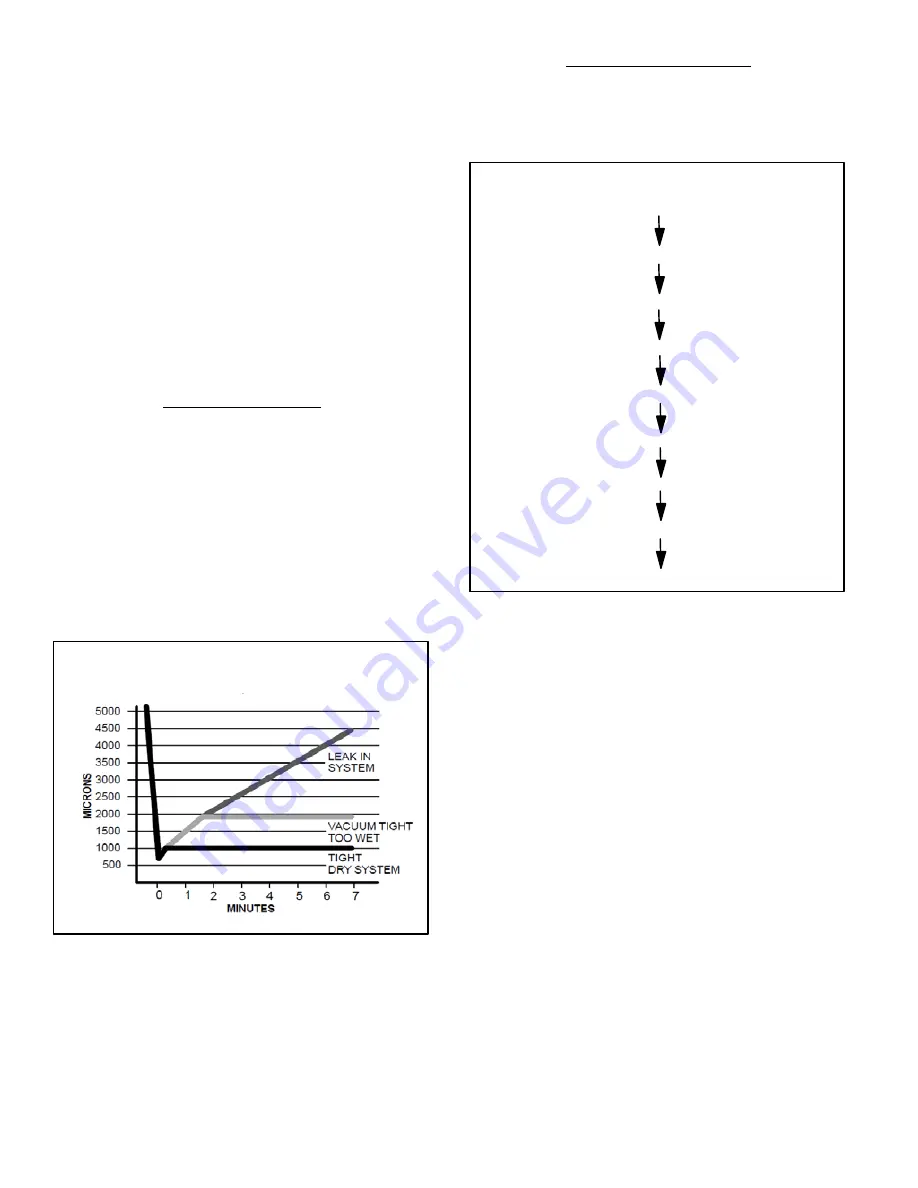
Page 20
EVACUATE LINE SET AND INDOOR COIL
The unit is shipped with a factory refrigerant charge. The
liquid and suction line valves were closed after final testing
at the factory. Do not operate these valves until the line set
and indoor coil have been evacuated and leak checked, or
the charge is lost.
NOTE -
Do not use any portion of the factory charge for
purging or leak testing. The factory charge is for filling the
system only after a complete evacuation and leak check
has been performed.
Line set and indoor coil should be evacuated using the re
commend deep vacuum method of 500 microns. If deep
vacuum equipment is not available, the alternate triple
evacuation method may be used by following the specified
procedure.
If vacuum must be interrupted during the evacuation pro
cedure, always break vacuum with dry nitrogen.
Deep Vacuum Method
The deep vacuum method requires a vacuum pump cap
able of pulling a vacuum to 500 microns and a vacuum
gauge capable of accurately measuring this vacuum level.
The deep vacuum method is the most positive way of as
suring a system is free of air and water.
Watch the vacuum gauge as the system is pulling down.
The response of the gauge is an indicator of the condition
of the system (refer to figure 19).
With no leaks in the system, allow the vacuum pump to run
for 30 minutes minimum at the deep vacuum level.
Deep Vacuum Gauge Response and
System Conditions
FIGURE 19
Triple Evacuation Method
The triple evacuation method should only be used when
system does not contain any water in liquid form and vacu
um pump is only capable of pulling down to 28 inches of
mercury (711mm Hg). Refer to figure 20 and proceed as
follows:
EVACUATE
BREAK VACUUM WITH DRY NITROGEN
WAIT
BREAK VACUUM WITH DRY NITROGEN
WAIT
EVACUATE
CHECK FOR TIGHT, DRY SYSTEM (IF IT HOLDS DEEP VACUUM)
CHARGE SYSTEM
Triple Evacuation Sequence
EVACUATE
FIGURE 20
1. Pull system down to 28 inches of mercury (711mm Hg)
and allow pump to continue operating for an additional
15 minutes.
2. Close manifold valves or valve at vacuum pump and
shut-off vacuum pump.
3. Connect a nitrogen cylinder and regulator to system
and fill with nitrogen until system pressure is 2 psig.
4. Close nitrogen valve and allow system to stand for one
hour. During this time, dry nitrogen will diffuse
throughout the system absorbing moisture.
5. Repeat this procedure as indicated in figure 20.
6. After the final evacuate sequence, confirm there are
no leaks in the system. If a leak is found, repeat the en
tire process after repair is made.
7. Reconnect the manifold gauge to the vacuum pump,
turn the pump on, and continue to evacuate the line set
and indoor unit until the absolute pressure does not
rise above 500 microns (29.9 inches of mercury) within
a 20
*
minute period after shutting off the vacuum
pump and closing the manifold gauge valves.