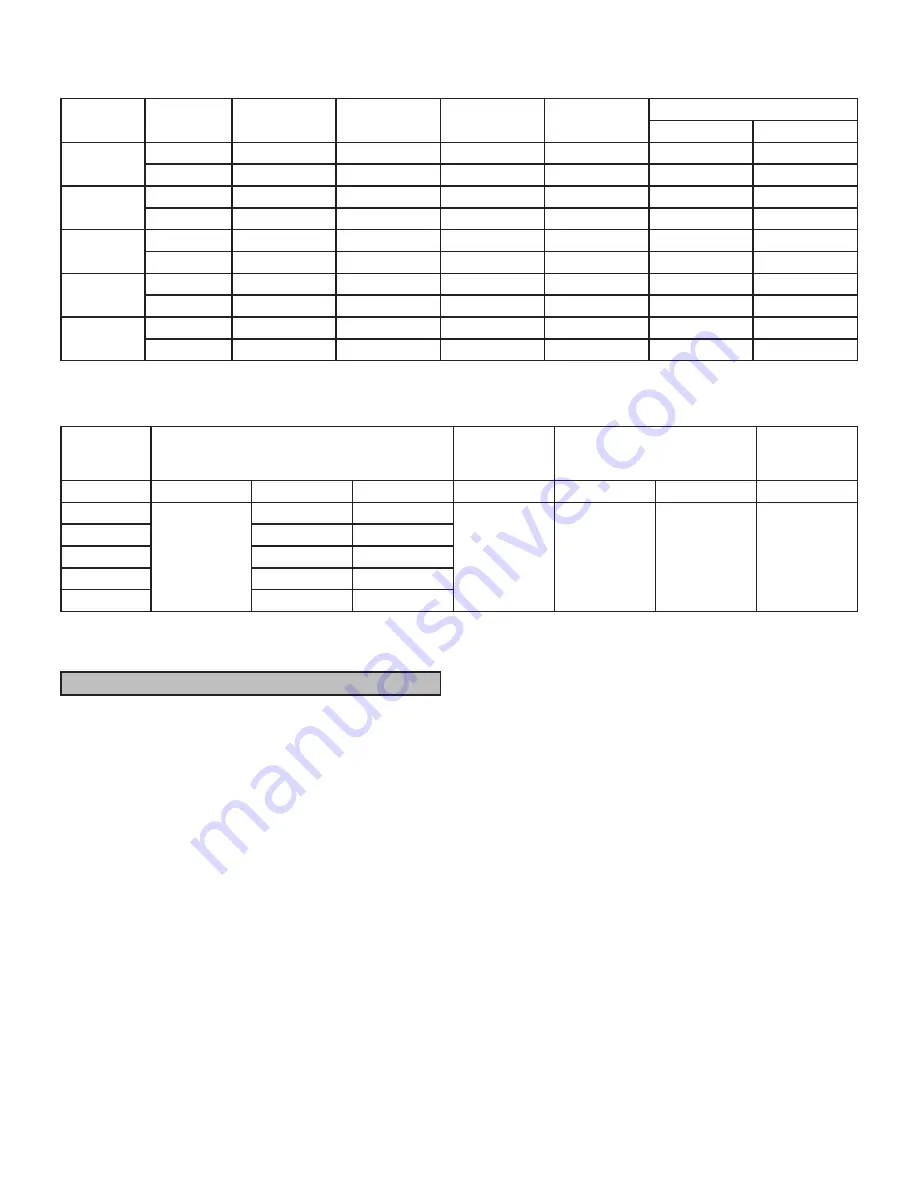
Page 28
TABLE 10
Manifold Pressure Settings at all Altitudes
Model
Input Size
Gas
0 - 2000 ft.
2001 -4500 ft . 4501 - 7500 ft. 7501 - 10,000
ft
Line Pressure in. wg.
Min
Max
045
Nat
3.5
3.2
3.0
3.5
4.5
13.0
LP/Propane
10.0
10.0
10.0
10.0
11.0
13.0
070
Nat
3.5
3.2
2.8
3.5
4.5
13.0
LP/Propane
10.0
10.0
10.0
10.0
11.0
13.0
090
Nat
3.5
3.2
2.7
3.5
4.5
13.0
LP/Propane
10.0
10.0
9.6
10.0
11.0
13.0
110
Nat
3.5
3.5
3.0
3.5
4.5
13.0
LP/Propane
10.0
10.0
9.6
10.0
11.0
13.0
135
Nat
3.5
3.5
2.9
3.5
4.5
13.0
LP/Propane
10.0
10.0
9.6
10.0
11.0
13.0
Other Unit Adjustments
Primary and Secondary Limits
The primary limit is located on the heating compartment
vestibule panel. The secondary limits (if equipped) are lo-
cated in the blower compartment, attached to the back
side of the blower. These auto reset limits are factory-set
and require no adjustment.
Flame Rollout Switches
These manually reset switches are located on the front of
the box.
Pressure Switch
The pressure switch is located in the heating compartment
adjacent to the combustion air inducer. The switch checks
for proper combustion air inducer operation before allow-
ing ignition trial. The switch is factory-set and requires no
adjustment.
TABLE 11
Pressure Switch and Gas Conversion Kits at all Altitudes
Model Input
Size
High Altitude Pressure Switch Kit
High Altitude
Natuarl Gas
Orifice Kit
LP/Propane Oricifice Kit
Natuarl Gas
Orifice Kit
045
0-4500 ft
4501-7500 ft 7501-10,000 ft 7501-10,000 ft
0-7500 ft
7501-10,000 ft
0-7500 ft
070
No Change
80W52
80W51
73W37
11K49
73W81
73W81
110
80W52
80W51
090
80W52
80W51
110
80W57
80W52
135
80W52
80W51
NOTE - A natural to L.P. propane gas changeover kit is necessary to convert this unit. Refer to the changeover kit instal
-
lation instruction for the conversion procedure.
Temperature Rise
After the furnace has been started, and supply and return
air temperatures have been allowed to stabilize, check the
temperature rise
If necessary, adjust the blower speed to maintain the tem-
perature rise within the range shown on the unit nameplate.
Increase the blower speed to decrease the temperature.
Decrease the blower speed to increase the temperature
rise. Failure to adjust the temperature rise may cause er-
ratic limit operation.
Fan Control
The heat fan-on time of 30 seconds is not adjustable. The
heat fan-off delay (amount of time that the blower oper-
ates after the heat demand has been satisfied) may be
adjusted by changing the jumper position across the five
pins on the integrated control. The unit is shipped with a
factory fan-off delay setting of 90 seconds. The fan-off de-
lay affects comfort and is adjustable to satisfy individual
applications. Adjust the fan-off delay to achieve a supply
air temperature between 90° and 110°F at the moment
that the blower is de-energized. Longer off delay settings
provide lower return air temperatures; shorter settings
provide higher return air temperatures. See figure 32