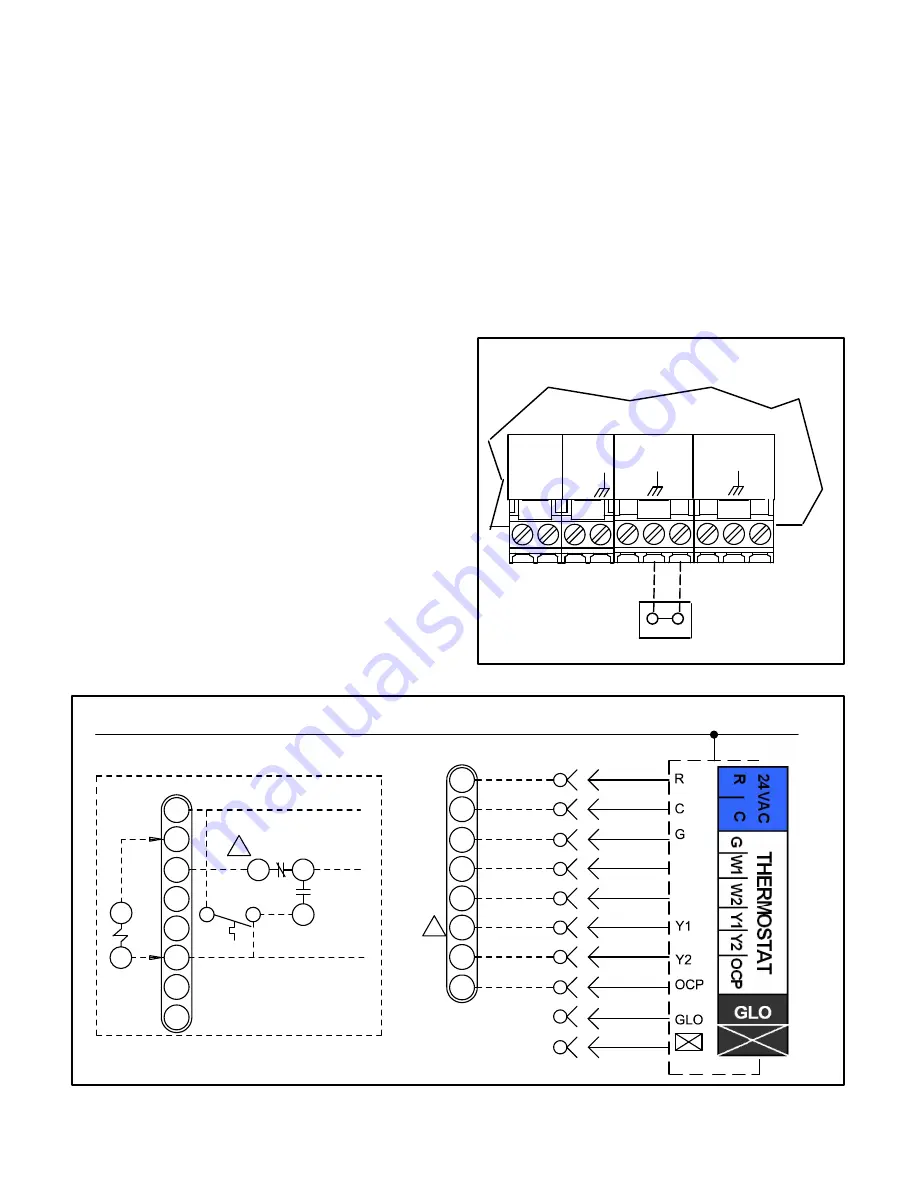
Page 11
LGM/LCM036, 048, 060, 074
B-Control Wiring
The Unit Controller will operate the unit from a
thermostat or zone sensor based on the System Mode.
The default System Mode is the thermostat mode. Refer
to the Unit Controller Setup Guide to change the System
Mode. Use the mobile service app menu and select
Settings > Install
.
Thermostat Mode
1- Route thermostat cable or wires from subbase to
control area above compressor (refer to unit
dimensions to locate bottom and side power entry).
IMPORTANT - Unless field thermostat wires are rated for
maximum unit voltage, they must be routed away from
line voltage wiring. Use wire ties located near the lower
left corner of the controls mounting panel to secure
thermostat cable.
Use18 AWG wire for all applications using remotely
installed electro-mechanical and electronic
thermostats.
2- Install thermostat assembly in accordance with
instructions provided with thermostat.
3- Connect thermostat wiring to Unit Controller on the
lower side of the controls hat section.
4- Wire as shown in figure 16 for electro-mechanical
and electronic thermostats. If using other
temperature control devices or energy management
systems see instructions and wiring diagram
provided by manufacturer.
IMPORTANT-Terminal connections at the wall plate or
subbase must be made securely. Loose control wire
connections may allow unit to operate but not with proper
response to room demand.
Zone Sensor Mode
The Unit Controller will operate heating and cooling
based on the Unit Controller internal setpoints and the
temperature from the A2 zone sensor. An optional
Network Control Panel (NCP) can also be used to provide
setpoints. A thermostat or return air sensor can be used
as a back-up mode. Make zone sensor wiring
connections as shown in figure 15.
FIGURE 15
FIELD WIRING IN ZONE SENSOR MODE
(Zone Sensor Mode)
A2 SENSOR
OUTPUTS
SENSOR
SENSOR
24VAC
R
C
IAQ
HUM
AI1
D01
TMP
D02
UNIT CONTROLLER
J298
FIGURE 16
FIELD WIRING WITH ELECTRONIC AND ELECTRO-MECHANICAL THERMOSTATS
(Thermostat Mode)
J262C
10
11
12
P297
J297A
1
2
B
3
4
5
6
7
8
C
9
10
24 V POWER
W1
W2
P262
A55
R
OCP
C
G
W1
W2
Y1
Y2
2
K55
B
A
K55
−
1
7
5
2
S86
R
OCP
C
G
W1
W2
Y1
Y2
TO R
TO G
TO Y1
TO PROVIDE SUPERMARKET REHEAT SCHEME
USE S86 DEHUMIDISTAT AND K55.
ALL
OTHER
THERMOSTAT
SIGNALS REMAIN CONNECTED
AS SHOWN ON THE RIGHT.
TO UNIT CONTROLLER
2
THERMOSTAT INPUTS