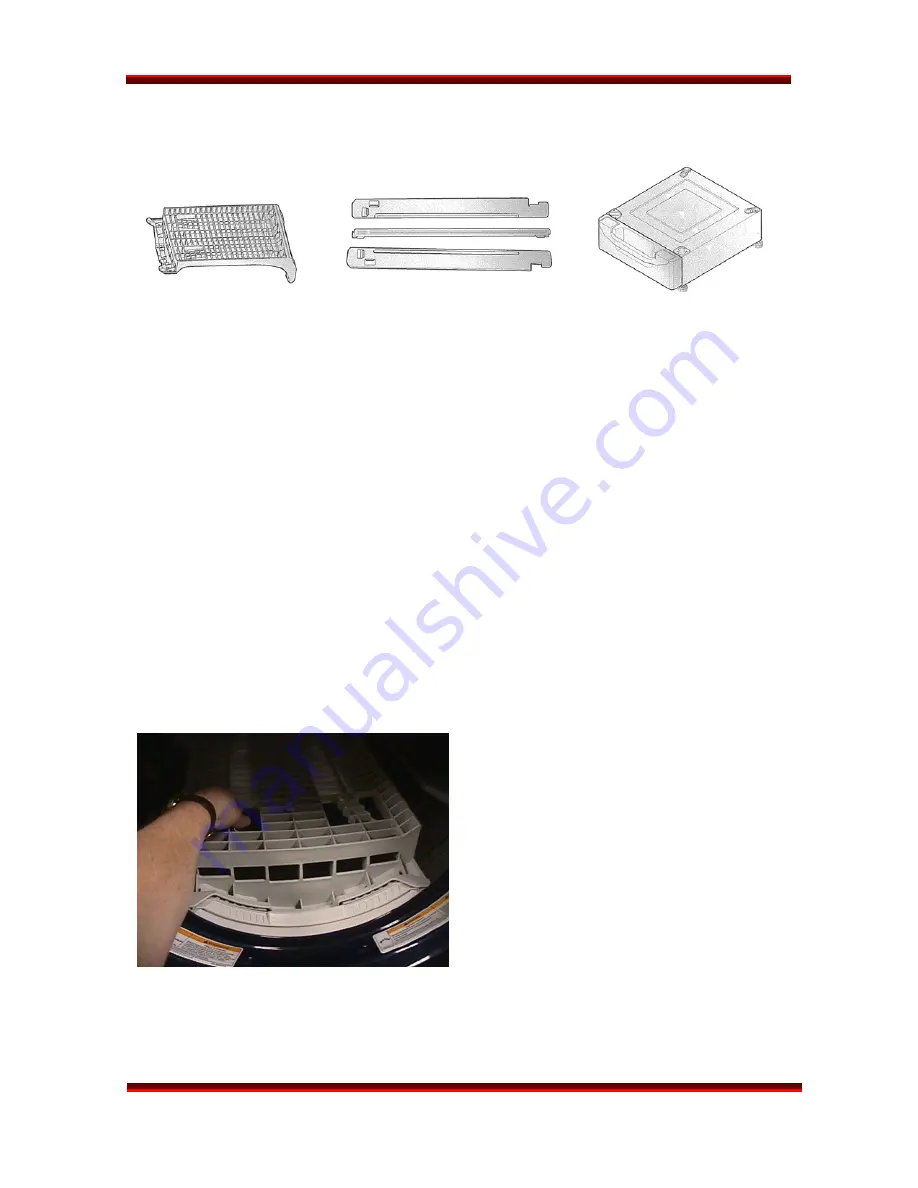
TRAINING MANUAL
DLEX8377WM
DLEX8388WM
Page 9
STEAM DRYER
ACCESSORIES
DRYING RACK STACKING KIT
PEDESTAL
The DRYING RACK is used to dry items that should not be tumbled, like sweaters, tennis
shoes, etc. It should be removed and stored when not in use. The rack is included with
the dryer. (See installation procedure, below.)
The STACKING KIT is used to stack a dryer on top of a matching washer. (NEVER put a
washer on top of a dryer!) The stacking kit should not be used in situation where there is
the possibility of excessive vibration and movement of the washer, such as in a mobile
home or an upper floor of a frame structure. The stacking kit is available as an optional
purchase. (See installation procedure, page 10.)
The PEDESTAL can be used under either the washer or the dryer. It is possible to stack a
washer and dryer on a pedestal, but the dryer controls may be difficult to reach and the
possibility of vibration and movement is greater. The pedestal is available as an optional
purchase. (See installation procedure, pages 12
~
13.) Pedestals are available in heights
of 7
¼
” and 13”.
INSTALLATION
(RACK)
Open the dryer door.
Put the rack in place.
Select RACK DRY (2
nd
button on right)
Press START.
Be sure the front of the rack is properly
situated in the notches on either side
of the filter. The back should rest on the
drum and allow the drum to rotate.
Summary of Contents for DLEX8377WM - SteamDryer Series - 27in Front-Load Electric Dryer
Page 1: ...LG TRAINING MANUAL LG TRAINING MANUAL Steam Dryers DLEX8377 M DLG8388 M Fall 2008 ...
Page 25: ...TRAINING MANUAL DLEX8377WM DLEX8388WM Page 23 STEAM DRYER SCHEMATIC ELECTRIC DRYER ...
Page 26: ...TRAINING MANUAL DLEX8377WM DLEX8388WM Page 24 STEAM DRYER SCHEMATIC GAS DRYER ...
Page 75: ...TRAINING MANUAL DLEX8377WM DLEX8388WM Page 73 STEAM DRYER SERVICE BULLETINS ...
Page 76: ...TRAINING MANUAL DLEX8377WM DLEX8388WM Page 74 STEAM DRYER ...
Page 77: ...TRAINING MANUAL DLEX8377WM DLEX8388WM Page 75 STEAM DRYER ...
Page 78: ...TRAINING MANUAL DLEX8377WM DLEX8388WM Page 76 STEAM DRYER ...
Page 79: ...TRAINING MANUAL DLEX8377WM DLEX8388WM Page 77 STEAM DRYER ...
Page 80: ...TRAINING MANUAL DLEX8377WM DLEX8388WM Page 78 STEAM DRYER ...
Page 81: ...TRAINING MANUAL DLEX8377WM DLEX8388WM Page 79 STEAM DRYER ...
Page 82: ...TRAINING MANUAL DLEX8377WM DLEX8388WM Page 80 STEAM DRYER ...
Page 83: ...TRAINING MANUAL DLEX8377WM DLEX8388WM Page 81 STEAM DRYER ...
Page 84: ...TRAINING MANUAL DLEX8377WM DLEX8388WM Page 82 STEAM DRYER ...
Page 85: ......
Page 86: ...Steam Dryer Fall 2008 ...