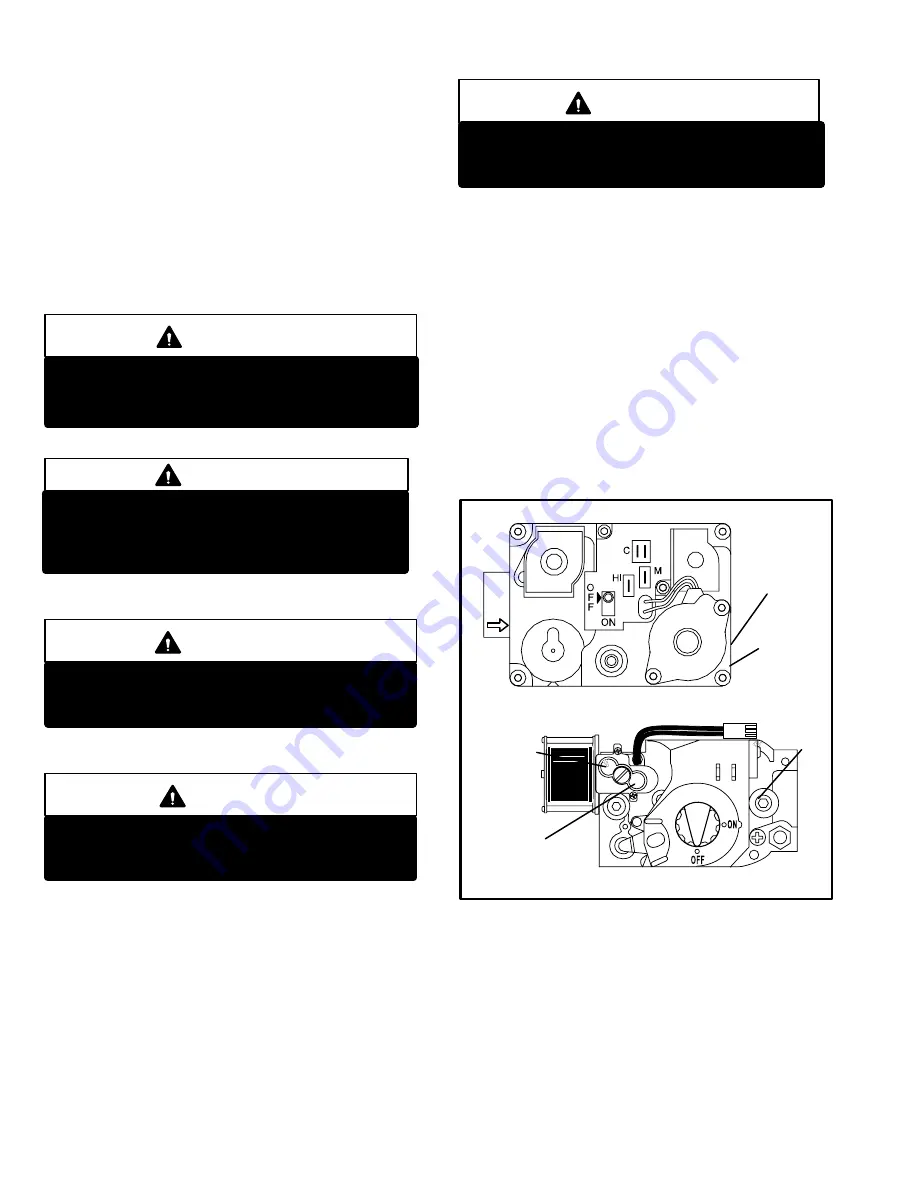
Page 26
III−STARTUP
A−Preliminary and Seasonal Checks
1 − Inspect electrical wiring, both field and factory installed
for loose connections. Tighten as required.
2 − Check voltage at disconnect switch. Voltage must be
within range listed on the nameplate. If not, consult the
power company and have voltage condition corrected
before starting unit.
3 − Inspect condition of condensate traps and drain as
sembly. Disassemble and clean seasonally.
B−Heating StartUp
FOR YOUR SAFETY READ BEFORE LIGHTING
CAUTION
Shock and burn hazard.
G32 units are equipped with the SureLight ignition
system. Do not attempt to light manually.
WARNING
Do not use this furnace if any part has been
underwater. Inspect the furnace and replace any
part of the control system and any gas control
which has been under water.
WARNING
If overheating occurs or if gas supply fails to shut
off, shut off the manual gas valve to the appliance
before shutting off electrical supply.
CAUTION
Before attempting to perform any service or main
tenance, turn the electrical power to unit OFF at
disconnect switch.
BEFORE LIGHTING smell all around the appliance area
for gas. Be sure to smell next to the floor because some gas
is heavier than air and will settle on the floor.
Use only your hand to turn the gas control switch. Never
use tools. If the switch will not turn by hand, do not try to re
pair it, call a qualified service technician. Force or at
tempted repair may result in a fire or explosion.
G32 units are equipped with the SureLight ignition system. DO
NOT attempt to manually light burners on this furnace. Each
time thermostat calls for heat, burners will be automatically lit.
The ignitor does not get hot when there is no call for heat on
units with SureLight ignition system.
How To Operate Gas Valve (Figure
37
)
WARNING
If you do not follow these instructions exactly, a
fire or explosion may result causing property
damage, personal injury or loss of life.
1 −
STOP
! Read the safety information at the beginning of
this section.
2 − Set thermostat to lowest setting.
3 − Turn off all electrical power to furnace.
4 − This appliance is equipped with an ignition device
which automatically lights the burner. Do
not
try to
light the burner by hand.
5 − Remove unit access panel.
6 −
White Rodgers 36E Gas Valve,
switch lever to
OFF
.
Do not force. See figure 37.
7 − Wait five (5) minutes to clear out any gas. If you then
smell gas,
STOP
! Immediately call your gas supplier from
a neighbor’s phone. Follow the gas supplier’s instruc
tions. If you do not smell gas go to next step.
WHITE RODGERS 36E SERIES GAS VALVE
FIGURE 37
HIGH HEAT
MANIFOLD
PRESSURE
ADJUSTMENT
ON SIDE
(under cap)
MANIFOLD
PRESSURE
OUTLET
HONEYWELL VR8205 SERIES Gas Valve
BOTH VALVES SHOWN IN OFF POSITION
HIGH HEAT
MANIFOLD
PRESSURE
ADJUSTMENT
(under cap)
MANIFOLD
PRESSURE
OUTLET ON
SIDE
LOW HEAT
MANIFOLD
PRESSURE
ADJUSTMENT
(under cap)
8 −
White Rodgers 36E Gas Valve,
switch lever to
ON
. Do
not force.
9 − Replace access panel.
10− Turn on all electrical power to unit.
11− Set thermostat to desired setting.
12− If the appliance will not operate, follow the instructions
To Turn Off Gas To Unit" and call your service techni
cian or gas supplier.
Turning Off Gas To Unit
1 − Set thermostat to lowest setting.