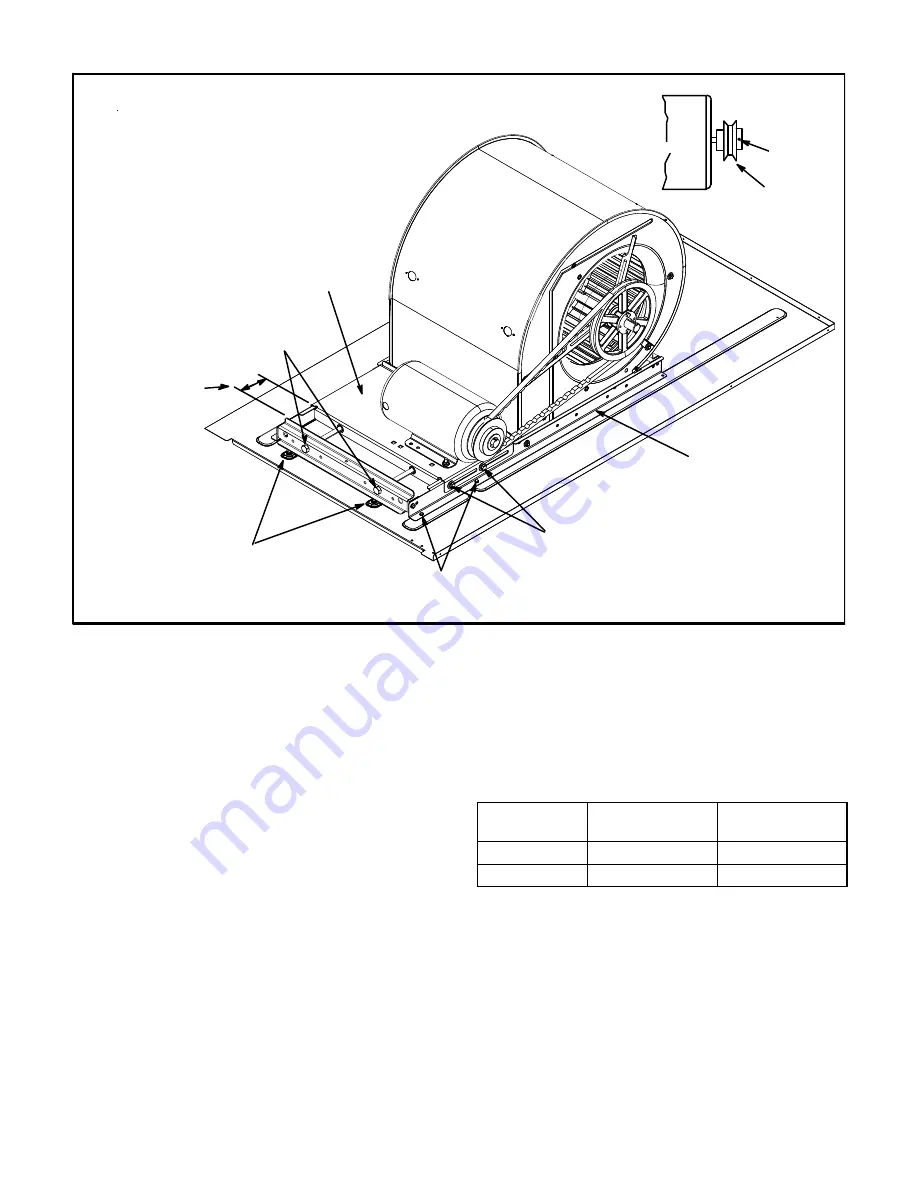
Page 11
STANDARD BLOWER ASSEMBLY
TO INCREASE BELT TENSION
1- Loosen four bolts securing motor mounting base
to frame.
2- Turn adjusting bolt to the right, or clockwise, to
move the motor away from the blower housing.
IMPORTANT - Gap between end of frame and motor
mounting base should be equal at both ends, i.e. par
allel along gap.
3- Tighten four bolts securing motor mounting base
to frame.
4- Relieve tension on two adjusting bolts.
FIGURE 13
PULLEY
MOTOR
SIDE VIEW
ALLEN
SCREW
BELT ADJUSTING BOLTS
- TURN CLOCKWISE
TO TIGHTEN BELT
MOTOR MOUNTING
BASE
LOOSEN BEFORE
ADJUSTING BELT TENSION
(TWO EACH SIDE)
REMOVE TWO SCREWS ON EACH
SIDE TO SLIDE FRAME PARTIALLY
OUT OF UNIT FOR SERVICE ACCESS
MOTOR
BLOWER
HOUSING
BLOWER
FRAME
GAP BETWEEN
EDGES SHOULD BE
PARALLEL ON BOTH
ENDS BEFORE
TIGHTENING MOTOR
MOUNTING BASE IN
PLACE
REMOVE TWO SCREWS
TO COMPLETELY SLIDE
BLOWER OUT OF UNIT
D-Determining Unit CFM
IMPORTANT - Units equipped with an inverter are
factory-set to run the blower at full speed when there is a
blower (G) demand without a heating or cooling demand.
Use the following procedure to adjust motor pulley to
deliver the full load cooling or heating CFM. See Inverter
Start-Up section to set blower CFM for all modes once the
motor pulley is set.
1- The following measurements must be made with a
dry indoor coil. Run blower without a cooling demand.
Measure the indoor blower shaft RPM. Air filters must
be in place when measurements are taken.
2- With all access panels in place, measure static
pressure external to unit (from supply to return).
Blower performance data is based on static pressure
readings taken in locations shown in figure 14.
Note - Static pressure readings can vary if not taken
where shown.
3- Referring to page 13, 14, or 15, use static pressure
and RPM readings to determine unit CFM. Use pages
16 and 17 when installing units with any of the
optional accessories listed.
4- The blower RPM can be adjusted at the motor pulley.
Loosen Allen screw and turn adjustable pulley
clockwise to increase CFM. Turn counterclockwise to
decrease CFM. See figure 13. Do not exceed
minimum and maximum number of pulley turns as
shown in table 2.
TABLE 2
MINIMUM AND MAXIMUM PULLEY ADJUSTMENT
Belt
Minimum
Turns Open
Maximum
Turns Open
A Section
0
5
B Section
1*
6
*No minimum number of turns open when B belt is used on
pulleys 6” O.D. or larger.
E-Blower Belt Adjustment
Maximum life and wear can be obtained from belts only
if proper pulley alignment and belt tension are
maintained. Tension new belts after a 24-48 hour
period of operation. This will allow belt to stretch and
seat in the pulley grooves. Make sure blower and motor
pulleys are aligned as shown in figure 15.
1- Loosen four bolts securing motor base to mounting
frame. See figure 13.