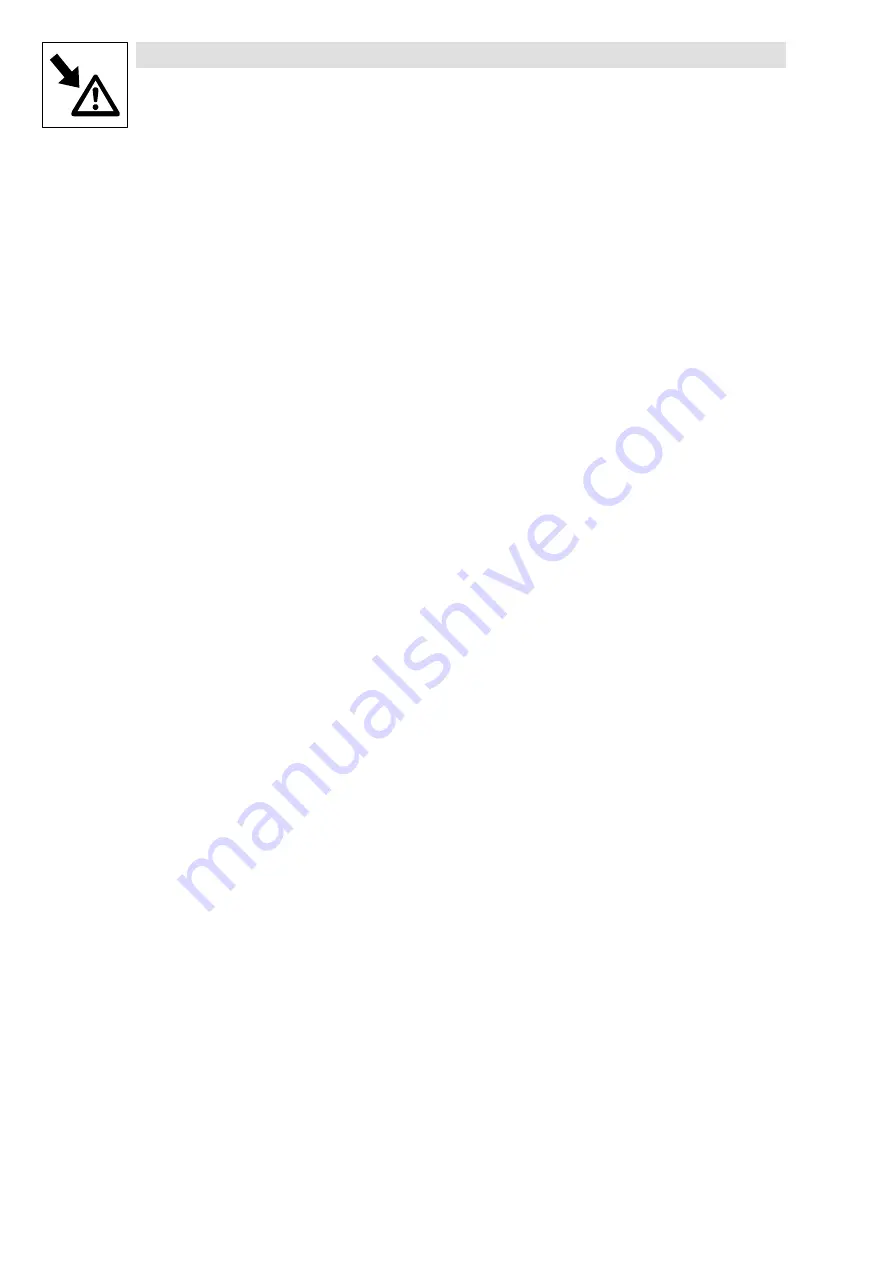
Safety information
Lenze low-voltage machinery
4
l
EDK82EVXXX EN 2.0
Electrical connection
All operations must only be carried out by qualified and skilled personnel when the low-voltage
machine is at standstill and when the machine is de-energized and protected against unintentional
restart. This also applies to auxiliary circuits (e.g. brake, encoder, separate fan).
Check safe isolation from the supply!
If the tolerances in EN 60034-1; IEC 34 (VDE 0530-1) - voltage ±5 % , frequency ±2 % , wave form,
symmetry - are exceeded, more heat will be generated and the electromagnetic compatibility will
be influenced.
Observe the indications on the nameplate, operating notes, and the connection diagram in the
terminal box.
The connection must ensure a continuous and safe electrical supply (no loose wire ends); use
appropriate cable terminals. The connection to the PE conductor must be safe. The plug-in
connector must be bolt tightly (to stop).
The clearances between blank, live parts and earth must not fall below 8 mm at V
r
≤
550 V, 10 mm
at V
r
≤
725 V, 14 mm at V
r
≤
1000 V.
The terminal box must be clean and dry; foreign particles, dirt and moisture disturb operation. All
unused cable entries and the box itself must be sealed against dust and water. For the trial run
without output elements, lock the key. Check brake operation before commissioning of low-voltage
machines with brakes.
Operation
Vibration severities v
rms
≤
3.5 mm/s (P
r
≤
15 kW) and 4.5 mm/s (P
r
> 15 kW) are acceptable when
the clutch is activated. If deviations from normal operation occur, e.g. increased temperatures,
noises, vibrations, find the cause and, if necessary, contact the manufacturer. Switch off the
machine in problematic situations.
If the drive is exposed to dirt, clean it regularly.
Do not switch off the protection devices, not even for trial runs.
Integrated temperature sensors do not provide full protection. If necessary, limit the maximum
current. Connect the function blocks to the option switch-off after several seconds of operation at
I > I
r
, especially if blocking may occur.
Shaft seals and bearings have a limited service life.
Regrease the bearings using the relubrication facility while the low-voltage machine is running.
Observe the saponification number. If the grease drain hole is sealed with a plug (IP54 drive end;
IP23 drive end and non-drive end), remove the plug before commissioning. Seal the bore holes with
grease. Replace the prelubricated bearings (2Z bearings) after approx. 10,000 h - 20,000 h, at the
latest however after 3 - 4 years. Observe the manufacturer’s Instructions.