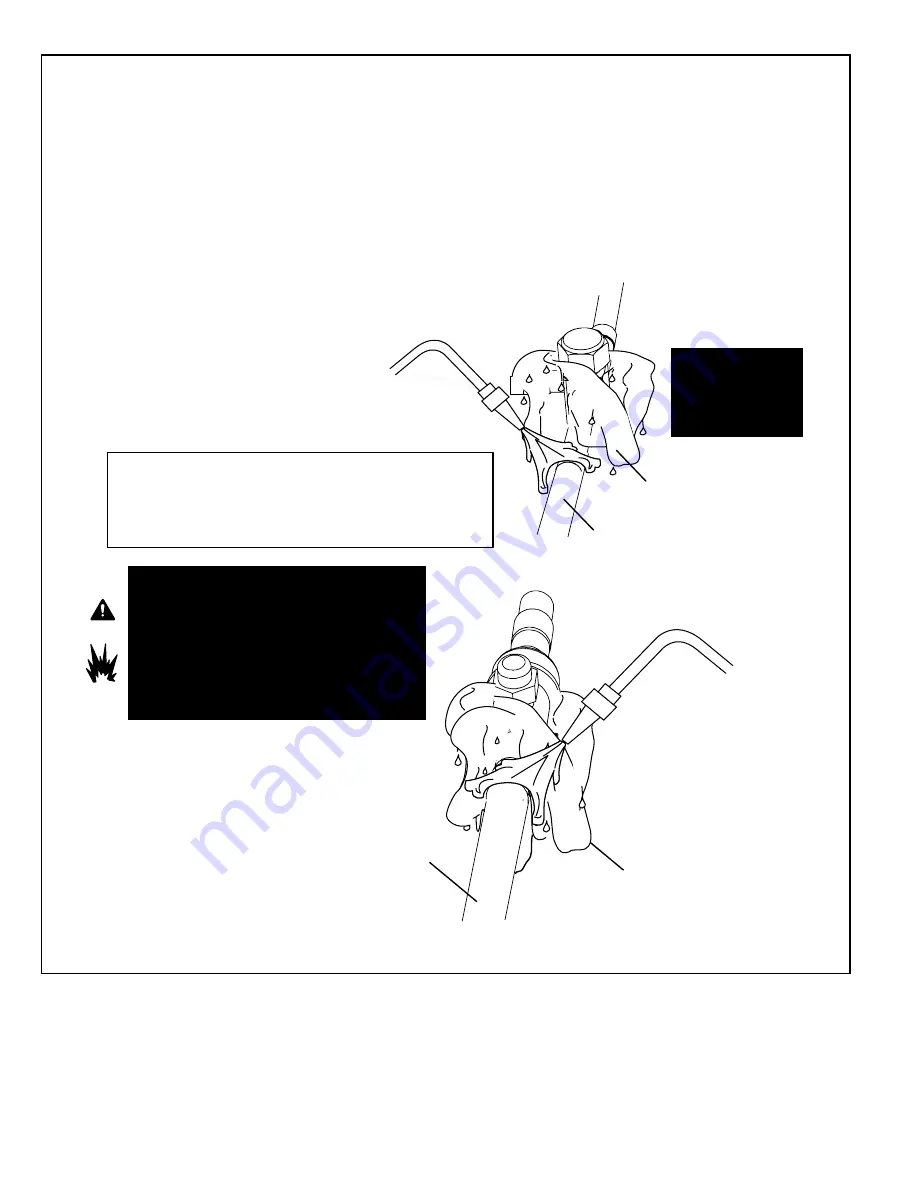
506318-03
Page 8 of 18
Issue 1946
WHEN BRAZING LINE SET TO
SERVICE VALVES, POINT FLAME
AWAY FROM SERVICE VALVE.
LIQUID LINE SERVICE VALVE
LIQUID LINE
BRAZE LINE SET
Wrap both service valves with water-saturated cloths as illustrated here and as mentioned in step 4, before brazing to line set.
Cloths must remain water-saturated throughout the brazing and cool-down process.
WATER-SATURATED
CLOTH
IMPORTANT —
Allow braze joint to cool. Apply
additional water-saturated cloths to help cool brazed
joint. Do not remove water-saturated cloths until
piping has cooled. Temperatures above 250ºF will
damage valve seals.
6
VAPOR LINE
WATER-SATURATED
CLOTH
VAPOR LINE
SERVICE VALVE
After all connections have been brazed, disconnect manifold gauge set from service ports. Apply additional water-saturated cloths to both
services valves to cool piping. Once piping is cool, remove all water-saturated cloths.
WHEN BRAZING LINE SET TO
SERVICE VALVES, POINT FLAME
AWAY FROM SERVICE VALVE.
PREPARATION FOR NEXT STEP
7
WRAP SERVICE VALVES
To help protect service valve seals during brazing, wrap water-saturated cloths around service valve bodies and copper tube stubs. Use
additional water-saturated cloths underneath the valve body to protect the base paint.
4
FLOW NITROGEN
Flow regulated nitrogen (at 1 to 2 psig) through the refrigeration gauge set into the valve stem port connection on the liquid service valve and
out of the vapor valve stem port. See steps
3A, 3B
and
3C
on manifold gauge set connections.
5
WARNING
FIRE, PERSONAL INJURY, OR PROPERTY DAMAGE
may result if you do not wrap a water-saturated cloth around
both liquid and suction line service valve bodies and copper
tube stub while brazing the line set! The braze, when
complete, must be quenched with water to absorb any
residual heat.
Do not open service valves until refrigerant lines and
indoor coil have been leak-tested and evacuated. Refer
to Leak Test and Evacuation section of this manual.
WARNING
While protecting the
service valve seals with
water-saturated cloths,
ensure that water does
NOT enter the system.