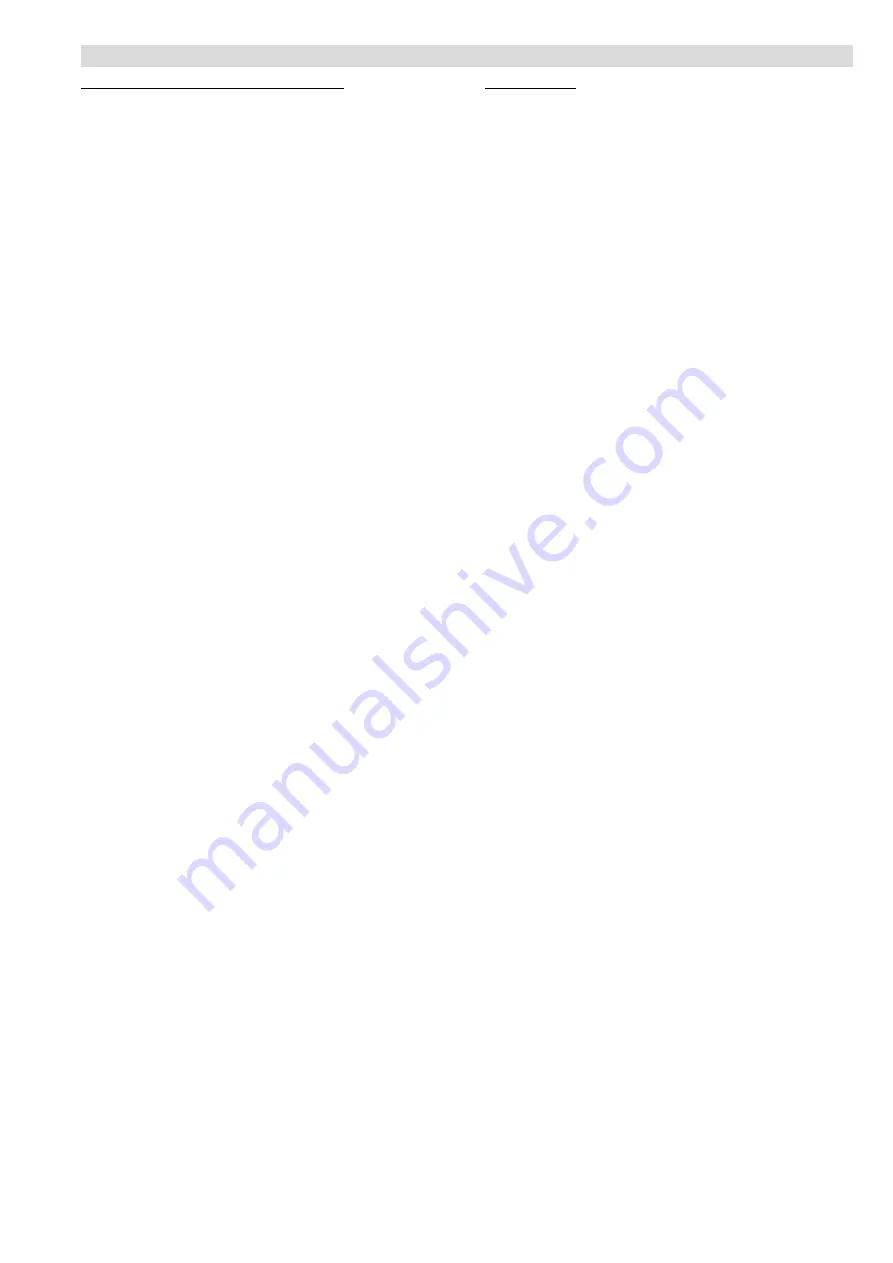
G61MPVT − 50hz
FEATURES
HEATING SYSTEM − continued
Lennox Designed Flue Condensate Trap Assembly
Condensate trap assembly is mounted outside the
conditioned air stream.
Assembly can be mounted on either side of cabinet in
up−flow and down−flow applications. Assembly is mounted
on the bottom of the cabinet in horizontal applications. See
Installation Instructions.
Connection can be made with field provided 1/2 in. PVC
pipe, 3/4 in. PVC coupling, or 1−1/4 in. OD x 1 in. ID tubing
with hose clamp.
Easy to clean and winterize.
Inshot Burners
Aluminized steel inshot burners provide efficient,
trouble−free operation.
Burner venturi mixes air and gas in correct proportion for
proper combustion.
Burner assembly is removable from the unit as a single
component for ease of service.
Two−Stage Gas Control Valve
24 volt redundant combination two stage gas control
valve combines manual shut off valve (On−Off),
automatic electric valve (dual) and gas pressure
regulation into a compact combination control.
Flame Rollout Switch
Manual reset switches are factory installed on burner
box.
Switch provides protection from abnormal operating
conditions.
Hot Surface Mini−Nitride Ignitor
Unique, non−porous, high strength proprietary ceramic
material provides long life and trouble−free
maintenance.
Low mass element provides fast heat−up and consistent
igniter temperature with low power usage.
Cemented to alumina block for positive mounting and
protection against current leakage.
High temperature Teflon
®
insulated ignition lead wires
for dependable operation.
Combustion Air Inducer
PSC, heavy−duty blower prepurges heat exchanger and
safely vents flue products.
Pressure switches prove blower operation before
allowing gas valve to open.
Operates only during heating cycle.
Limit Control
Automatic reset, primary and secondary limits are
accurately located.
Primary limit factory installed on vestibule panel on all
units, secondary limit factory installed on blower
housing.
OPTIONS
High Altitude Pressure Switch Kit
Required on certain units for proper unit operation on
installations above 610 m.
Units not approved for installations above 1372 m.
Order two per unit.
LPG/Propane Conversion Kit
Required for field changeover from natural gas to
LPG/Propane.
Natural Gas Conversion Kit
Required for field changeover from LPG/Propane to
natural gas.
CONTROLS
Integrated Two Stage / Variable Speed Blower
Control
Solid−state board contains all necessary controls and
relays to operate furnace.
Combustion air inducer is controlled by board. Prior to
ignition, a pre−purge cycle for 15 seconds is initiated.
After the main burners are turned off, a post−purge cycle
for 5 seconds is run.
Electronic flame sensor assures safe, reliable
operation.
Should flame fail to ignite, flame sensor will initiate 4
re−attempts at ignition before locking out unit operation
for 60 minutes.
Watchguard type circuit automatically resets ignition
controls after one hour of continuous thermostat
demand after unit lockout, eliminating nuisance calls for
service.
To aid in troubleshooting, the last three fault codes are
stored for a maximum of six months. Displays the fault
codes through indicator LED’s.
Jumper settings for 1 or 2 stage thermostat operation.
Two selectable 2nd stage recognition times (10 and 15
minutes) are available on the board when the furnace is
used with a single stage thermostat. When used with a
two stage thermostat, furnace will only initiate second
stage operation with a second stage thermostat
demand.
Two accessory terminals furnished for additional power
supply requirements for 240 volt (less than 1 amp)
power humidifiers and powered air cleaners.
Two blower speeds − second stage heat and second
stage cool (with four air volume selections for each) are
selected by DIP switches on board. Heat speed can be
adjusted to optimize discharge temperature. Cool
speed can be adjusted to correct optional cooling
capacity. See Blower Performance tables.
First stage blower speed is a percentage of 2nd stage
speed.
The ADJUST switch (DIP) allows normal (NORM), 10%
higher (+ plus) or 10% lower
(
minus) motor speed
selection within HEAT and COOL speeds selected for
fine tuning air volume.
DELAY switch (DIP) allows one of four de−humidification
profiles during cooling mode.
Profile A
− Motor runs at 50% for 30 seconds, then at
82% for 7−1/2 minutes, then at 100% (if needed) until
demand is satisfied. Once demand is met, motor runs
at 50% for 30 seconds, then ramps down to stop.
Profile B
− Motor runs at 82% for 7−1/2 minutes and
then at 100% (if needed) until demand is satisfied.
Once demand is met,motor ramps down to stop.
Profile C
− Motor runs at 100% until demand is
satisfied. Once demand is met, motor runs at 100% for
60 seconds, then ramps down to stop.
Profile D
− Motor runs at 100% until demand is satisfied.
Once demand is met, motor ramps down to stop.
In heat mode, blower on time is fixed at 45 seconds,
blower off time is adjustable from 60, 90, 120 and 180
seconds (factory setting − 90 seconds).
Power Lead
2.5 m power lead is provided for connection to an IEC
receptacle located on the right side of the furnace.
IEC Receptacle
IEC receptacle provided on right side of furnace cabinet
for easy, plug−in electrical connection.
24 Volt Transformer
Furnished and factory installed on blower wrapper.
40VA transformer has circuit breaker wired in series.
D
E
F
G
H
I