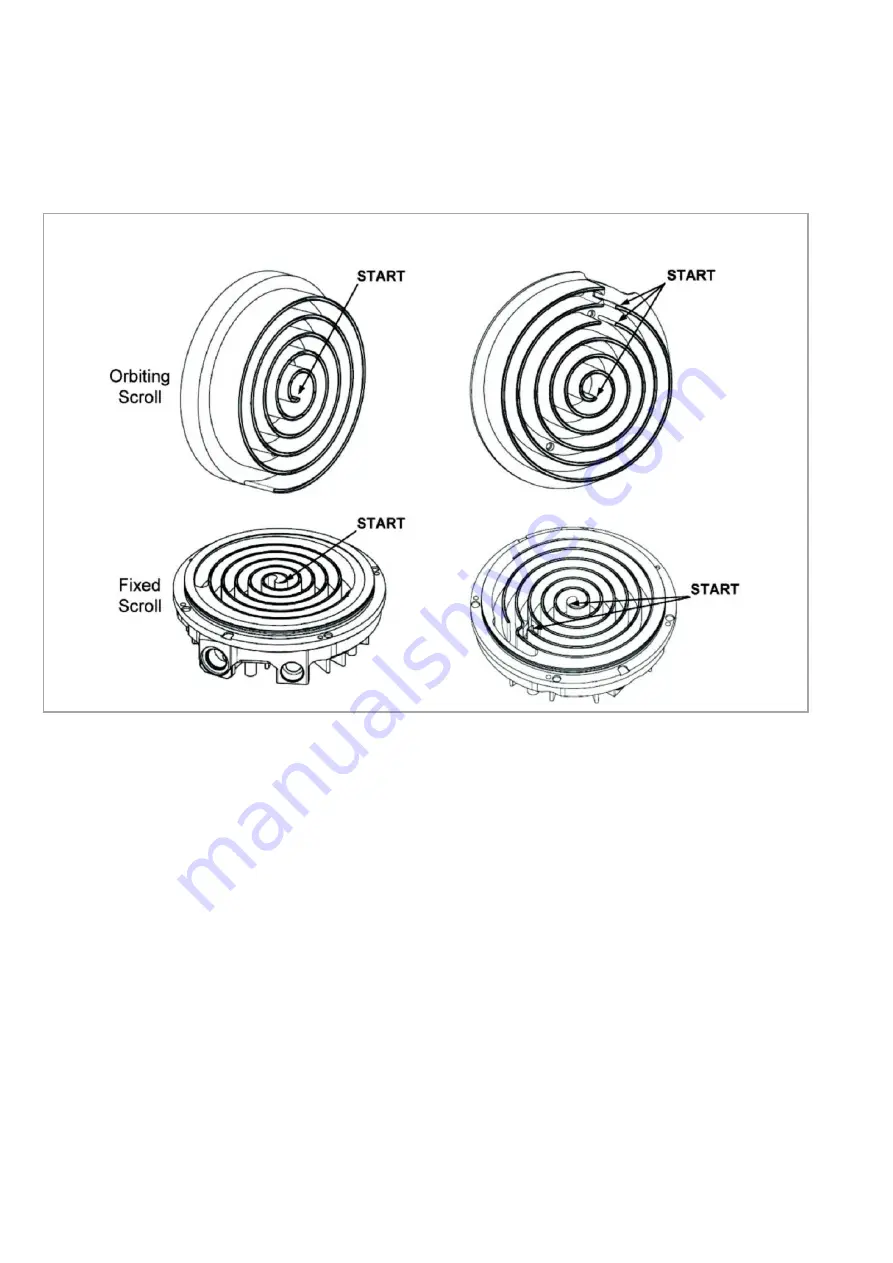
8
300668736_002_C0 - 11/2017 - © Leybold
Starting at the centre of the scroll form, insert the tip seal into the tip seal
channel. Ensure that each tip seal starts as close as possible at the start of
the scroll channel. (Figure 6).
Note: The SCROLLVAC 18 plus has multiple tip seal starts in both the
Orbiting and Fixed scrolls.
Continue to push the tip seal into the tip seal channel while working your way
around the channel profile until you have reached the end. Ensure the tip seal
is pressed squarely and fully home at each pinch point, these are located
closer to the centre of the scroll.
Cut short the tip seal at the end of the scroll channel. There should be at
least 10 mm between the end of the channel and the tip seal, this is to allow
for expansion.
Note: A mark is provided at the end of all the tip seal channels to indicate
where to cut the tip seal (Figure 7).
Figure 6 - Tip seal fitting
SCROLLVAC SC 7 to SC 15 plus
SCROLLVAC SC 18 plus