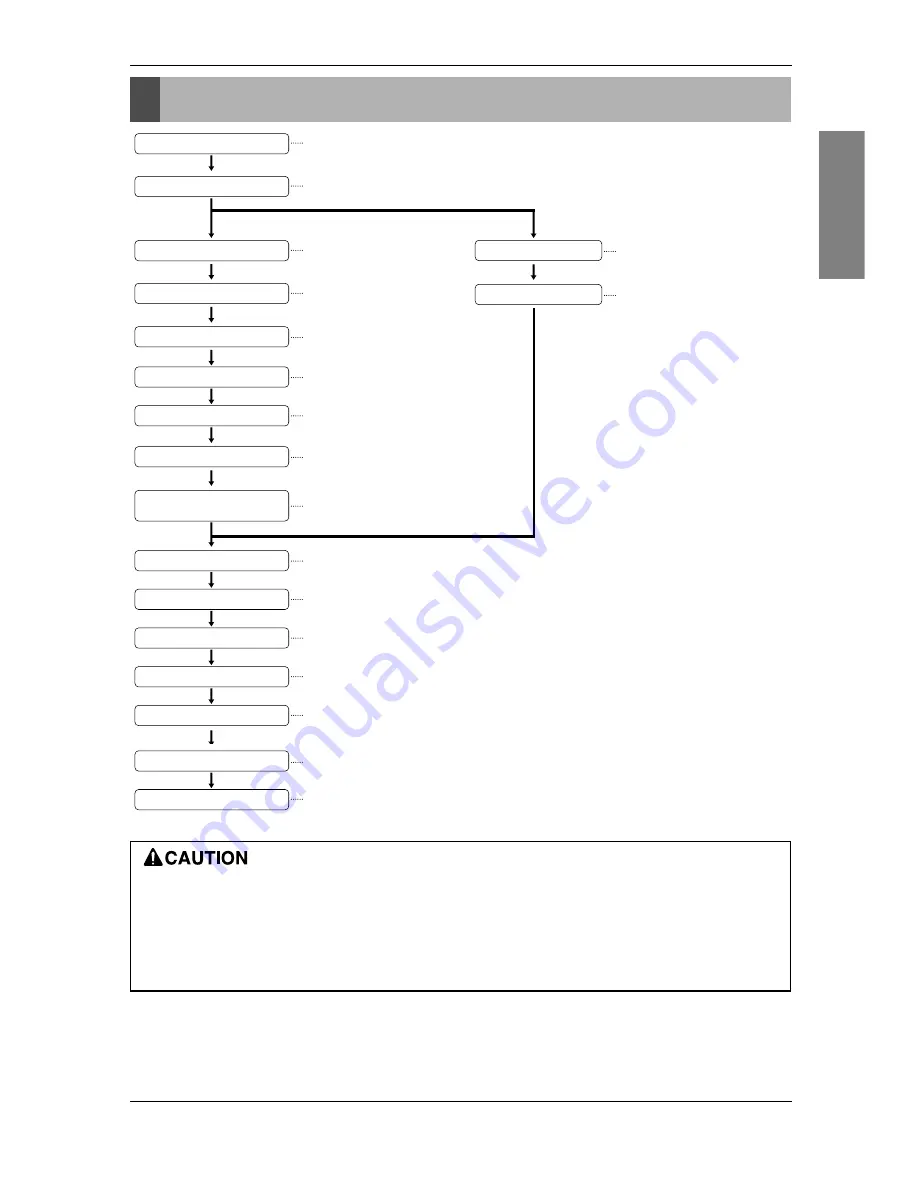
Installation Process
Installation Process
The foundation must be level even
Outdoor unit foundation work
Avoid short circuits and ensure
sufficient space is allowed for service
Installation of outdoor unit
Refer to automatic addressing flowchart
Automatic addressing of indoor unit
In the final check for 24hours at 3.8 MPa(38.7 kgf/cm2) there must be no drop in pressure.
Airtight test
Multiple core cable must not be used.
(suitable cable should be selected)
Electrical work
(connection circuits and drive circuits)
Make sure no gaps are left where
the insulating materials are joined
Heat insulation work
Make sure airflow is sufficient
Duct work
Adjust to downward gradient
Drain pipe work
Special attention to dryness,
cleanness and tightness
Refrigerant piping work
Check model name to make
sure the fitting is made correctly
Installation of indoor unit
Take account of gradient
of drain piping
Sleeve and insert work
Make relationship between outdoor, indoor, remote controller, and option connections clear.
(Prepare control circuit diagram)
Preparation of contract drawings
Indicate clearly who is to be responsible for switch settings
Determination of division work
The vacuum pump used must have a capacity of reaching at least 5 torr, more than 1 hour
Vacuum drying
Recharge correctly as calculated in this manual. and record the amount of added refrigerant
Additional charge of refrigerant
Make sure there are no gaps left between the facing materials used on the ceiling
Fit facing panels
Run each indoor unit in turn to make sure the pipe work has been fitted correctly
Test run adjustment
Explain the use of the system as clearly as possible to your customer and make sure all relevant
documentation is in order
Transfer to customer with explanation
Preheat the crank case with the electrical heater for more than 6 hours.
• The above list indicates the order in which the individual work operations are normally carried out but this order may be
varied where local conditions warrants such change.
• The wall thickness of the piping should comply with the relevant local and national regulations for the designed pres-
sure 3.8MPa.
• Since R410A is a mixed refrigerant, the required additional refrigerant must be charged in its liquid state.(If the refriger-
ant is charged in its gaseous state, its composition changes and the system will not work properly.)
ENGLISH
Installation Manual
7