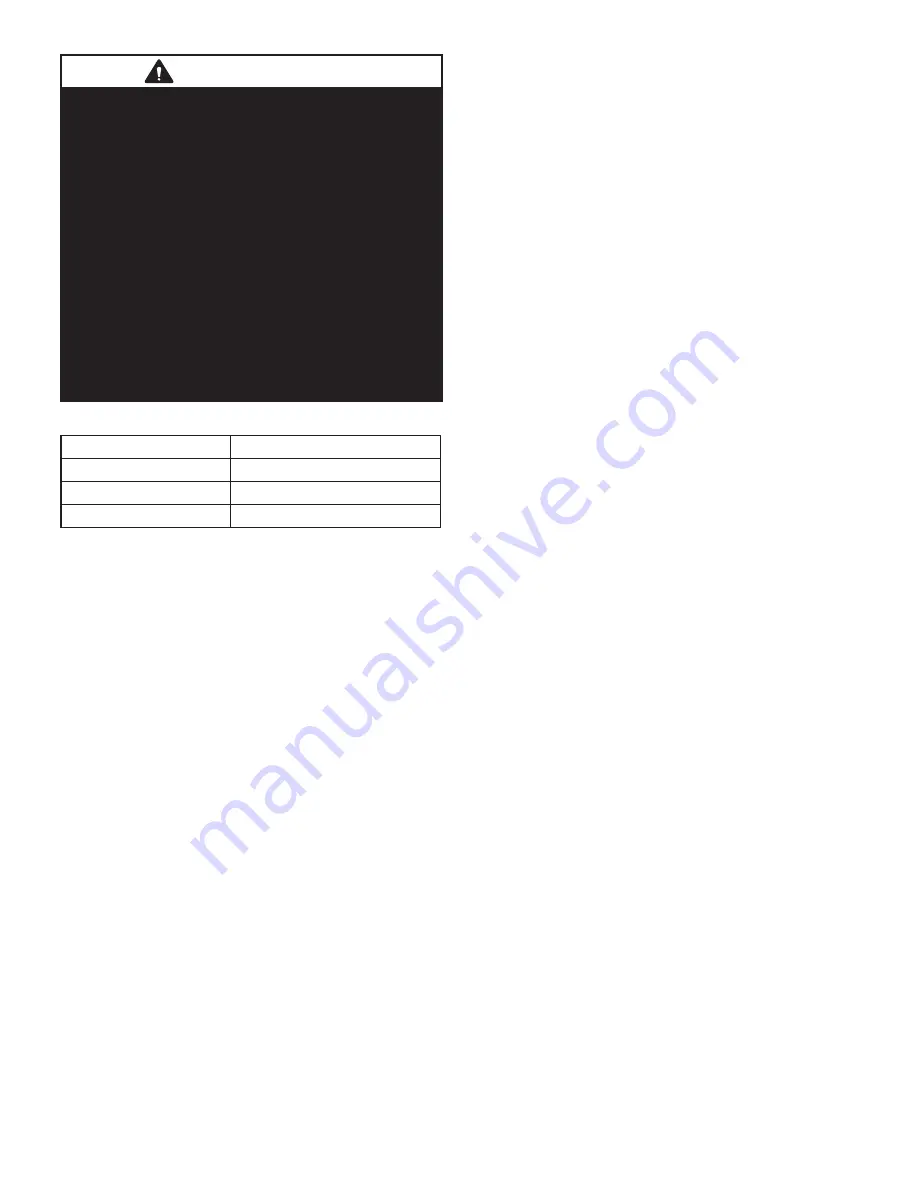
Page 24
IMPORTANT
If a highefficiency filter is being installed as part
of this system to ensure better indoor air quality,
the filter must be properly sized. Highefficiency
filters have a higher static pressure drop than
standardefficiency glass/foam filters. If the pressure
drop is too great, system capacity and performance
may be reduced.
The pressure drop may also cause the limit to trip
more frequently during the winter and the indoor
coil to freeze in the summer, resulting in an increase
in the number of service calls.
Before using any filter with this system, check the
specifications provided by the filter manufacturer
against the data given in the appropriate Lennox
Product
Specifications
bulletin.
Additional
information is provided in Service and Application
Note ACC002 (August 2000).
TABLE 15
Furnace Cabinet Width
Filter Size (inches)
A - 14-1/2”
14 X 25 X 1 (1)
B - 17-1/2”
16 X 25 X 1 (1)
C - 21”
20 x 25 x 1 (1)
5 - Check the condition and cleanliness of burners and
heat exchanger and clean if necessary.
6 - Check the cleanliness of blower assembly and
clean the housing, blower wheel and blower motor
if necessary. The blower motors are prelubricated
for extended bearing life. No further lubrication is
needed.
7 - Inspect the combustion air inducer and clean if
necessary.
8 -
Evaluate the heat exchanger integrity by inspecting
the heat exchanger per the AHRI heat exchanger
inspection procedure. This procedure can be
viewed at www.ahrinet.org
9 - Ensure sufficient combustion air is available to the
furnace. Fresh air grilles and louvers (on the unit
and in the room where the furnace is installed)
must be properly sized, open and unobstructed to
provide combustion air.
10 -
Inspect the furnace venting system to make sure
it is in place, structurally sound, and without holes,
corrosion, or blockage. Vent system must be free
and clear of obstructions and must slope upward
away from the furnace . Vent system should be
installed per the National Fuel Gas Code
11 -
Inspect the furnace return air duct connection to
ensure the duct is sealed to the furnace. Check for
air leaks on supply and return ducts and seal where
necessary.
12 - Check the condition of the furnace cabinet insulation
and repair if necessary.
13 - Perform a complete combustion analysis during the
furnace inspection to ensure proper combustion
and operation. Consult Service Literature for proper
combustion values.
14 - Verify operation of CO detectors and replace
batteries as required.
Perform a general system test. Turn on the furnace to
check operating functions such as the start-up and shut-
off operation.
1 -
Check the operation of the ignition system, inspect
and clean flame sensor. Check microamps before
and after. Check controls and safety devices (gas
valve, flame sensor, temperature limits). Consult
Service Manual for proper operating range. Thermal
Limits should be checked by restricting airflow and
not disconnecting the indoor blower. For additional
details, please see Service and Application Note
H049.
2 - Verify that system total static pressure and airflow
settings are within specific operating parameters.
3 - Clock gas meter to ensure that the unit is operating
at the specified firing rate. Check the supply
pressure and the manifold pressure. On two-stage
gas furnaces check the manifold pressure on high
fire and low fire. If manifold pressure adjustment is
necessary, consult the Service Literature for unit
specific information on adjusting gas pressure.
Not all gas valves are adjustable. Verify correct
temperature rise.