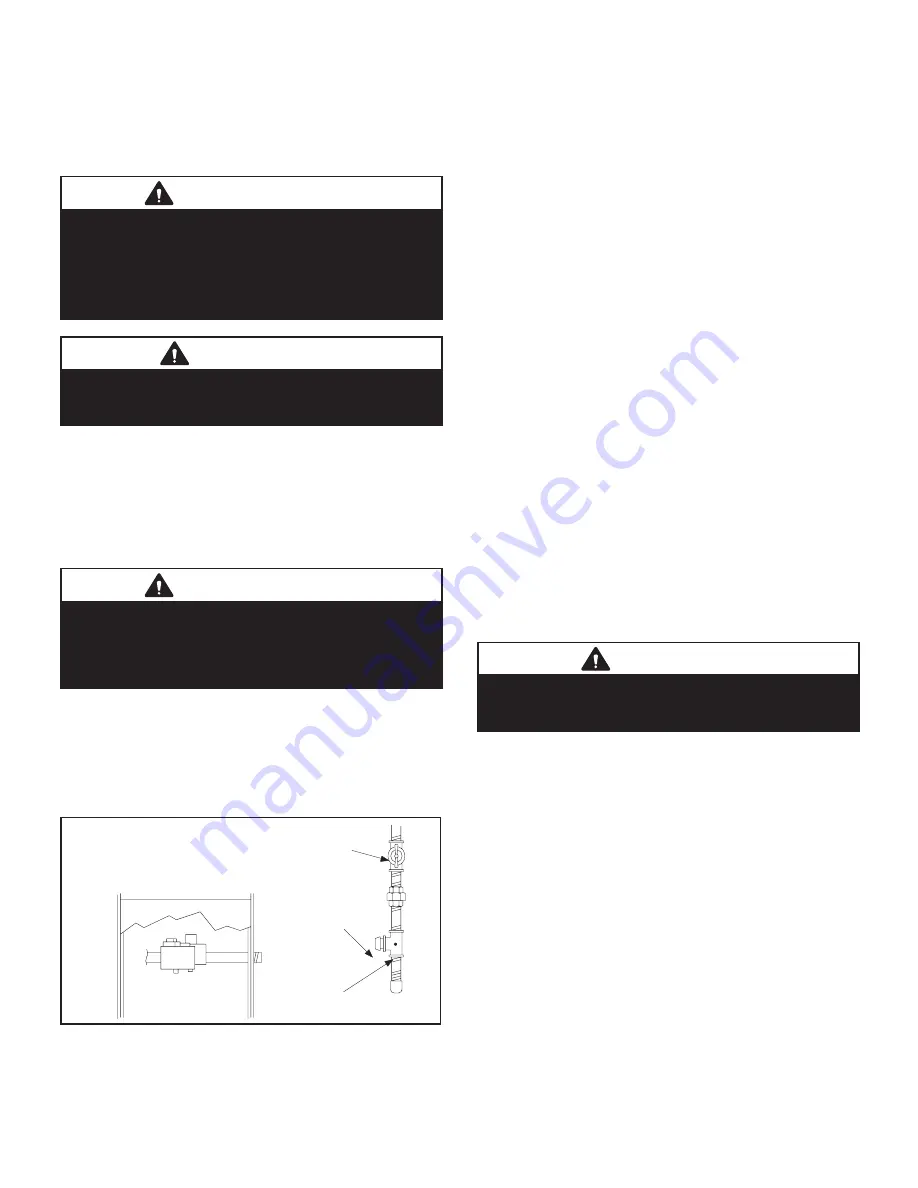
Page 38
IV-HEATING SYSTEM SERVICE CHECKS
A-CSA Certification
All units are CSA design certified without modifications.
Refer to the SL280DFV Installation Instruction.
B-Gas Piping
IMPORTANT
If a flexible gas connector is required or allowed by
the authority that has jurisdiction, black iron pipe
shall be installed at the gas valve and extend outside
the furnace cabinet. The flexible connector can then
be added between the black iron pipe and the gas
supply line.
WARNING
Do not over torque (800 in-lbs) or under torque (350
in-lbs) when attaching the gas piping to the gas
valve.
Gas supply piping should not allow more than 0.5”W.C.
drop in pressure between gas meter and unit. Supply gas
pipe must not be smaller than unit gas connection.
Compounds used on gas piping threaded joints should be
resistant to action of liquefied petroleum gases.
C-Testing Gas Piping
IMPORTANT
In case emergency shutdown is required, turn off the
main shut-off valve and disconnect the main power
to unit. These controls should be properly labeled
by the installer.
When pressure testing gas lines, the gas valve must be
disconnected and isolated. Gas valves can be damaged
if subjected to more than 0.5 psig (14” W.C.). See FIG-
URE 19. If the pressure is equal to or less than 0.5psig
(14”W.C.), use the manual shut-off valve before pressure
testing to isolate furnace from gas supply.
MANUAL MAIN SHUT-OFF VALVE
WILL NOT HOLD TEST PRESSURE
IN EXCESS OF 0.5 PSIG (14”W.C.)
GAS VALVE
CAP
GAS PIPING TEST PROCEDURE
FIELD PROVIDED
LINE PRESSURE TAP
FIGURE 19
When checking piping connections for gas leaks, use
preferred means. Kitchen detergents can cause harmful
corrosion on various metals used in gas piping. Use of a
specialty Gas Leak Detector is strongly recommended. It
is available through Lennox under part number 31B2001.
See Corp. 8411-L10, for further details.
Do not use matches, candles, flame or any other source of
ignition to check for gas leaks.
D-Testing Gas Supply Pressure
White Rodgers Gas Valve
An inlet post located on the gas valve provides access to
the supply pressure. See FIGURE 17. Back out the 3/32
hex screw one turn, connect a piece of 5/16 tubing and
connect to a manometer to measure supply pressure. See
TABLE 20 for supply line pressure.
Honeywell / ResideoGas Valve
A threaded plug on the inlet side of the gas valve provides
access to the supply pressure tap. Remove the threaded
plug, install a field-provided barbed fitting and connect a
manometer to measure supply pressure. See TABLE 20
for supply line pressure. Replace the threaded plug after
measurements have been taken.
E-Check Manifold Pressure
After line pressure has been checked and adjusted, check
manifold pressure. Move pressure gauge to outlet pres-
sure tap located on unit gas valve (GV1). Checks of man-
ifold pressure are made as verification of proper regulator
adjustment.
Manifold pressure can be measured at any time the gas
valve is open and is supplying gas to the unit. See TABLE
20 for normal operating manifold pressure.
CAUTION
For safety, connect a shut\-off valve between the
manometer and the gas tap to permit shut off of gas
pressure to the manometer.
The gas valve is factory set and should not require adjust-
ment. All gas valves are factory regulated.
Manifold Adjustment Procedure:
1 - Connect test gauge to manifold pressure post
(FIGURE 17) or tap (FIGURE 18) on gas valve.
2 - Ignite unit on low fire and let run for 5 minutes to
allow for steady state conditions.
3 - After allowing unit to stabilize for 5 minutes, record
manifold pressure and compare to value given in
4 - If necessary, make adjustments. FIGURE 17 and
FIGURE 18 show location of high fire and low fire
adjustment screw.
5 - Repeat steps 2, 3 and 4 on high fire.
6 - Shut unit off and remove manometer as soon as an
accurate reading has been obtained. Take care to
replace pressure tap plug.
7 - Start unit and perform leak check. Seal leaks if
found.