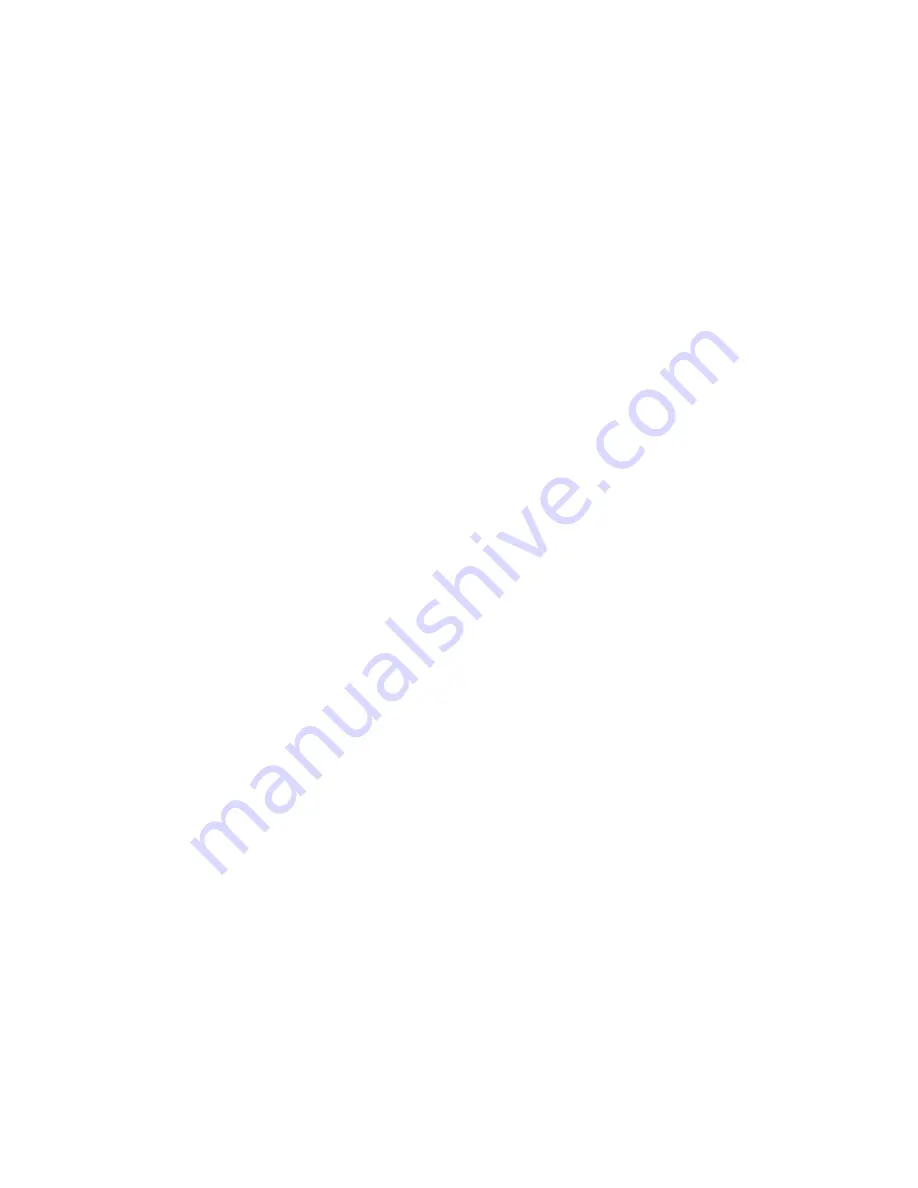
—2—
1. PREFACE
1.1 SPECIFICATIONS ..........................................3
1.2 FEATURES AND BENEFITS ..........................4
1.3 CONTROL LOCATIONS .................................6
1.4 ADDITIONAL CONTROLS..............................7
2. DISASSEMBLY INSTRUCTIONS
2.1 MECHANICAL PARTS....................................9
2.1.1 FRONT GRILLE .....................................9
2.1.2 CONTROL BOX (Half-Disassembly)....10
2.1.3 CONTROL BOX (Full-Disassembly) ....10
2.2 AIR HANDLING PARTS................................11
2.2.1 HEATER ASSEMBLY AND CROSS
FLOW FAN...........................................11
2.2.2 FAN ......................................................11
2.2.3 SHROUD..............................................12
2.3 ELECTRICAL PARTS ...................................12
2.3.1 OUTDOOR MOTOR ............................12
2.3.2 INDOOR MOTOR ................................12
2.3.3 COMPRESSOR ...................................12
2.3.4 CAPACITOR ........................................12
2.3.5 POWER CORD ....................................13
2.3.6 P.C.B....................................................13
2.4 REFRIGERATION CYCLE............................14
2.4.1 CONDENSER ......................................14
2.4.2 EVAPORATOR ....................................14
2.4.3 CAPILLARY TUBE...............................14
3. INSTALLATION
3.1 HOW TO INSTALL THE UNIT ......................17
3.2 SUGGESTED TOOL REQUIREMENTS .......18
3.2.1 PREPARATION OF SLEEVE ..............18
3.2.2 PREPARATION OF THE FRONT
GRILLE ................................................18
3.2.3 UNIT INSTALLATION ..........................19
3.3 ELECTRICAL REQUIREMENTS ..................20
3.3.1 ELECTRICAL DATA (FOR 230V/208 MODEL)........20
3.3.2 ELECTRICAL SAFETY ............................20
4. FERFORMANCE DATA
.................................21
5. TROUBLESHOOTING GUIDE
5.1 OUTSIDE DIMENSIONS...............................26
5.2 PIPING SYSTEM ..........................................26
5.3 TROUBLESHOOTING GUIDE......................27
6. SCHEMATIC DIAGRAM
.....................32
7. EXPLODED VIEW
..................................33
8. REPLACEMENT PARTS LIST
.......34
1. PREFACE
This
SERVICE MANUAL
provides various service information, including the mechanical and electrical
parts etc. This room air conditioner was manufactured and assembled under a strict quality control system.
The refrigerant is charged at the factory. Be sure to read the safety precautions prior to servicing the unit.
1.1 SAFETY PRECAUTIONS
1. When servicing the unit, set the ROTARY SWITCH
or POWER SWITCH to OFF(O) and unplug the
power cord.
2. Observe the original lead dress.
If a short circuit is found, replace all parts which
have been overheated or damaged by the short
circuit.
3. After servicing the unit, make an insulation
resistance test to protect the customer from being
exposed to shock hazards.
1.2 INSULATION RESISTANCE TEST
1. Unplug the power cord and connect a jumper
between 2 pins (black and white).
2. The grounding conductor (green or green & yellow)
is to be open.
3. Measure the resistance value with an ohm meter
between the jumpered lead and each exposed
metallic part on the equipment at all the positions
(except OFF or O) of the ROTARY SWITCH.
4. The value should be over 2M
Ω
.
CONTENTS