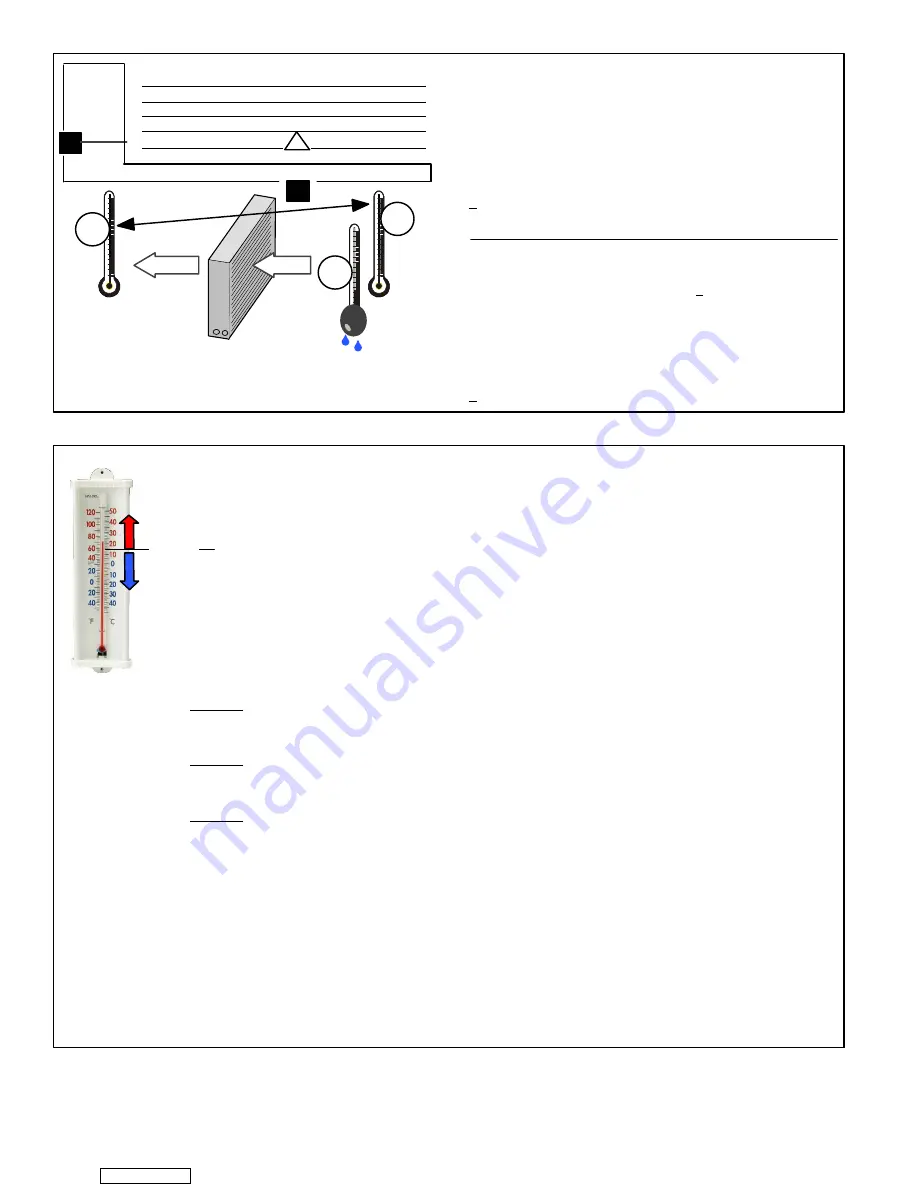
Page 26
506727−01
1. Determine the desired
D
T
Measure entering air temper-
ature using dry bulb (
A
) and wet bulb (
B
).
D
T
is the intersect-
ing value of
A
and
B
in the table (see triangle).
2. Find temperature drop across coil
Measure the coil’s dry
bulb entering and leaving air temperatures (
A
and
C
). Tem-
perature Drop Formula: (
T
Drop
) =
A
minus
C
.
3. Determine if fan needs adjustment
If the difference between
the measured
T
Drop
and the desired
D
T
(T
Drop
–
D
T)
is within
+3º, no adjustment is needed. See examples: Assume
D
T
=
15 and
A
temp. = 72º, these
C
temperatures would necessi-
tate stated actions:
Cº
T
Drop
–
D
T
=
ºF
ACTION
53º
19
–
15
=
4
Increase the airflow
58º
14
–
15
=
−1
(3º range) no change
62º
10
–
15
=
−5
Decrease the airflow
4. Adjust the fan speed
See indoor unit instructions to in-
crease/decrease fan speed.
Changing air flow affects all temperatures; recheck tempera-
tures to confirm that the temperature drop and
D
T are within
+3º.
D
T
80
24 24 24 23 23 22 22 22 20 19 18 17 16 15
78
23 23 23 22 22 21 21 20 19 18 17 16 15 14
76
22 22 22 21 21 20 19 19 18 17 16 15 14 13
74
21 21 21 20 19 19 18 17 16 16 15 14 13 12
72
20 20 19 18 17 17 16 15 15 14 13 12 11 10
70
19 19 18 18 17 17 16 15 15 14 13 12 11 10
57 58 59 60 61 62 63 64 65 66 67 68 69 70
Temp.
of air
entering
indoor
coil ºF
INDOOR
COIL
DRY
BULB
DRY
BULB
WET
BULB
B
T
Drop
19º
A
Dry−bulb
Wet−bulb ºF
A
72º
B
64º
C
53º
air flow
air flow
All temperatures are
expressed in ºF
Figure 22. Checking Airflow over Indoor Coil Using Delta−T Formula
1. Check liquid and vapor line pressures. Compare pressures with either second−stage heat or cooling mode
normal operating pressures listed in table 4. Table 4 is a general guide and expect minor pressures
variations. Significant pressure differences may indicate improper charge or other system problem.
2. Decide whether to use cooling or heating mode based on current outdoor ambient temperature:
A
Use
COOLING MODE
when:
Outdoor ambient temperature is
60°F (15.5°C) and above
.
Indoor return air temperature range is between
70 to 80°F (21−27°C)
. This temperature range is
what the target subcooling values are base upon in table 3.
If indoor return air temperature is not within reference range, set thermostat to cooling mode and a
setpoint of
68ºF (20ºC)
.
This should place the outdoor unit into second−stage (high−capacity)
cooling
mode. When operating and temperature pressures have stabilized, continue to step 3.
B
Use
HEATING MODE
when:
Outdoor ambient temperature is
59°F (15.0°C) and below
.
Indoor return air temperature range is between
65−75°F (18−24°C)
. This temperature range is
what the target subcooling values are base upon in table 3.
If indoor return air temperature is not within reference range, set thermostat to heating mode and a
setpoint of
77ºF (25ºC)
.
This should place the outdoor unit into second−stage (high−capacity)
heating
mode. When operating and temperature pressures have stabilized, continue to step 3.
it in the
SATº
space to the left.
4. Read the liquid line temperature; record in the
LIQº
space to the left.
5. Subtract
LIQº
temperature from
SATº
temperature to determine subcooling; record it in
SCº
space to the
left..
6. Compare
SCº
Heating
or
Cooling
mode column), also consider any additional
charge required for line set lengths longer than 15 feet and/or unit matched component combinations (
Add
Charge
column).
7. If subcooling value is:
AGREATER
than shown for the applicable unit match component,
REMOVE
refrigerant;
BLESS
than shown for the applicable unit match component,
ADD
refrigerant.
8. If refrigerant is added or removed, repeat steps 3 through 6 to verify charge.
9. Close all manifold gauge set valves and disconnect gauge set from outdoor unit.
10. Replace the stem and service port caps and tighten as specified in
Operating Service Valves
11. Recheck voltage while the unit is running. Power must be within range shown on the nameplate.
USE
COOLING
MODE
USE
HEATING
MODE
60ºF
(15ºC)
SATº
LIQº
–
SCº
=
Figure 23. Using HFC−410A Subcooling Method Second Stage (High Capacity) Optimizing Charge
Downloaded from