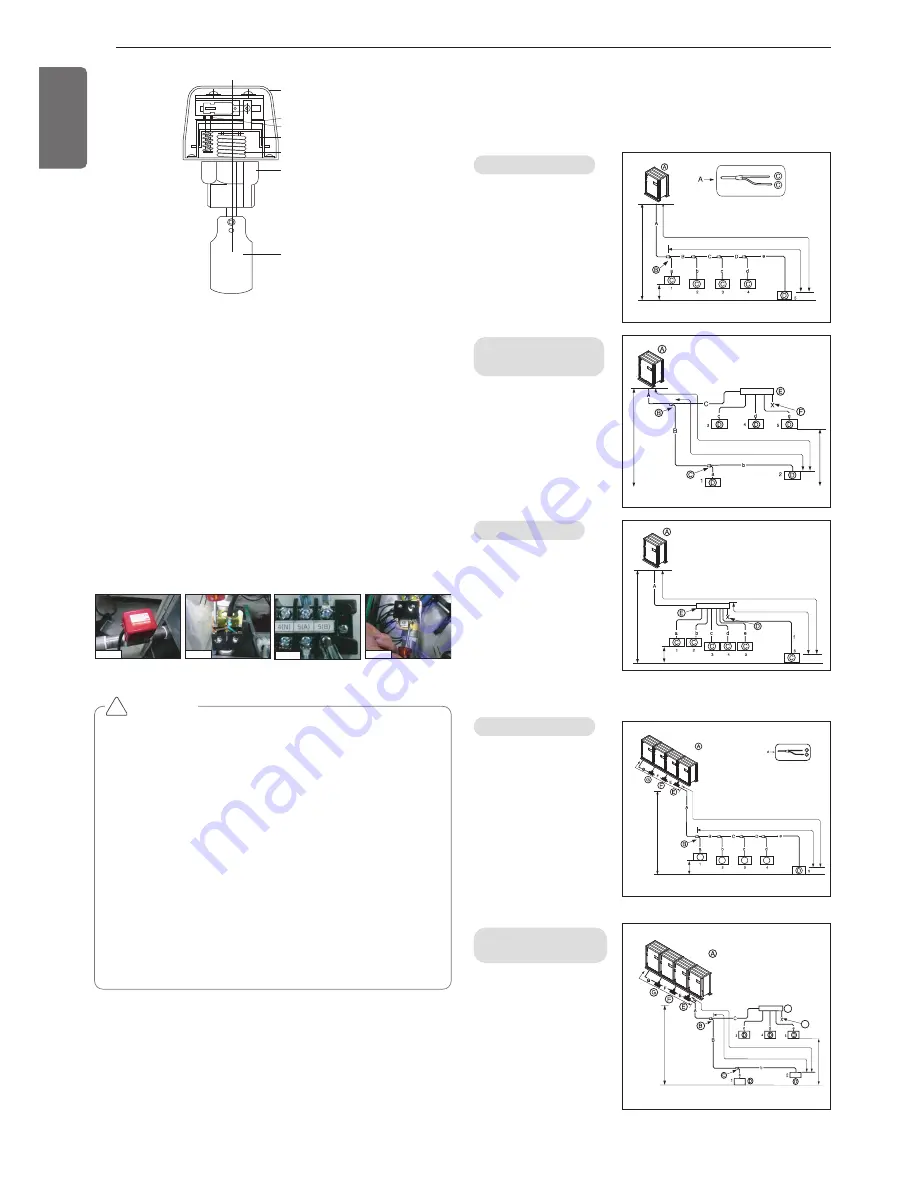
14
ENGLISH
1 inch or
3/4 inch
socket
Cover
Micro-switch
Adjustment screw
Vibration plate
Bellows
Pad
Installation of flow switch
• The flow switch must be installed at the horizontal pipe of the heat
water supply outlet of the product and check the direction of the heat
water flow before the installation. (Picture 1)
• When connecting the flow switch to the product, remove the jump
wire to connect to the communication terminal (5(A) and 5(B)) of the
outside unit control box. (Picture 2, 3) (Open the cover of the flow
switch and check the wiring diagram before connecting the wires.
The wiring method can differ by the manufacturer of the flow
switch.)
• If necessary, adjust the flow rate detection screw after consulting
with an expert and adjust to the minimum flow rate range. (Picture 4)
(Minimum flow rate range of this product is 50%. Adjust the flow
switch to touch the contact point when the flow rate reaches 50% of
the flow rate.)
- Reference flow rate : 10HP – 96LPM, 20HP – 192LPM)
Picture 1
Picture 2
Picture 3
Picture 4
CAUTION
• If the set value does not satisfy the minimum flow rate or if the
set value is changed by the user arbitrarily, it can result in prod-
uct performance deterioration or serious product problem.
• If the product is operated with the heat water supply not flow-
ing smoothly, it can damage the heat exchanger or cause seri-
ous product problems.
• In case of CH24 or CH180 error, there is a possibility that the
plate type heat exchanger is partially frozen inside. In this case
resolve the issue of partial freezing and then operate the prod-
uct again. (Cause of partial freezing : Insufficient heat water
flux, water not supplied, insufficient coolant, alien particle pene-
trated inside plate type heat exchanger)
• When the product operates while the flow switch touches the
contact point at the flow rate range out of the permitted range,
it can cause product performance deterioration or serious prod-
uct problem.
• Must use the normal closed type flow switch
- Circuit of outside unit is normal closed type.
!
Y branch method
Combination of Y
branch/header method
Header method
Ⓐ
: Outside Unit
Ⓑ
: 1st branch (Y branch)
Ⓒ
: Indoor Units
Ⓓ
:
Downward Indoor Unit
Ⓐ
: Outside Unit
Ⓑ
: 1st branch (Y branch)
Ⓒ
: Y branch
Ⓓ
: Indoor Unit
Ⓔ
: Header
Ⓕ
: Sealed piping
Ⓐ
: Outside Unit
Ⓑ
: 1st branch
Ⓒ
: Indoor Units
Ⓓ
: Sealed piping
Ⓔ
: Header
Ⓐ
: Outside Unit
Ⓑ
: 1st branch (Y branch)
Ⓒ
: Indoor Units
Ⓓ
: Downward Indoor Unit
Ⓔ
: Connection branch
pipe between Outside
units: ARCNN41
Ⓕ
: Connection branch
pipe between Outside
units : ARCNN31
Ⓖ
: Connection branch
pipe between Outside
units : ARCNN21
l
40m (90 m : Conditional application)*
h 40m
H 50m
L150m (200 m : Conditional application)*
Indoor
Unit
l
40m (90 m : Conditional application)*
h 40m
H 50m
L150m (200 m : Conditional application)*
l
40m
h 40m
H 50m
L 150m
PIPE CONNECTIONS BETWEEN INDOOR
AND OUTSIDE UNIT
1 Outside Units
Y branch method
Combination of Y branch/
header method
Ⓐ
: Outside Unit
Ⓑ
: 1st branch(Y branch)
Ⓒ
: Y branch
Ⓓ
: Indoor Unit
Ⓔ
: Connection branch pipe
between Outside units :
ARCNN41
Ⓕ
: Connection branch pipe
between Outside units :
ARCNN31
Ⓖ
: Connection branch pipe
between Outside units :
ARCNN21
Ⓗ
: Header
Ⓘ
: Sealed piping
Slave3
Slave2
Slave1
Master
Indoor
Unit
l
40m (90 m : Conditional application)*
H 50m
L150m (200 m : Conditional application)*
h 40m
10m or
less
ODU Capacity
Master ≥ Slave 1 ≥Slave 2 ≥Slave 3
C
C
C
C
l
40m (90 m : Conditional application)*
L150m (200 m : Conditional application)*
h 40m
ODU Capacity
Master ≥ Slave 1 ≥Slave 2 ≥Slave 3
H
I
Slave3
Slave2
Slave1
Master
H 50m
10m or
less
Series Outside Units (2 Units ~ 4 Units)
h
* : See the Table 4
h
* : See the Table 4
h
* : See the Table 4
h
* : See the Table 4
Summary of Contents for Multi V ARWN Series
Page 37: ......