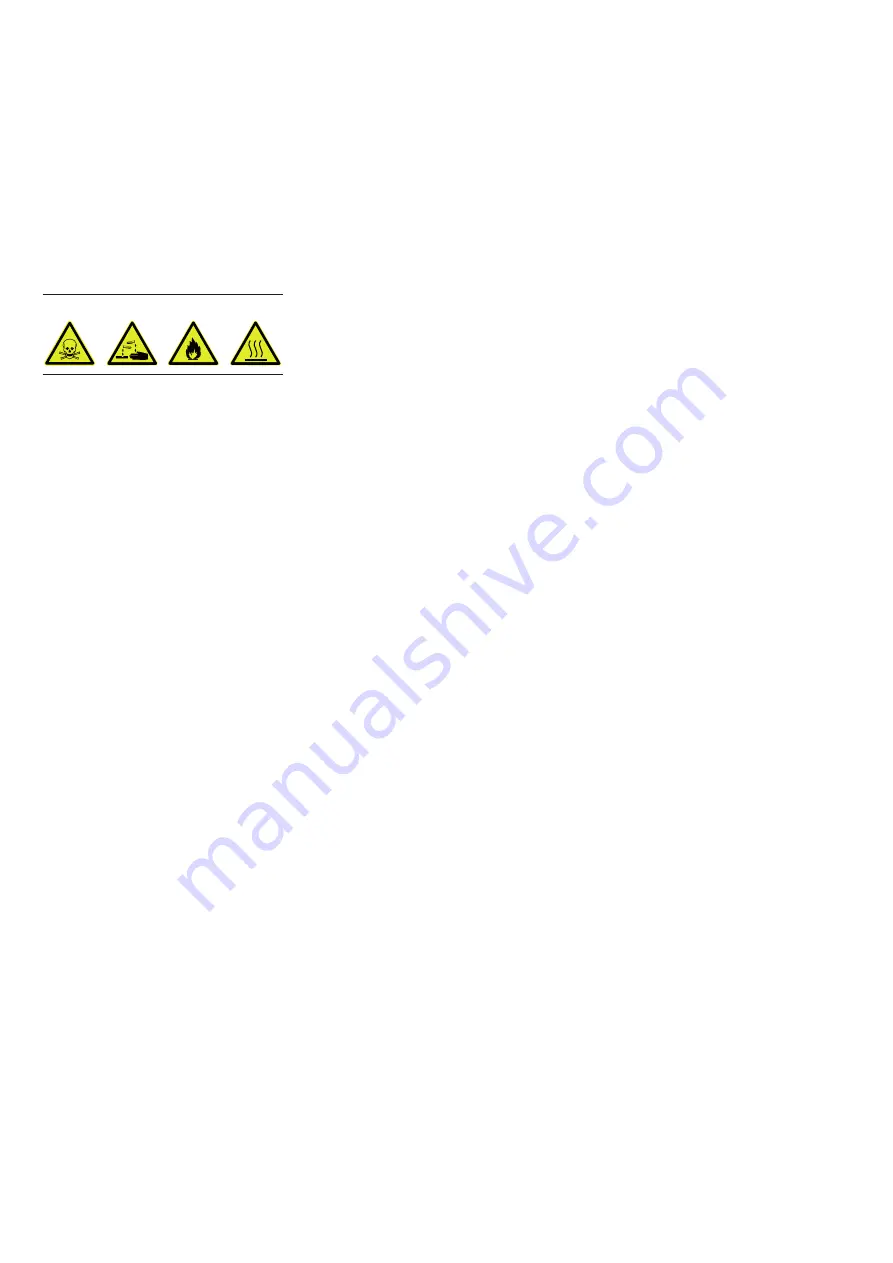
Maintenance
36
GA01301_002_C1 - 07/2018 - © Leybold
5.3 Monitoring the Oil Level
During operation of the TRIVAC BCS the oil level must always remain bet-
ween marks (9/2) and (9/3) on the oil-level glass. The amount of oil must be
checked and topped up as required.
Check and top up oil only after having shut down the pump first.
Please note the safety information given in Section 0.3 und 0.4.
Pumps which have not directly been delivered from Leybold, e.g. in sys tems,
may have been filled with oils different from LVO 100. In this case a refill with
LVO 100 may cause problems. Therefore check before the refill the kind of oil
in the pump and fill in only suitable oil or change the oil.
When operating the TRIVAC BCS in connection with the exhaust filter with
lubricant return (ARS 40-65) the checking intervals are extended.
When using the oil float switch (LSS) remote monitoring of the lubricant is
possible.
5.3.1 Checking the Condition of LVO 100
The ageing process for the standard operating fluid LVO 100 respectively
(see Section 1.2) will depend very much on the area of application for the
pump.
There exist the following ways of checking the oil:
a) Visual check
Normally the oil is clear and transparent. If the oil darkens, it should be chan-
ged.
b) Chemical check
The neutralisation number of LVO 100 oil is determined according to DIN
51558. If it exceeds 2, the oil should be changed.
c) Viscosity check
If the viscosity of LVO 100 at 25 °C exceeds a level of 240 mPas (20 % high-
er than the viscosity of fresh oil) an oil change is recommended.
If gases or liquids dissolved in the oil result in a deterioration of the ultimate
pressure, the oil can be degassed by allowing the pump to run for approx.
30 min. with the intake port closed and the gas ballast valve open.
When wanting to check the oil, switch off the pump first and drain out from
the warm pump the required amount of oil through the oil drain (9/4) into a
beaker or similar.
Please note the safety information given in Section 5.4.
CAUTION