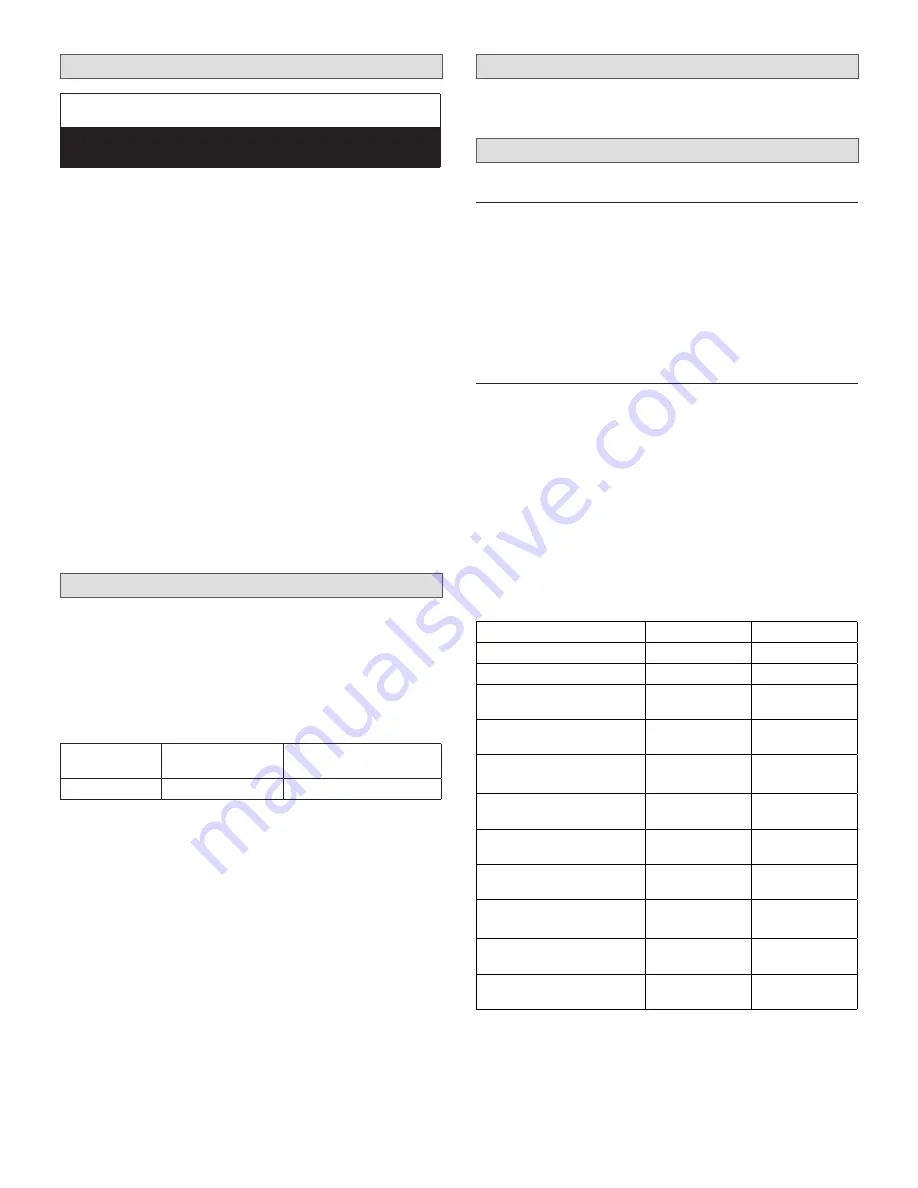
17
Unit Start-Up
IMPORTANT
Units should be energized 24 hours before unit start-up
to prevent compressor damage as a result of slugging.
1.
Inspect all factory- and field-installed wiring for loose
connections.
2. Verify that the manifold gauge set is connected.
3. Add additional refrigerant charge if required before
opening valves and while system is still under a
vacuum.
4.
Open the liquid and gas line service valves to release
the refrigerant charge contained in outdoor unit into
the system.
5. Replace the stem caps and tighten to the value listed
in “Table 4. Flare Nut Torque Recommendations” on
page 12.
6. Check voltage supply at the outdoor unit terminal strip.
The voltage must be within the range listed on the
unit’s nameplate. If not, do not start the equipment
until you have consulted with the power company and
the voltage condition has been corrected.
7. Refer to the included user guide to operate the system
using the provided remote control.
8. Visually check for binding of both indoor and outdoor
fans.
Adding Refrigerant for Longer Line Set
The outdoor unit is factory-charged with refrigerant.
Calculate the additional refrigerant required according to
the diameter and the length of the liquid pipe between the
outdoor unit and indoor unit connections.
Be sure to add the proper amount of additional refrigerant.
Failure to do so may result in reduced performance.
Table 8.
Additional Refrigerant Charge
System Size
(KBtu)
Pipe Length
(feet / meters)
Amount of Refrigerant
to add
12
>25 (7.5)
0.161 oz/ft (15g/m)
Troubleshooting
See “Error Codes” on page 19 for details on
troubleshooting.
Test Run
Pre-Checks
Only perform test run after you have completed the
following steps:
•
Electrical Safety Checks – Confirm that the unit’s elec
-
trical system is safe and operating properly
•
Refrigerant Leak Checks – Check all flare nut connec
-
tions and confirm that the system is not leaking
•
Confirm that liquid and gas valves are fully open
Procedure
You should perform the Test Run for at least 30 minutes.
1. Connect power to the unit.
2.
Press the ON/OFF button on the remote controller to
turn it on.
3. Press the mode button to scroll through the following
functions, one at a time:
•
COOL - Select lowest possible temperature
•
HEAT - Select highest possible temperature
4. Let each function run for 5 minutes, and perform the
following checks:
Table 9.
Test Run Checklist
Checks
Pass
Fail
No electrical leakage
Unit is properly grounded
All electrical terminals
properly covered
Indoor and outdoor units are
solidly installed
All pipe connection points do
not leak
Outdoor
(2):
Indoor
(2):
Water drains properly from
drain hose
All piping is properly
insulated
Unit performs COOL function
properly
Unit performs HEAT function
properly
Indoor unit louvers rotate
properly
Indoor unit responds to
remote controller