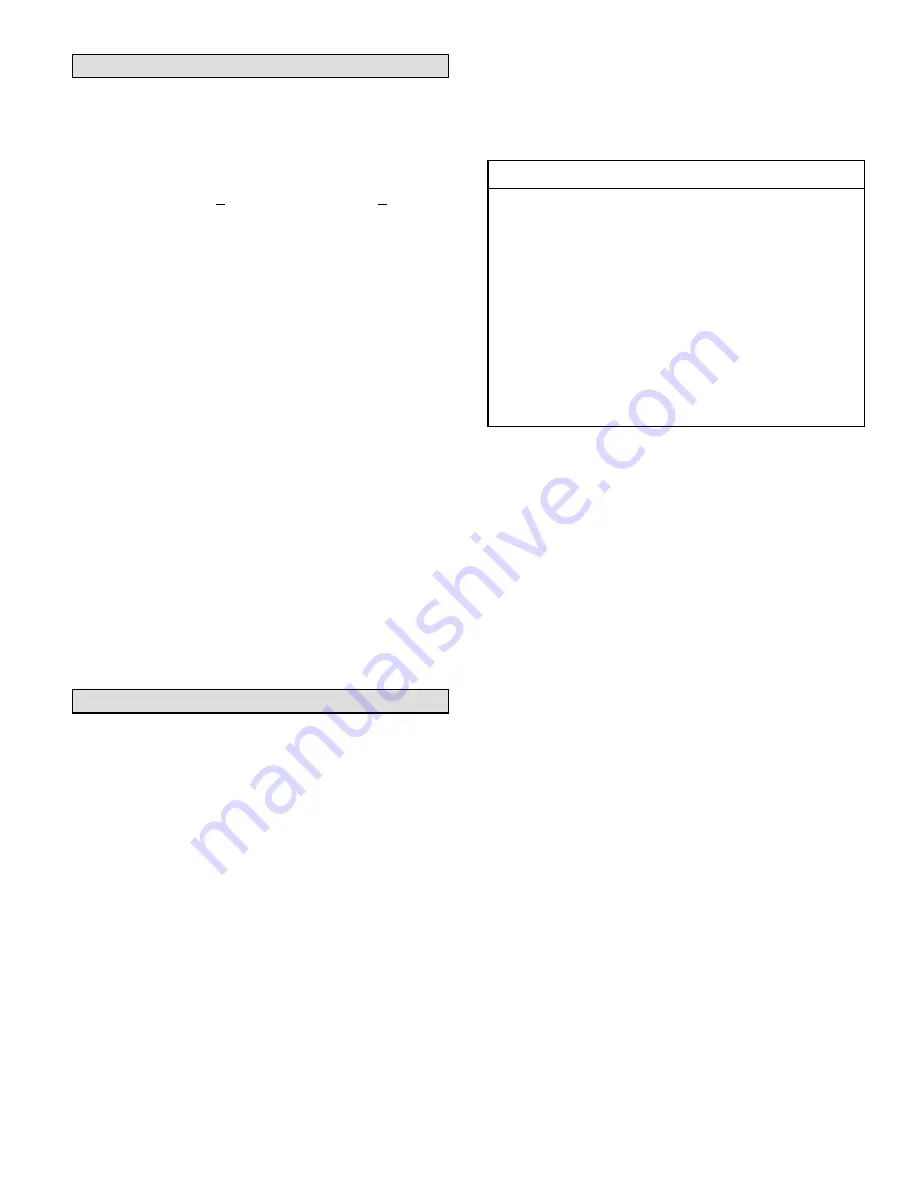
Page 23
EL16XC1 SERIES
System Operation
HIGH PRESSURE SWITCH (S4)
EL16XC1 units are equipped with a high‐pressure switch
that is factory-wired and located in the liquid line. The
switch is a Single Pole, Single Throw (SPST), auto-reset
switch which is normally closed and removes power from
the compressor when discharge pressure rises above
factory setting at 590 + 10 psig; resets at 418 + 5 psig.
CRANKCASE HEATER (HR1) AND THERMOSTAT
(S40)
Compressors in some models are equipped with a 40 watt
or 70 watt, belly band type crankcase heater. HR1
prevents liquid from accumulating in the compressor. HR1
is controlled by a single pole, single throw thermostat
switch (S40) located on the liquid line.
When liquid line temperature drops below 50° F the
thermostat closes energizing HR1. The thermostat will
open, de-energizing HR1 once liquid line temperature
reaches 70° F.
THERMAL PROTECTION SWITCH (S173) -
COMPRESSOR MOUNTED
Some units are equipped with a compressor mounted
normally closed temperature switch that prevents
compressor damage due to overheating caused by
internal friction. The switch is located on top of the
compressor casing. This switch senses the compressor
casing temperature and opens at 239-257°F
(115°C-125°C) to shut off compressor operation. The
auto-reset switch closes when the compressor casing
temperature falls to 151-187°F (66°C-86°C), and the
compressor is re-energized. This single-pole, single-throw
(SPST) bi-metallic switch is wired in series with the 24V Y
input signal to control compressor operation.
Maintenance
Your heating and air conditioning system should be
inspected and maintained yearly (before the start of the
cooling and heating seasons) by a licensed professional
HVAC technician. You can expect the technician to check
the following items.
These checks may only be
conducted by a licensed professional HVAC
technician.
Outdoor Unit
1. Inspect component wiring for loose, worn or damaged
connections. Also check for any rubbing or pinching of
wires. Confirm proper voltage plus amperage of outdoor
unit.
2. Check the cleanliness of outdoor fan and blade
assemblies. Check condition of fan blades (cracks).
Clean or replace them, if necessary.
3. Inspect base pan drains for debris and clean as
necessary.
4. Inspect the condition of refrigerant piping and confirm
that pipes are not rubbing copper-to-copper. Also,
check the condition of the insulation on the refrigerant
lines. Repair, correct, or replace as necessary.
5. Test capacitor. Replace as necessary.
6. Inspect contactor contacts for pitting or burn marks.
Replace as necessary.
7. Check outdoor fan motor for worn bearings/bushings.
Replace as necessary.
8. Inspect and
clean
outdoor coils, if necessary and note
any damage to coils or signs of leakage.
NOTICE !
Failure to follow instructions will cause damage to
the unit.
This unit is equipped with an aluminum coil. Alu
minum coils may be damaged by exposure to solu
tions with a pH below 5 or above 9. The aluminum
coil should be cleaned using potable water at a
moderate pressure (less than 50psi). If the coil can
not be cleaned using water alone, Lennox recom
mends use of a coil cleaner with a pH in the range of
5 to 9. The coil must be rinsed thoroughly after
cleaning.
In coastal areas, the coil should be cleaned with
potable water several times per year to avoid corro
sive buildup (salt).
Indoor Unit (Air Handler or Furnace)
1. Inspect component wiring for loose, worn or damaged
connections. Confirm proper voltage plus amperage
indoor unit.
2. Inspect and clean or replace air filters in indoor unit.
3. Check the cleanliness of indoor blower and clean
blower, if necessary.
4. Inspect the evaporator coil (Indoor) drain pans and
condensate drains for rust, debris, obstructions, leaks
or cracks. Pour water in pans to confirm proper
drainage from the pan through to the outlet of the pipe.
Clean or replace as necessary.
5. Inspect and clean evaporator (indoor) coil, if necessary.
6. Inspect the condition of the refrigerant lines and
confirm that pipes are not rubbing copper-to-copper.
Also, ensure that refrigerant pipes are not being
affected by indoor air contamination. Check condition
of insulation on the refrigerant lines. Repair, correct, or
replace as necessary.
7. Inspect the duct system for leaks or other problems.
Repair or replace as necessary.
8. Check for bearing/bushing wear on indoor blower
motor. Replace as necessary.
9. Indoor unit inspections of gas- or oil-fired furnaces will
also include inspection and cleaning of the burners,
and a full inspection of the gas valve, heat exchanger
and flue (exhaust) system.
General System Test with System Operating
1. Your technician should perform a general system test.
He will turn on the air conditioner to check operating
functions such as the startup and shutoff operation.
He will also check for unusual noises or odors, and
measure indoor/outdoor temperatures and system
pressures as needed.
2. The technician will check the refrigerant charge per
the charging sticker information on the outdoor unit.
3. Verify that system total static pressure and airflow
settings are within specific operating parameters.
4. Verify correct temperature drop across indoor coil.