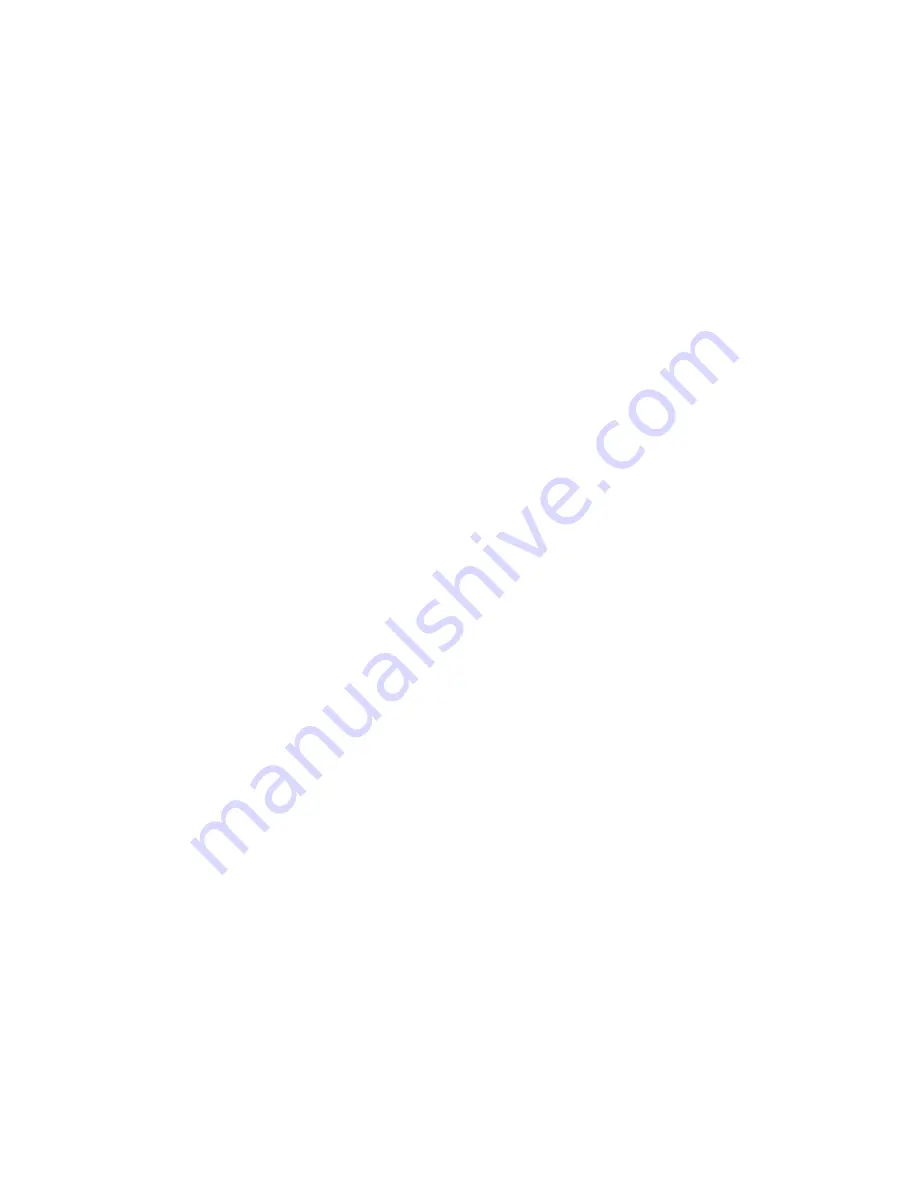
P/N
Part name
Page
40X8753
Motor (staple finisher aligner paddle).....................................................................................................1348
40X9079
Audio speaker.............................................................................................................................................. 1270
40X9879
Contact Authentication Device................................................................................................................. 1341
40X9935
Fax Card.......................................................................................................................................................... 1341
41X0023
MarkNet N8360 Wireless Network Card................................................................................................1341
41X0028
DDR3-G2 512Mx32 RAM, 2GB.................................................................................................................. 1341
41X0052
Board, 10.1
‑
inch control panel................................................................................................................... 1274
41X0056
Toner supply actuator.................................................................................................................................1296
41X0057
TPS wiper actuator......................................................................................................................................1300
41X0058
MPF media present actuator.................................................................................................................... 1278
41X0059
MPF tray front actuator...............................................................................................................................1278
41X0060
MPF tray rear actuator................................................................................................................................ 1278
41X0062
Hold down arm.............................................................................................................................................1302
41X0063
Transfer belt right bias arm....................................................................................................................... 1302
41X0064
Transfer belt left bias arm..........................................................................................................................1302
41X0065
Rear nip release arm................................................................................................................................... 1276
41X0066
Front nip release arm..................................................................................................................................1276
41X0067
Feeder bearing............................................................................................................................................ 1280
41X0069
smart chip interface board........................................................................................................................ 1296
41X0070
Right cover bracket..................................................................................................................................... 1270
41X0071
Upper duplex sensor bracket...................................................................................................................1276
41X0072
Lower duplex sensor bracket................................................................................................................... 1276
41X0073
Connector cover, metal.............................................................................................................................. 1278
41X0074
Frame connector bracket.......................................................................................................................... 1282
41X0076
Printhead data cable...................................................................................................................................1294
41X0078
Fuser connect cable................................................................................................................................... 1284
41X0079
Transfer roller housing............................................................................................................................... 1300
41X0080
Left door rear catch..................................................................................................................................... 1278
41X0081
Left door front catch....................................................................................................................................1278
41X0082
Printhead clamp........................................................................................................................................... 1294
41X0083
Toner cartridge contact (CMY)................................................................................................................. 1296
41X0084
Toner cartridge contact (K)........................................................................................................................1296
41X0085
Transfer belt contact................................................................................................................................... 1300
41X0086
Developer roll power contact...................................................................................................................1294
7564
Part number index
1523
Summary of Contents for XC8155
Page 22: ...7564 Table of contents 22 ...
Page 101: ...Staple jam in door G 1 Open door C 2 Open door G 7564 Diagnostic information 101 ...
Page 103: ...3 5 Close the staple guard 7564 Diagnostic information 103 ...
Page 106: ... Area J1 Areas J3 and J4 Areas J5 and J6 3 Close door J 7564 Diagnostic information 106 ...
Page 630: ...5 From the rear remove the screw B A B A 7564 Repair information 630 ...
Page 647: ...2 Open door A 3 Remove the waste toner bottle 7564 Repair information 647 ...
Page 653: ...2 Open door A 3 Remove the waste toner bottle 4 Open door A1 7564 Repair information 653 ...
Page 654: ...5 Remove the transfer belt Pick roller removal 1 Remove the tray 7564 Repair information 654 ...
Page 656: ...2 Remove the separator pad Door rod cover removal 1 Remove tray 1 7564 Repair information 656 ...
Page 660: ...6 Remove the fan D D 7564 Repair information 660 ...
Page 674: ...A B 3 Remove the HVPS 7564 Repair information 674 ...
Page 676: ...3 Remove the SIM 7564 Repair information 676 ...
Page 682: ...7 Remove the five screws A A 7564 Repair information 682 ...
Page 699: ...12 Remove the two screws A from the appropriate contact B A B 7564 Repair information 699 ...
Page 706: ...A 8 Remove the ground screw B from the front column B 7564 Repair information 706 ...
Page 719: ...5 Remove the ten screws C securing the motor ADF C 7564 Repair information 719 ...
Page 773: ...4 Remove the two screws A and then remove the motor A 7564 Repair information 773 ...
Page 778: ...3 Remove the bracket 7564 Repair information 778 ...
Page 779: ...4 Move the actuator away and then behind the sensor 7564 Repair information 779 ...
Page 782: ...2 Remove the four screws A A 7564 Repair information 782 ...
Page 792: ...5 Remove the four screws A A A 7564 Repair information 792 ...
Page 793: ...A 6 Push the plate and then pull the assembly to remove 1 2 7564 Repair information 793 ...
Page 847: ...9 Remove the two screws B B 10 Disconnect the cable C C 7564 Repair information 847 ...
Page 849: ...13 Pry the retainer clockwise to unlock and then loosen it 2 1 7564 Repair information 849 ...
Page 856: ...1 2 13 Remove the cam gear assembly 7564 Repair information 856 ...
Page 857: ...14 Pry the retainer clockwise to unlock and then loosen it 2 1 7564 Repair information 857 ...
Page 858: ...15 Release and then remove the bracket from the frames 2 1 3 4 7564 Repair information 858 ...
Page 880: ...3 Remove the two screws A A 4 Remove the motor 7564 Repair information 880 ...
Page 887: ...A B B A 7564 Repair information 887 ...
Page 890: ...7 Remove the four screws E E E E 7564 Repair information 890 ...
Page 893: ...7 Remove the two screws A and then remove the retainer B A B 7564 Repair information 893 ...
Page 900: ...8 Remove the 10 screws C C C 7564 Repair information 900 ...
Page 901: ...9 Remove the four screws D and then set aside the HPT lock D D D 7564 Repair information 901 ...
Page 904: ...10 Remove the two screws A and then remove the retainer B A B 7564 Repair information 904 ...
Page 905: ...11 Remove the 10 screws C C C 7564 Repair information 905 ...
Page 906: ...12 Remove the four screws D D D D 7564 Repair information 906 ...
Page 908: ...16 Remove the roller G G 7564 Repair information 908 ...
Page 913: ...2 Open the hinges and then remove the door 7564 Repair information 913 ...
Page 918: ...Note The latches engage with the holes A on the frame A A 1 3 2 7564 Repair information 918 ...
Page 929: ...5 Remove the two screws C and then remove the cover C 7564 Repair information 929 ...
Page 948: ...5 Remove the two screws A and then open the cage A 7564 Repair information 948 ...
Page 952: ...5 Remove the two screws A and then open the cage A 7564 Repair information 952 ...
Page 957: ...7 Release the bracket from the carriage 7564 Repair information 957 ...
Page 968: ...5 Remove the two screws A and then open the cage A 7564 Repair information 968 ...
Page 970: ...5 Remove the two screws A and then open the cage A 7564 Repair information 970 ...
Page 972: ...5 Remove the two screws A and then open the cage A 7564 Repair information 972 ...
Page 974: ...5 Remove the two screws A and then open the cage A 7564 Repair information 974 ...
Page 976: ...5 Remove the two screws A and then open the cage A 7564 Repair information 976 ...
Page 979: ...5 Remove the two screws A and then open the cage A 7564 Repair information 979 ...
Page 983: ...5 Remove the two screws A and then open the cage A 7564 Repair information 983 ...
Page 987: ...5 Remove the two screws A and then open the cage A 7564 Repair information 987 ...
Page 991: ...6 Remove the two screws A and then open the cage A 7564 Repair information 991 ...
Page 993: ...8 Remove the four screws C and then pull the bracket C 7564 Repair information 993 ...
Page 995: ...5 Remove the two screws A and then open the cage A 7564 Repair information 995 ...
Page 997: ...5 Remove the two screws A and then open the cage A 7564 Repair information 997 ...
Page 1002: ...E D F 7564 Repair information 1002 ...
Page 1009: ...5 Remove the two screws A and then open the cage A 7564 Repair information 1009 ...
Page 1017: ...B C 7564 Repair information 1017 ...
Page 1023: ...20 Using a Torx screwdriver remove the three screws E E D 7564 Repair information 1023 ...
Page 1028: ...19 Disconnect the two cables J J 20 Remove the screw K K 7564 Repair information 1028 ...
Page 1030: ...23 Pull the shaft to the front and then lift it 1 2 7564 Repair information 1030 ...
Page 1039: ...13 Remove the two screws A and then open the cage A 7564 Repair information 1039 ...
Page 1044: ...12 Remove the two screws A and then open the cage A 7564 Repair information 1044 ...
Page 1047: ...F E E 16 Remove the sensor transmitter 7564 Repair information 1047 ...
Page 1059: ...18 Unhook the spring A A 7564 Repair information 1059 ...
Page 1066: ...A A 7564 Repair information 1066 ...
Page 1070: ...14 Remove the E clip D and then remove the bushing D 7564 Repair information 1070 ...
Page 1075: ...16 Remove the E clip D and then remove the bushing D 7564 Repair information 1075 ...
Page 1080: ...19 Remove the E clip D and then remove the bushing D 7564 Repair information 1080 ...
Page 1083: ...25 Pry the bracket to release and then pull it 7564 Repair information 1083 ...
Page 1092: ...B A Installation note Route the cables as shown 7564 Repair information 1092 ...
Page 1093: ...3 Remove the two screws C C 4 Remove the two screws D D 7564 Repair information 1093 ...
Page 1097: ...5 Remove the E clip A from the appropriate roller A A 7564 Repair information 1097 ...
Page 1098: ...6 Remove the E clip B B B 7 Remove the roller Upper roller 1 2 7564 Repair information 1098 ...
Page 1103: ...10 Remove the four screws D D 11 Remove the four screws E E 7564 Repair information 1103 ...
Page 1110: ...10 Remove the four screws D D 11 Remove the four screws E E 7564 Repair information 1110 ...
Page 1111: ...12 Lift the front end of the plate and then remove the plate 7564 Repair information 1111 ...
Page 1112: ...13 Remove the screw F and then loosen the two screws G G F 7564 Repair information 1112 ...
Page 1117: ...16 Remove the five screws E E 7564 Repair information 1117 ...
Page 1122: ...c Align the locating pins C and screw holes D C D 7564 Repair information 1122 ...
Page 1129: ...C D C B 7564 Repair information 1129 ...
Page 1138: ...3 Remove the screw C and then remove the sensor A B C 7564 Repair information 1138 ...
Page 1141: ...Installation notes a Route the cables properly on the rear side 7564 Repair information 1141 ...
Page 1150: ...4 Remove the three screws A A 7564 Repair information 1150 ...
Page 1154: ...C D 7564 Repair information 1154 ...
Page 1161: ...B A B 3 Remove the E clip C C 7564 Repair information 1161 ...
Page 1166: ...G F 7564 Repair information 1166 ...
Page 1178: ...6 Remove the two screws C and then remove the ground screw D D C 7564 Repair information 1178 ...
Page 1192: ...5 Remove the two screws C C 7564 Repair information 1192 ...
Page 1194: ...4 Remove the two E clips A and then remove the handles A 7564 Repair information 1194 ...
Page 1198: ...3 Remove the two E clips A and then remove the handles A 7564 Repair information 1198 ...
Page 1212: ...7564 Repair information 1212 ...
Page 1235: ...10 Remove the eight E clips C and then remove the gears C C B C 7564 Repair information 1235 ...
Page 1236: ...7564 1236 ...
Page 1260: ...7564 1260 ...
Page 1265: ...3 Insert the hole punch box 4 Close door J 7564 Maintenance 1265 ...
Page 1267: ...Assembly 1 Covers 1 3 4 5 6 7 1 10 11 9 8 2 12 7564 Parts catalog 1267 ...
Page 1269: ...Assembly 2 Covers 2 2 1 3 5 6 4 10 9 8 13 12 7 11 7564 Parts catalog 1269 ...
Page 1271: ...Assembly 3 Covers 3 1 2 3 5 4 7 12 11 10 9 6 6 8 7564 Parts catalog 1271 ...
Page 1273: ...Assembly 4 Control panel 3 4 2 5 6 7 8 1 7564 Parts catalog 1273 ...
Page 1275: ...Assembly 5 Duplex 1 2 3 9 4 6 8 5 11 10 12 7 7564 Parts catalog 1275 ...
Page 1279: ...Assembly 7 Feeder 1 3 4 5 6 7 9 8 2 7564 Parts catalog 1279 ...
Page 1281: ...Assembly 8 Frame 6 1 2 4 3 5 7564 Parts catalog 1281 ...
Page 1283: ...Assembly 9 Fuser 7564 Parts catalog 1283 ...
Page 1285: ...Assembly 10 Electronics Front 3 1 6 2 5 4 8 7 7564 Parts catalog 1285 ...
Page 1287: ...Assembly 11 Electronics Rear 3 4 5 6 9 8 1 2 7 7564 Parts catalog 1287 ...
Page 1289: ...Assembly 12 Registration 1 3 5 4 6 11 2 7 8 9 10 7564 Parts catalog 1289 ...
Page 1291: ...Assembly 13 Motors 1 2 7 5 6 4 3 7564 Parts catalog 1291 ...
Page 1293: ...Assembly 14 Printhead 2 3 5 7 8 10 4 1 6 9 7564 Parts catalog 1293 ...
Page 1295: ...Assembly 15 Toner supply 10 3 5 1 2 6 4 4 7 8 9 11 11 11 4 7564 Parts catalog 1295 ...
Page 1297: ...Assembly 16 Redrive 1 3 2 7564 Parts catalog 1297 ...
Page 1299: ...Assembly 17 Transfer Front 1 2 3 4 5 6 5 8 9 10 11 11 7 12 7564 Parts catalog 1299 ...
Page 1301: ...Assembly 18 Transfer Rear 1 2 3 4 4 4 4 5 7564 Parts catalog 1301 ...
Page 1303: ...Assembly 19 ADF 1 7564 Parts catalog 1303 ...
Page 1305: ...Assembly 20 ADF 2 7564 Parts catalog 1305 ...
Page 1307: ...Assembly 21 ADF 3 7564 Parts catalog 1307 ...
Page 1309: ...Assembly 22 ADF 4 7564 Parts catalog 1309 ...
Page 1311: ...Assembly 23 ADF 5 7564 Parts catalog 1311 ...
Page 1313: ...Assembly 24 ADF 6 7564 Parts catalog 1313 ...
Page 1315: ...Assembly 25 Flatbed scanner 1 7564 Parts catalog 1315 ...
Page 1317: ...Assembly 26 Flatbed scanner 2 3 4 5 6 7564 Parts catalog 1317 ...
Page 1319: ...Assembly 27 Flatbed scanner 3 1 2 5 6 7 3 4 7564 Parts catalog 1319 ...
Page 1321: ...Assembly 28 550 sheet tray 1 2 7564 Parts catalog 1321 ...
Page 1323: ...Assembly 29 550 sheet tray Rear 7564 Parts catalog 1323 ...
Page 1325: ...Assembly 30 550 sheet tray Front 9 2 2 10 11 5 7 8 3 4 6 1 12 7564 Parts catalog 1325 ...
Page 1327: ...Assembly 31 2200 sheet tray 1 2 3 4 7564 Parts catalog 1327 ...
Page 1329: ...Assembly 32 2200 sheet tray Front 1 7 3 4 5 6 2 9 1 8 7564 Parts catalog 1329 ...
Page 1331: ...Assembly 33 2200 sheet tray Rear 7564 Parts catalog 1331 ...
Page 1333: ...Assembly 34 Caster base 2 3 3 3 2 1 7564 Parts catalog 1333 ...
Page 1338: ...7564 Parts catalog 1338 ...
Page 1342: ...7564 Parts catalog 1342 ...
Page 1343: ...Assembly 39 Staple finisher option 1 7564 Parts catalog 1343 ...
Page 1345: ...Assembly 40 Staple finisher Covers 8 3 4 5 1 2 1 1 6 7 7564 Parts catalog 1345 ...
Page 1347: ...Assembly 41 Staple finisher Front 4 3 2 5 6 7 8 9 10 7564 Parts catalog 1347 ...
Page 1349: ...Assembly 42 Staple finisher Electrical 6 1 2 4 3 5 7564 Parts catalog 1349 ...
Page 1351: ...Assembly 43 Staple finisher Rear 1 2 3 5 6 4 7 7564 Parts catalog 1351 ...
Page 1353: ...Assembly 44 Staple finisher Tamper 1 2 2 3 3 4 5 6 7 8 9 11 10 7564 Parts catalog 1353 ...
Page 1355: ...Assembly 45 Staple finisher Transport 4 5 6 6 7 8 1 3 2 7564 Parts catalog 1355 ...
Page 1357: ...Assembly 46 Staple finisher Bottom 7564 Parts catalog 1357 ...
Page 1359: ...Assembly 47 Mailbox 1 M1 M2 1 7564 Parts catalog 1359 ...
Page 1361: ...Assembly 48 Mailbox 2 7564 Parts catalog 1361 ...
Page 1363: ...Assembly 49 Mailbox 3 7564 Parts catalog 1363 ...
Page 1365: ...Assembly 50 Mailbox 4 1 2 3 4 6 7 8 9 5 7564 Parts catalog 1365 ...
Page 1367: ...Assembly 51 Mailbox 5 7564 Parts catalog 1367 ...
Page 1369: ...Assembly 52 HPT 1 7564 Parts catalog 1369 ...
Page 1371: ...Assembly 53 HPT 2 7564 Parts catalog 1371 ...
Page 1373: ...Assembly 54 HPT 3 7564 Parts catalog 1373 ...
Page 1375: ...Assembly 55 HPT 4 7564 Parts catalog 1375 ...
Page 1377: ...Assembly 56 HPT 5 7564 Parts catalog 1377 ...
Page 1379: ...Assembly 57 MSHPF covers 1 1 2 3 4 5 6 7 8 15 9 10 12 11 13 14 7564 Parts catalog 1379 ...
Page 1381: ...Assembly 58 MSHPF covers 2 7564 Parts catalog 1381 ...
Page 1383: ...Assembly 59 MSHPF electronics 2 4 6 3 5 7 8 1 7564 Parts catalog 1383 ...
Page 1385: ...Assembly 60 MSHPF mid transport drive 2 1 3 8 12 7 6 5 10 13 11 9 4 7564 Parts catalog 1385 ...
Page 1387: ...Assembly 61 MSHPF mid transport paper path 6 1 4 3 1 2 9 5 7 8 7564 Parts catalog 1387 ...
Page 1389: ...Assembly 62 MSHPF offset drive 2 1 3 4 7564 Parts catalog 1389 ...
Page 1391: ...Assembly 63 MSHPF standard bin 1 8 7 5 6 3 4 2 1 7564 Parts catalog 1391 ...
Page 1393: ...Assembly 64 MSHPF standard bin 2 4 3 5 7 8 9 6 2 1 7564 Parts catalog 1393 ...
Page 1399: ...Assembly 67 MSHPF staging paper path 1 5 7 8 9 10 3 4 2 6 11 7564 Parts catalog 1399 ...
Page 1403: ...Assembly 69 MSHPF compiler 2 2 3 4 2 5 6 1 7564 Parts catalog 1403 ...
Page 1405: ...Assembly 70 MSHPF tamper 2 1 3 8 4 5 5 6 9 7 7564 Parts catalog 1405 ...
Page 1407: ...Assembly 71 MSHPF carriage transport 10 11 7 8 9 1 2 3 4 5 6 7564 Parts catalog 1407 ...
Page 1409: ...Assembly 72 MSHPF door interlock 1 3 2 7564 Parts catalog 1409 ...
Page 1411: ...Assembly 73 MSHPF stapler bin 1 1 5 4 3 3 2 6 7 8 7564 Parts catalog 1411 ...
Page 1413: ...Assembly 74 MSHPF stapler bin 2 1 2 5 3 4 7564 Parts catalog 1413 ...
Page 1415: ...Assembly 75 MSHPF stapler bin 3 2 8 3 4 7 1 4 5 6 7564 Parts catalog 1415 ...
Page 1417: ...Assembly 76 MSHPF cabinet 3 1 1 3 4 4 5 5 7 7 8 8 2 6 7564 Parts catalog 1417 ...
Page 1420: ...7564 1420 ...
Page 1464: ...Multiple sheets Single sheet thick 7564 Appendix C Theory of operation 1464 ...
Page 1506: ...7564 1506 ...
Page 1520: ...7564 Index 1520 ...
Page 1540: ...7564 Part number index 1540 ...
Page 1560: ...7564 Part name index 1560 ...