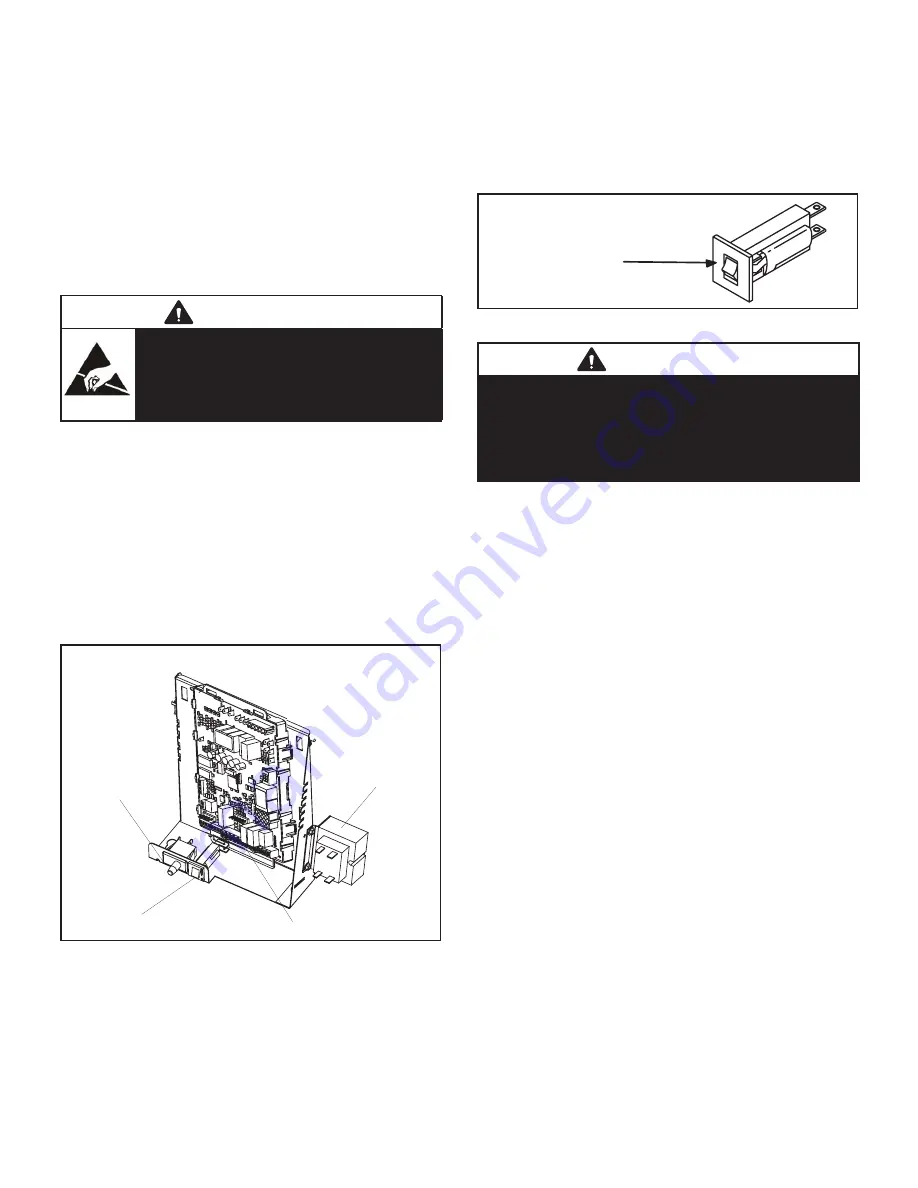
Page 6
I-UNIT COMPONENTS
SL280DFNV unit components are shown in FIGURE 1.
The gas valve, combustion air inducer and burners can be
accessed by removing the access panel. Electrical com
-
ponents are in the control box (FIGURE 2) found in the
blower section.
SL280DFNV units are factory equipped with a bottom re-
turn air panel in place. The panel is designed to be field
removed as required for bottom air return. Markings are
provided for side return air and may be cut out in the field
.
ELECTROSTATIC DISCHARGE (ESD)
Precautions and Procedures
CAUTION
Electrostatic discharge can affect
electronic components. Take precautions
to neutralize electrostatic charge by
touching your hand and tools to metal
prior to handling the control.
A- Control Box
1. Control Transformer (T1)
A transformer located in the control box provides pow-
er tothe low voltage section of the unit. Transformers on
allmodels are rated 40VA with a 120V primary and a 24V
secondary.
2. Door Interlock Switch (S51)
A door interlock switch rated 14A at 125VAC is wired in se
-
ries with line voltage. When the inner blower access panel
is removed the unit will shut down.
CONTROL BOX
SureLight
®
Integrated Control
Interlock Switch
Transformer
Circuit Breaker
FIGURE 2
3. Circuit Breaker (CB8)
A 24V circuit breaker is also located in the control box.
The switch provides overcurrent protection to the trans-
former (T1). The breaker is rated 3A at 32V. If the current
exceeds this limit the breaker will trip and all unit opera-
tion will shutdown. The breaker can be manually reset by
pressing the button on the face. See FIGURE 3
.
CIRCUIT BREAKER CB8
PRESS TO RESET
FIGURE 3
WARNING
Shock hazard.
Disconnect power before servicing. Integrated
control is not field repairable. If control is
inoperable, simply replace entire control.
Can cause injury or death. Unsafe operation will
result if repair is attempted.
4. Integrated Control (A92)
Units are equipped with the communicating enabled Sure-
Light
®
two-stage, variable speed integrated control. This
control is used with any communicating enabled thermo-
stat as part of a communicating comfort system. The con-
trol can also operate with a non-communicating conven-
tional single or two-stage thermostat. The system consists
of a ignition / blower control (FIGURE 4) with control pin
designations in TABLE 1, TABLE 2, TABLE 3 and ignitor
(FIGURE 13).
The control and ignitor work in combination to ensure fur-
nace ignition and ignitor durability. The control provides
gas ignition, safety checks and indoor blower control with
two-stage gas heating.
The furnace combustion air inducer, gas valve and indoor
blower are controlled in response to various system inputs
such as thermostat signal, pressure and limit switch signal
and flame signal. The control features a seven-segment
LED display, indicating furnace status (including indoor
blower) and error codes. The LED flashes in single dig
-
its. For example using table 5 under LIMIT CODE, an “E”
followed by “2” followed by “5” followed by “0”, the limit
switch circuit is open. The control also has two unpowered
(dry) 1/4” contacts for a humidifier and a 120 volt accesso
-
ry terminal. Both rated at (1) one amp each.
Electronic Ignition
At the beginning of the heat cycle the integrated control
monitors the first stage and second stage combustion air
inducer prove switch. The control will not begin the heating
cycle if the first stage prove switch is closed (by-passed).
Likewise the integrated control will not begin the second
stage heating cycle if the second stage prove switch is
closed, and will remain in first stage heat. However, if the
second stage prove switch closes during the first stage
heat pre-purge, the control will allow second stage heat.