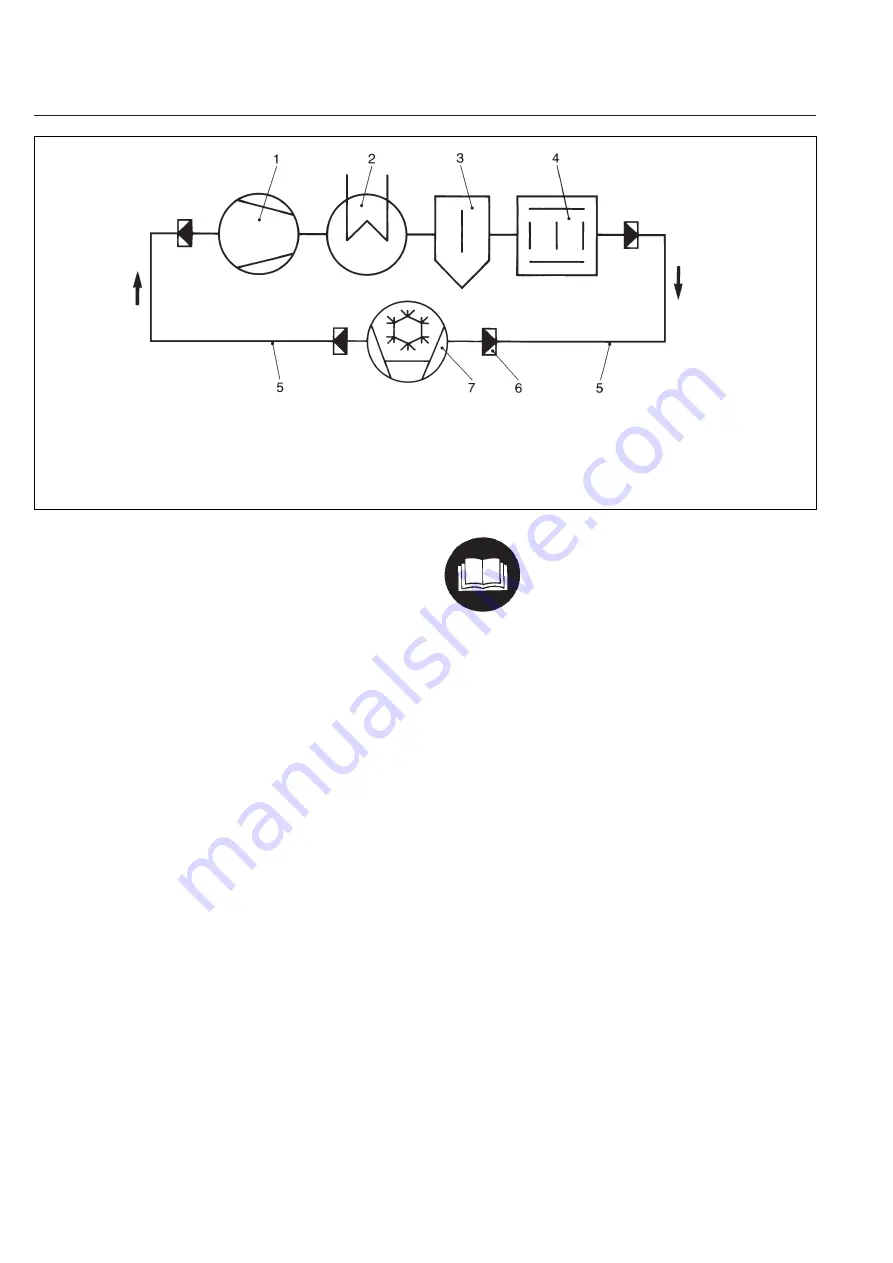
GA 12.137/2.02 - 05/2002
Description
Contents
Page
1
Description . . . . . . . . . . . . . . . . . . . . . . . . . . 3
1.1
Design and function . . . . . . . . . . . . . . . . . . . 3
1.2
Standard equipment . . . . . . . . . . . . . . . . . . . 5
1.3
Technical specifications . . . . . . . . . . . . . . . . . 7
1.4
Order information . . . . . . . . . . . . . . . . . . . . . 8
2
Installation . . . . . . . . . . . . . . . . . . . . . . . . . . . 9
2.1
Safety information . . . . . . . . . . . . . . . . . . . . . 9
2.2
Unpacking and inspecting . . . . . . . . . . . . . . 12
2.3
Mounting . . . . . . . . . . . . . . . . . . . . . . . . . . . 12
2.4
Ambient conditions and coolant connection . 13
2.5
Electrical connection . . . . . . . . . . . . . . . . . . 16
2.6
Mounting the flexlines . . . . . . . . . . . . . . . . . 20
3.
Operation . . . . . . . . . . . . . . . . . . . . . . . . . . 23
3.1
Switching on . . . . . . . . . . . . . . . . . . . . . . . . 23
3.2
Normal operation . . . . . . . . . . . . . . . . . . . . . 23
3.3
Switching off . . . . . . . . . . . . . . . . . . . . . . . . 24
3.4
Removing from service . . . . . . . . . . . . . . . . 24
3.4.1
Transport and storage . . . . . . . . . . . . . . . . . 25
3.5
Interface description . . . . . . . . . . . . . . . . . . 26
4.
Maintenance . . . . . . . . . . . . . . . . . . . . . . . . 30
4.1
Helium gas pressure adjustment . . . . . . . . . 30
4.2
Replacing the adsorber . . . . . . . . . . . . . . . . 31
4.3
Changing the fuses for the control voltage . . 33
4.4
Leybold service . . . . . . . . . . . . . . . . . . . . . . 33
5
Troubleshooting . . . . . . . . . . . . . . . . . . . . . . 35
6
Spare parts . . . . . . . . . . . . . . . . . . . . . . . . . 38
7
Appendix: Conformance statement /
Electrical Schematic / Certifications . . . . . . . 39
Service personnel shall without fail read the
instructions provided for their guidance
(ISO 7000-0419).
Precautionary notes used in these instructions:
Warning
This indicates procedures and operations which must be
strictly observed to prevent hazards to persons.
Caution
This indicates procedures and operations which must be
strictly observed to prevent damage to or destruction of
the unit.
Illustrations
In the references to illustrations, such as (1/2), the first
number is the figure number, while the second digit iden-
tifies the item in the illustration.
We reserve the right to adopt modifications in the
engineering design and the specifications indicated
here.
The illustrations are not binding.
2
Legend for Fig. 1
1
Helium compressor
2
Heat exchanger
3
Oil separator
4
Oil adsorber
5
flexlines
6
Self-sealing couplings
7
Cold head or cryo pump
Fig. 1 Simplified schematic for the helium circuit