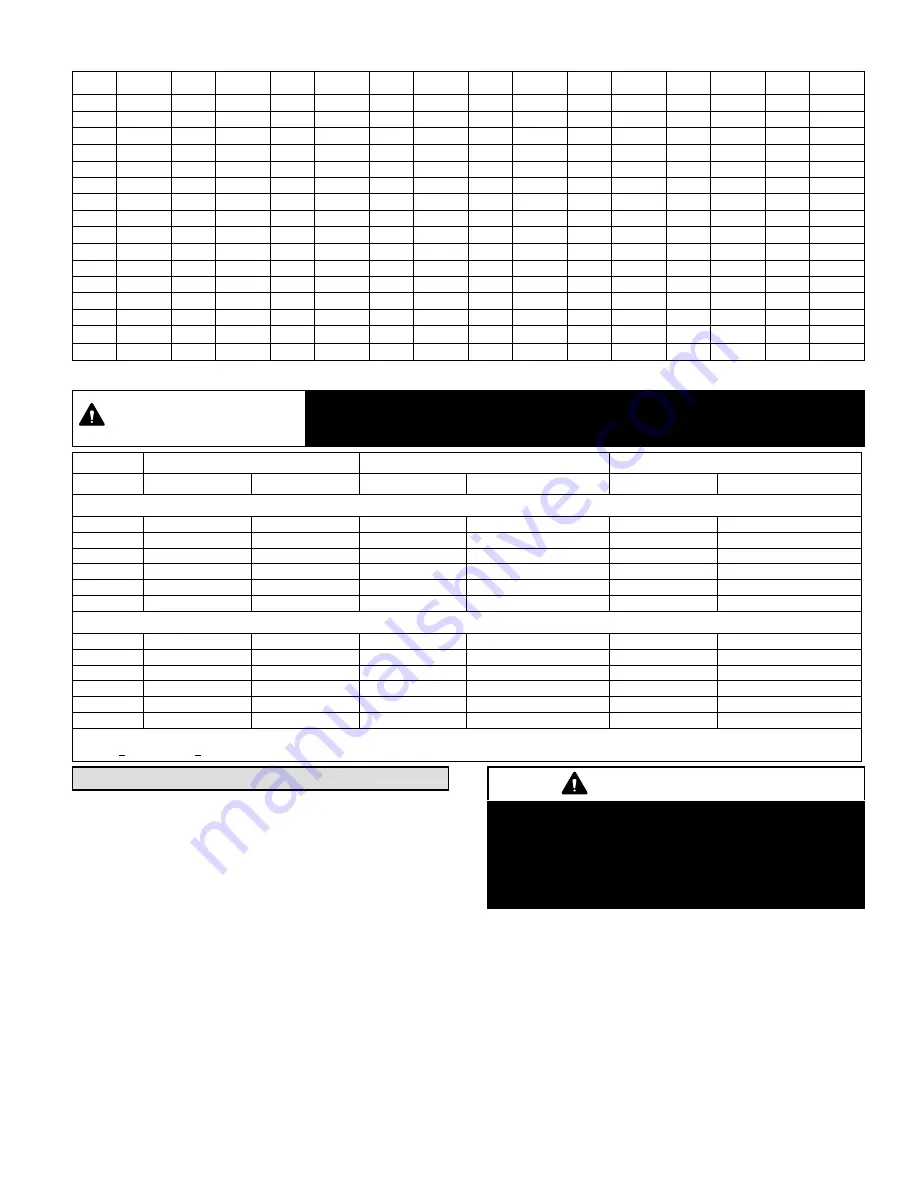
Page 25
SSB*H4 SERIES
Table 3. HFC-410A Temperature (°F) - Pressure (Psig)
°F
Psig
°F
Psig
°F
Psig
°F
Psig
°F
Psig
°F
Psig
°F
Psig
°F
Psig
32
100.8
48
137.1
63
178.5
79
231.6
94
290.8
110
365.0
125
445.9
141
545.6
33
102.9
49
139.6
64
181.6
80
235.3
95
295.1
111
370.0
126
451.8
142
552.3
34
105.0
50
142.2
65
184.3
81
239.0
96
299.4
112
375.1
127
457.6
143
559.1
35
107.1
51
144.8
66
187.7
82
242.7
97
303.8
113
380.2
128
463.5
144
565.9
36
109.2
52
147.4
67
190.9
83
246.5
98
308.2
114
385.4
129
469.5
145
572.8
37
111.4
53
150.1
68
194.1
84
250.3
99
312.7
115
390.7
130
475.6
146
579.8
38
113.6
54
152.8
69
197.3
85
254.1
100
317.2
116
396.0
131
481.6
147
586.8
39
115.8
55
155.5
70
200.6
86
258.0
101
321.8
117
401.3
132
487.8
148
593.8
40
118.0
56
158.2
71
203.9
87
262.0
102
326.4
118
406.7
133
494.0
149
601.0
41
120.3
57
161.0
72
207.2
88
266.0
103
331.0
119
412.2
134
500.2
150
608.1
42
122.6
58
163.9
73
210.6
89
270.0
104
335.7
120
417.7
135
506.5
151
615.4
43
125.0
59
166.7
74
214.0
90
274.1
105
340.5
121
423.2
136
512.9
152
622.7
44
127.3
60
169.6
75
217.4
91
278.2
106
345.3
122
428.8
137
519.3
153
630.1
45
129.7
61
172.6
76
220.9
92
282.3
107
350.1
123
434.5
138
525.8
154
637.5
46
132.2
62
175.4
77
224.4
93
286.5
108
355.0
124
440.2
139
532.4
155
645.0
47
134.6
78
228.0
109
360.0
140
539.0
Table 4. Normal Operating Pressures (10 and S5 psig)
IMPORTANT
Use this table to perform maintenance checks; it is not a procedure for charging the system. Minor variations
in these pressures may be due to differences in installations. Significant deviations could mean that the
system is not properly charged or that a problem exists with some component in the system.
Model
SSB036H4S4
SSB048H4S4
SSB060H4S4
5
F (
5
C)*
Liquid
Suction
Liquid
Suction
Liquid
Suction
First Stage (Low Capacity)
65 (18)
217
141
229
140
229
134
75 (24)
251
143
263
143
264
138
85 (29)
292
146
304
146
305
140
95 (35)
337
147
350
148
349
142
105 (41)
387
150
400
150
402
147
115 (46)
440
154
453
155
455
149
Second Stage (High Capacity)
65 (18)
230
137
234
135
244
129
75 (24)
265
140
269
137
282
131
85 (29)
307
141
312
140
324
133
95 (35)
354
144
359
141
371
136
105 (41)
405
146
409
143
422
139
115 (46)
460
149
465
146
474
143
*Temperature of air entering outdoor coil.
**(10 psig; Vapor +5 psig) Typical pressures; indoor unit match up, indoor air quality equipment, and indoor load will cause the pressures to vary.
System Operation
SECOND-STAGE OPERATION
If the demand defrost control (A108) receives a call for
second-stage compressor operation Y2 in heating or
cooling mode and the first‐stage compressor output is
active, the second‐stage compressor solenoid output will
be energized.
If first‐stage compressor output is active in heating mode
and the outdoor ambient temperature is below the selected
compressor lock-in temperature, the second‐stage
compressor solenoid output will be energized without the
Y2 input. If the jumper is not connected to one of the
temperature selection pins on
P3
(40, 45, 50, 55°F), the
default lock-in temperature of 40°F (4.5°C) will be used.
IMPORTANT
Some scroll compressor have internal vacuum protector
that will unload scrolls when suction pressure goes
below 20 psig. A hissing sound will be heard when the
compressor is running unloaded. Protector will reset
when low pressure in system is raised above 40 psig. DO
NOT REPLACE COMPRESSOR.