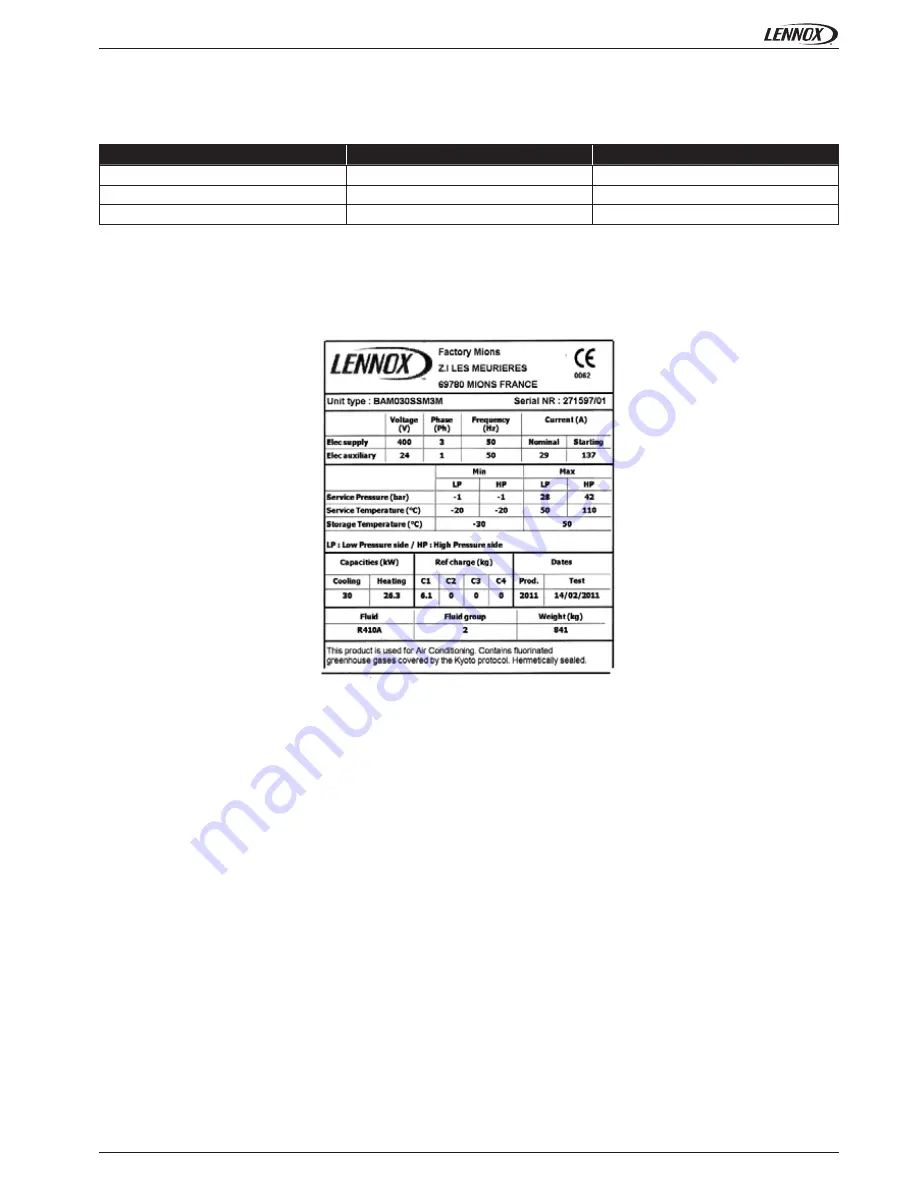
• 35 •
29,5
42 bar R410A
42 bar R410A
BALTIC-IOM-0412-E / Service manual
PRESSURE EQUIPEMENT DIRECTIVE INFORMATIONS
CE marking compliance
These units are CE marked according to Pressure Equipement Directive.
Periodical visit according european pressure equipment directive
According to Pressure Equipments Directive, periodical controls on site are expected on equipments equal or above category II.
Name plate example
Section
Phase
PS (bars gauge)
Suction
Vapor
Discharge
Vapor
Liquid
Liquid / Vapor
Summary of Contents for BAC 024 SNM 3M
Page 2: ......
Page 4: ......
Page 76: ...72 BALTIC IOM 0412 E Service manual...
Page 98: ...94 BALTIC IOM 0412 E Certificates CE CONFORMITY DECLARATION...
Page 99: ...95 BALTIC IOM 0412 E Certificates CE CONFORMITY DECLARATION...