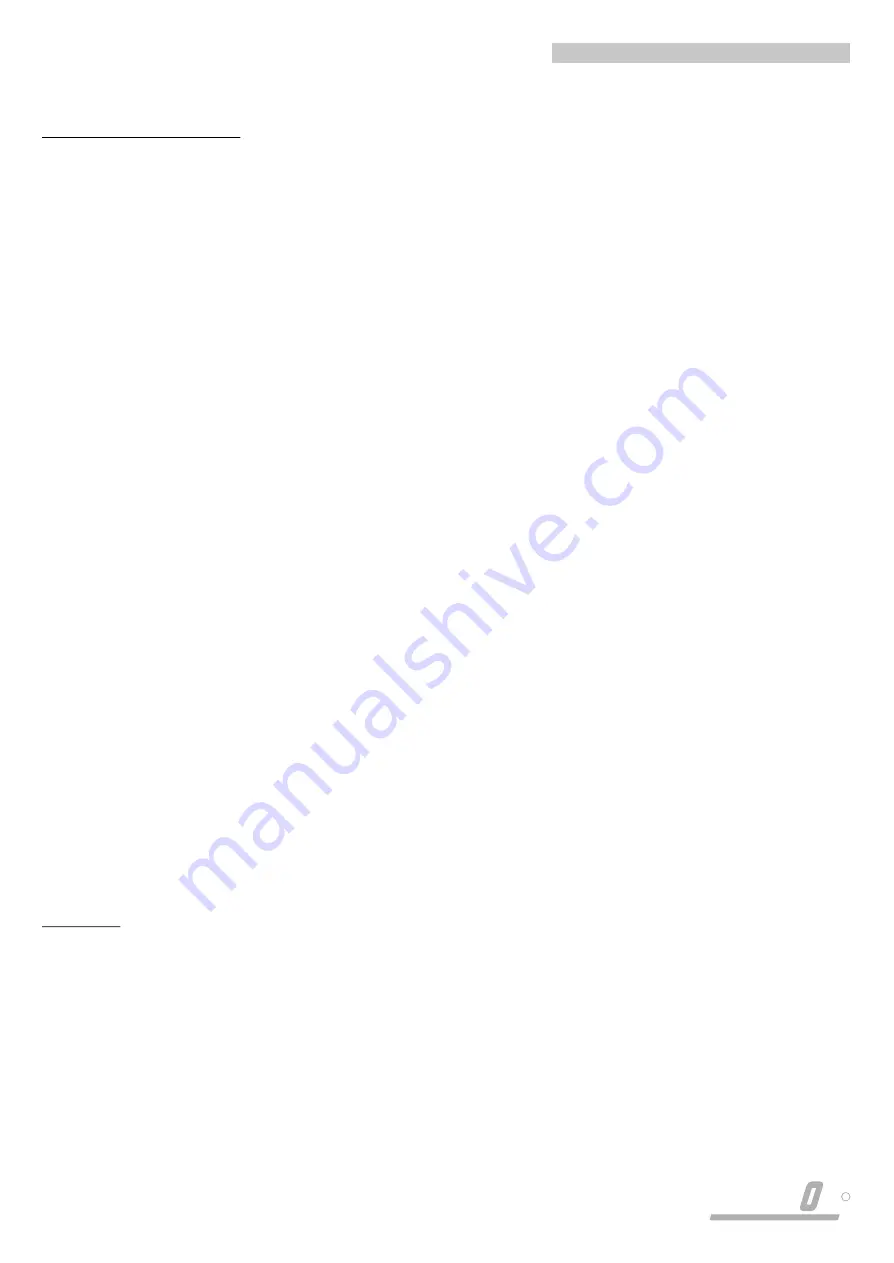
ELECTRICAL CONNECTIONS
ISOLATE ELECTRICAL SUPPLY BEFORE
ATTEMPTING SERVICE WORK.
A 230V, 50Hz, single phase supply is required. Wiring
must be installed by a qualified electrician and conform
to current local and national regulations.
1.
Wire mains to unit via a double pole isolating switch,
fused to IEE regulation. Refer to diagrams indicating
electrical wiring details.
2.
The electrical connection is via a 2m flying lead with
factory fitted connector into socket on control box
where an electric heater is NOT fitted. If an electric
heater is fitted, to connect mains supply to unit,
slacken off the screw holding the control box front
cover. Carefully pivot the cover to support it, making
sure the wires connecting the cover to the unit are not
strained. Connect the mains lead via grommet hole
in the side panel to the LIVE, NEUTRAL and EARTH
positions on the 12-way terminal block. Replace
cover and tighten screw.
3.
If a Condensate Lift Pump is specified, this w i l l b e
pre-wired back to the control box, but the pump
assembly will be taped to the unit and must be fixed to
the end of the drip tray before installing the unit, using
the screws supplied.
4.
The fan motors are of the permanent split capacitor
type and have a capacitor fixed to the outside of the
motor. All motors have thermal overload protection
as standard. Access to the fan tray is via removable
panels on the bottom face of the unit.
CONTROLS
All units are fitted as standard with an ON/OFF switch and
a FAN SPEED selector switch for three speeds.
When specified, the water control valves will have a
controller that will be fitted to the exterior of the control
box.
These are all fitted into the control box and pre-wired.
1. Fan Speed
Out of 6 speeds available, SL (Super Low), EL(Extra Low),
L(Low), ML(Med/Low), M(Med), and H(High), the fan
speed selector switch will be wired for three speeds.
Speed adjustment and fine tuning is achieved by
following the instructions indicated on the label that is
positioned on the underside of the unit, adjacent to the
control box.
Each model size has its specific settings, examples as
detailed on page 5 of this document.
An example of adjusting the speed setting is described
below:-
E.g.:
If unit is selected for Medium/Low (ML) speed,
then the speed selector switch is set at position II and
other positions L and M, as below:
Position I
=
L (Low Speed)
Position II
=
ML(Med/LowSpeed)
Position III
=
M (Medium Speed)
If selected speed is EL then this would be Position II with
SL and L other positions. If selected speed is H then this
would be posiition III with M and ML other positions.
ELECTRICAL CONNECTIONS / CONTROLS
R
LENN X
4