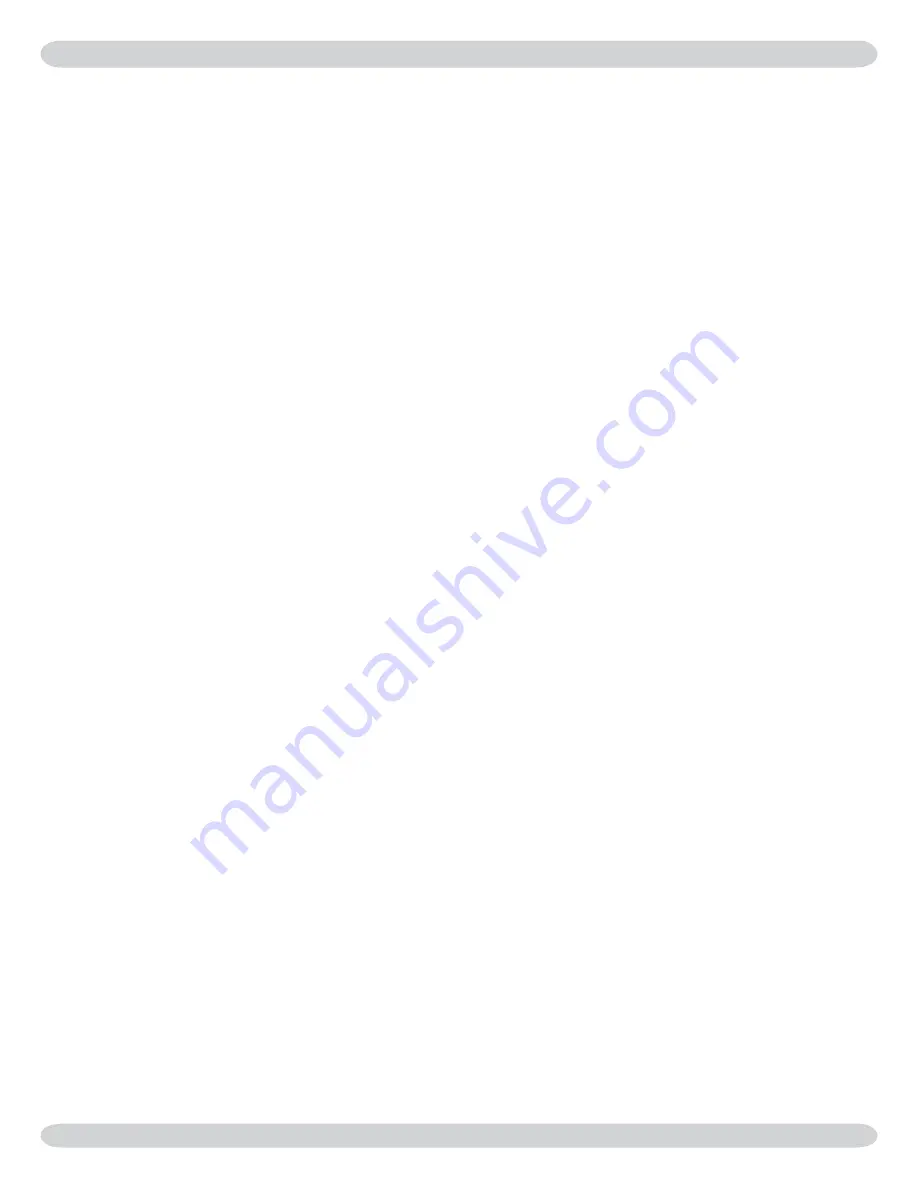
37
When filling the boiler water is the preferred heating solution.
Most potable water supplies may be used to charge and re-fill
provided the chlorine and chloride ions levels are less than 100
ppm.
Antifreeze may be used in most applications provided all of the
following conditions are met:
Unless a strict schedule of sampling, analysis and main-
1.
tenance of the antifreeze solution is followed, the boiler
must be piped as a primary loop connected to secondary
loop as shown in the Piping & Wiring Diagram Appendix.
Failure to perform regular maintenance to the antifreeze
manufacturer’s instructions will result in damage to the
heat exchanger and the voiding of boiler warranty.
Only the antifreeze manufacturers listed below are se-
2.
lected.
At installation of a new or replacement boiler and at least
3.
on an annual basis the system antifreeze must be analyzed
by the antifreeze supplier or their recommended labora-
tory.
Adjustments to the system antifreeze must be made ac-
4.
cording to the antifreeze manufacturers recommendations
using only their recommended products.
All existing systems MUST be flushed of ALL old system
5.
fluid. Failure to do so may void the boiler warranty if evi-
dence of improper flushing is revealed. Consult with your
heating professional for recommendations.
Piping Recommendations
System leaks may not always be visible. An unseen system leak
will become obvious if boiler pressure decreases when make up
valve is closed.
All system leaks must be repaired immediately. Constant in-
troduction of make up water will introduce dissolved oxygen,
resulting in accelerated boiler corrosion.
It is recommended that Primary/Secondary piping be used
with any of the recommended antifreeze solutions found in
this manual. See the
Piping & Wiring Diagram Appendix
.
Water Chemistry
This boiler is designed for a closed loop hydronic heat system
ONLY! This boiler is not suitable for natural gravity type in-
stallations, or any other open type system.
System fluid pH must be maintained between 7.0 and 8.0.
Maintain water hardness below 7 grains hardness.
Filling with chlorinated fresh water should be acceptable since
drinking water chlorine levels are typically less than 5 ppm. Do
not fill boiler with water containing chlorine and chloride ions
levels greater than 100 ppm.
Do not use inhibitors or other additives that are not specifically
approved by the antifreeze manufacturer for this product.
Consult the antifreeze manufacturer if any of the above are
outside the stated ranges.
WATER TREATMENT & FREEZE PROTECTION
Summary of Contents for GWB9
Page 15: ...15 Near Boiler Piping Figure 2 Single Zone Boiler Piping...
Page 16: ...16 Figure 3 Multi zone Boiler Piping With Zone Valves Near Boiler Piping...
Page 19: ...19 Figure 6 Diaphragm Type Expansion Tank Piping Near Boiler Piping...
Page 20: ...20 Figure 7 Conventional closed type Expansion Tank Piping Near Boiler Piping...
Page 27: ...27 Combustion Air and Vent Pipe Figure 11 Combustion Air and Vent Piping...
Page 32: ...32 Electrical Wiring Figure 13 Field Wiring Connections...
Page 53: ...53 DETAILED SEQUENCE OF OPERATION...
Page 57: ...57 TROUBLESHOOTING CHART 2 TROUBLESHOOTING...
Page 58: ...58 TROUBLESHOOTING CHART 3 TROUBLESHOOTING...
Page 60: ...60 TROUBLESHOOTING CHART 5 TROUBLESHOOTING...
Page 72: ...Product Literature Lennox Industries Inc Dallas Texas...