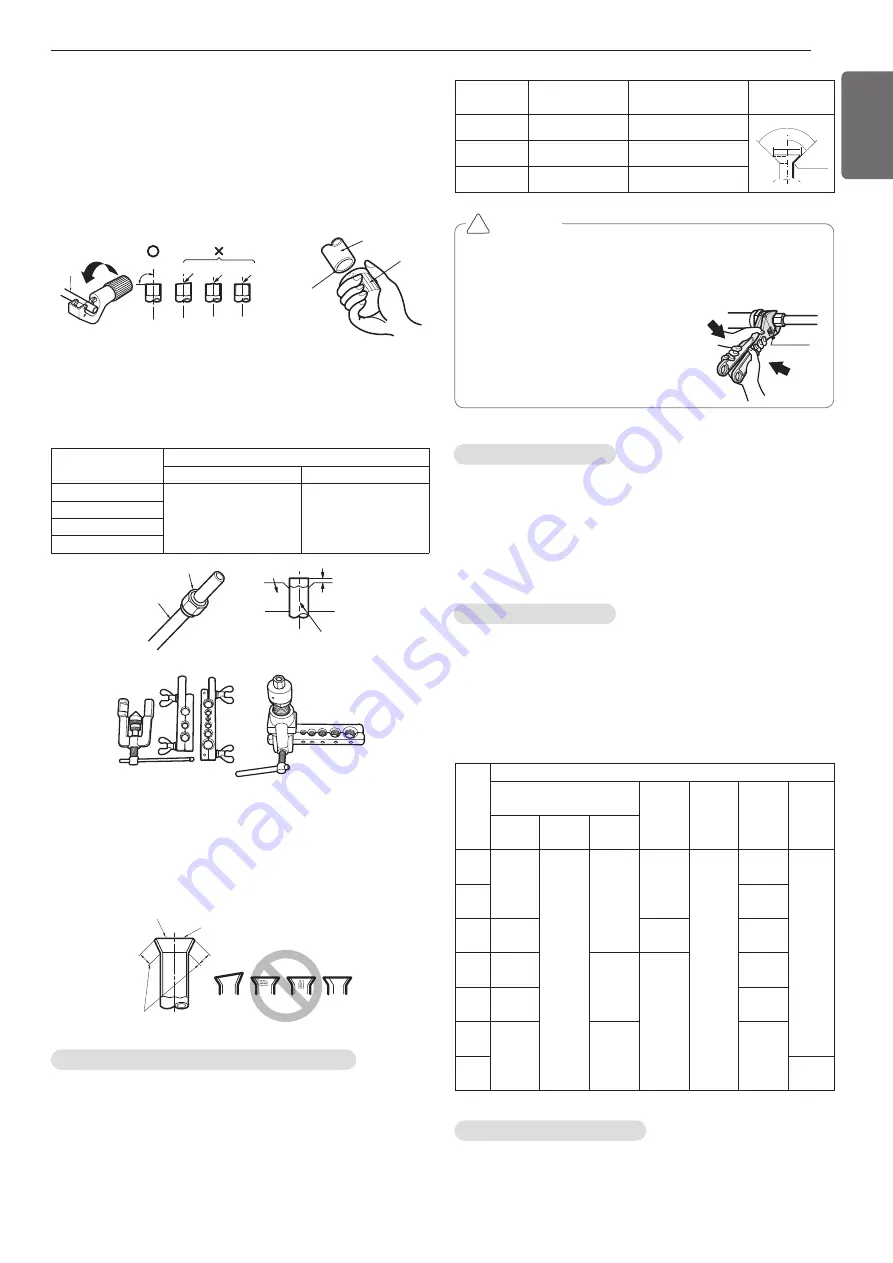
11
ENGLISH
Check
- Compare the flared work with figure below.
- If flare is noted to be defective, cut off the flared section and do
flaring work again.
Burrs removal
- Completely remove all burrs from the cut cross section of pipe/tube.
- Put the end of the copper tube/pipe to downward direction as you
remove burrs in order to avoid to let burrs drop in the tubing.
Inclined
Inside is shining without scratches.
Smooth all round
Even length
all round
Surface
damaged
Cracked Uneven
thickness
= Improper flaring =
Flare shape and flare nut tightening torque
Opening shutoff valve
Precautions when connecting pipes
- See the following table for flare part machining dimensions.
- When connecting the flare nuts, apply refrigerant oil to the inside and
outside of the flares and turn them three or four times at first. (Use
ester oil or ether oil.)
- See the following table for tightening torque.(Applying too much torque may
cause the flares to crack.)
- After all the piping has been connected, use nitrogen to perform a
gas leak check.
1
Remove the cap and turn the valve counter clockwise with the
hexagon wrench.
2
Turn it until the shaft stops.
Do not apply excessive force to the shutoff valve. Doing so may
break the valve body, as the valve is not a backseat type. Always
use the special tool.
3
Make sure to tighten the cap securely.
Pipe size
[mm (inch)]
Tightening Torque
N.m (lbs.ft)
A [mm (inch)]
Flare shape
Ø9.52 (3/8)
38±4 (28±3.0)
12.8 (0.5)~13.2 (0.52)
90°
±2
45°
±2
A
R=0.4~0.8
Ø12.7 (1/2)
55±6 (41±4.4)
16.2 (0.64)~16.6 (0.65)
Ø15.88 (5/8)
75±7 (55±5.2)
19.3 (0.76)~19.7(0.78)
CAUTION
• Always use a charge hose for service port connection.
• After tightening the cap, check that no refrigerant leaks are present.
• When loosening a flare nut, always use two wrenches in
combination, When connecting the piping,
always use a spanner and torque wrench
in combination to tighten the flare nut.
• When connecting a flare nut, coat the
flare(inner and outer faces) with oil for
R410A(PVE) and hand tighten the nut
3 to 4 turns as the initial tightening.
Union
!
Closing shutoff valve
1
Remove the cap and turn the valve clockwise with the hexagon
wrench.
2
Securely tighten the valve until the shaft contacts the main body seal.
3
Make sure to tighten the cap securely.
* For the tightening torque, refer to the table on the below.
Tightening torque
Shut
off
valve
size
(mm
(inch))
Tightening torque N.m (lbs.ft) (Turn clockwise to close)
Shaft
(valve body)
Cap
(Valve lid)
Service
port
Flare nut
Gas line
piping
attached
to unit
Closed
Opened
Hexagonal
wrench
Ø6.35
(1/4)
6.0±0.6
(4.4±0.4)
5.0±0.0
(3.7±0.4)
4 mm
(0.16 inch)
17.6±2.0
(13.0±1.5)
12.7±2
(9.4±1.5)
16±2
(12±1.5)
-
Ø9.52
(3/8)
38±4
(28±3.0)
Ø12.7
(1/2)
10.0±1.0
(7.4±0.7)
20.0±2.0
(14.8±1.5)
55±6
(41±4.4)
Ø15.88
(5/8)
12.0±1.2
(8.9±0.9)
5 mm
(0.24 inch)
25.0±2.5
(18.4±1.8)
75±7
(55±5.1)
Ø19.05
(3/4)
14.0±1.4
(10.3±1.0)
110±10
(81.1±7.4)
Ø22.2
(7/8)
30.0±3.0
(22.1±2.2)
8 mm
(0.31 inch)
-
Ø25.4
(1)
25±3
(18.5±2.2)
Main cause of gas leakage is defect in flaring work. Carry out correct
flaring work in the following procedure.
Cut the pipes and the cable
- Use the accessory piping kit or the pipes purchased locally.
- Measure the distance between the indoor and the outdoor unit.
- Cut the pipes a little longer than measured distance.
- Cut the cable 1.5 m (4.92 ft) longer than the pipe length.
Preparation of Piping
Pipe
Reamer
Point down
Copper
tube
90°
Slanted Uneven Rough
Flaring work
- Carry out flaring work using flaring tool as shown below.
Firmly hold copper tube in a bar(or die) as indicated dimension in the
table above.
Pipe diameter
Inch (mm)
A inch (mm)
Wing nut type
Clutch type
Ø1/4 (Ø6.35)
0.04~0.07 (1.1~1.8)
0~0.02 (0~0.5)
Ø3/8 (Ø9.52)
Ø1/2 (Ø12.7)
Ø5/8 (Ø15.88)
Bar
Copper pipe
"A"
<Wing nut type>
<Clutch type>
Flare nut
Copper tube
Insulation of shutoff valve
1
Use the heat insulation material for the refrigerant piping which has
an excellent heat-resistance (over 120 °C [248 °F]).
Summary of Contents for Multi V 5 ARUM080LTE5
Page 55: ......