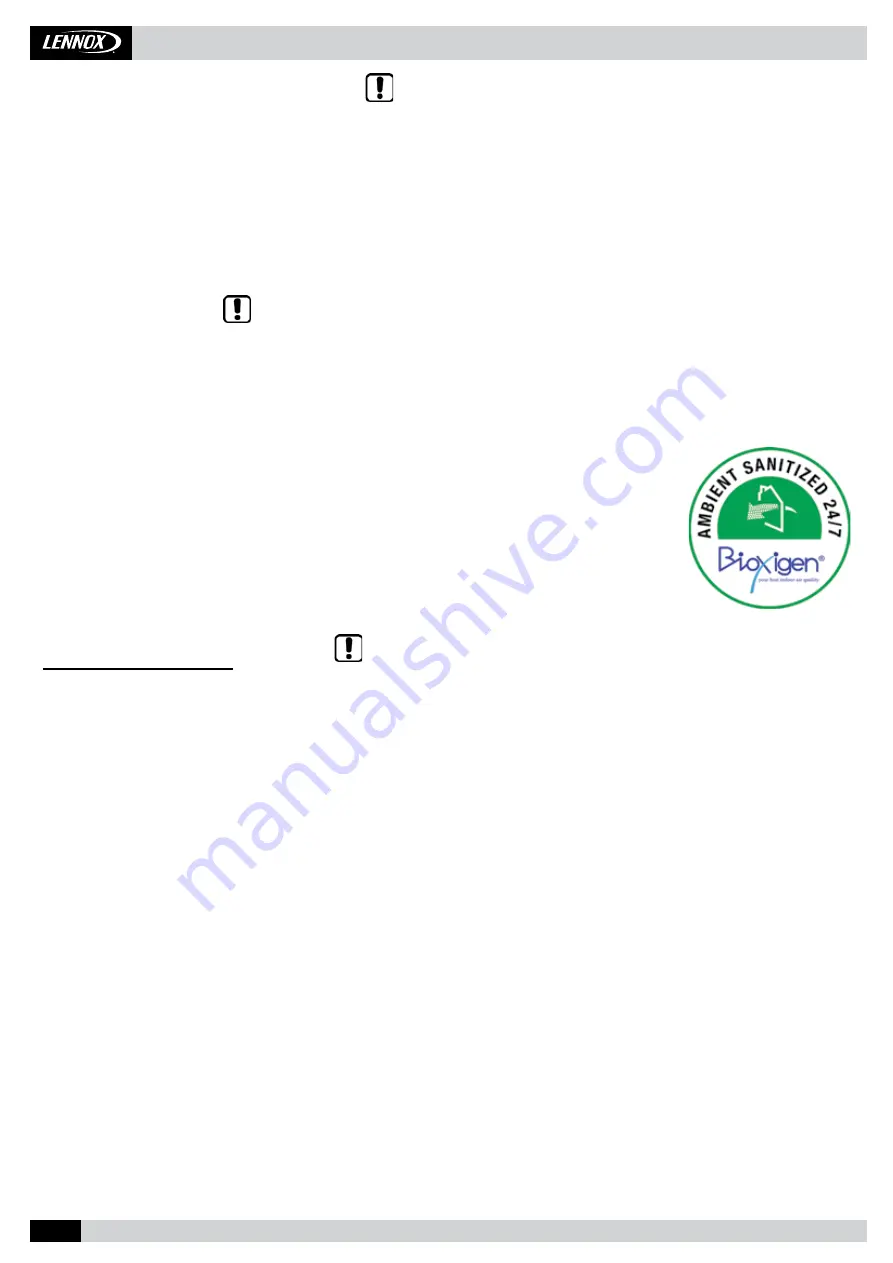
• 4 •
Installation Manual •
MAXIAIR MXP-HPW & HPWI-IOM/1905-E
3. PRESENTATION OF THE MANUAL
This manual describes the rules for the transportation, the installation, the use and the maintenance of the heat recovery. The
user will find everything that is normally useful to know for a correct and safe installation of
MXP-HPW
and
MXP-HPWI
air
treatment units.
The non-observance of what is described in this handbook and an inadequate installation of the unit may cause the
cancellation of the guarantee that the Manufacturing Company grants on the same one. The Manufacturing Company,
moreover, does not answer to possible direct and/or indirect damages due to wrong installation carried out by inexpert and/or
non-authorised staff. At the moment of the purchase, check that the machine is integral and complete. Claims will have to be
produced within 8 days from the reception of the goods.
4. MXP-HPW / HPWI
MXP-HPW
and
MXP-HPWI
fresh air handling units are distinguished by twin heat recovery system, by rotative enthalpic
recovery and refrigerant reversing cycle, which helps to reduce the installed power. Thanks to scroll compressors (n°1
variable flow inverter driven type + n°1 ON /OFF type on
HPWI
version) and EC motor fans, the purpose of heat loads &
ventilation control is always to achieve as the highest system efficiency as the highest reduction of energy consumption
and pollutant emissions.
These units, equipped with the needed additional treatment optional systems, may be a stand-
alone plant solution or can well integrate central heating/cooling systems, both series and
parallel layout.
The models of
MXP-HPW
and
MXP-HPWI
series can be fitted with a ionization system of
the air called BIOXIGEN
®
. This system, unique in his type, makes the air and surfaces of the
machine, of the ducts and of the bordering rooms healthy and good smelling.
5. GENERAL CHARACTERISTICS
5.1 General characteristics
• Frame made from extruded Anticorodal 63 aluminium alloy bars, connected by 3-way reinforced nylon joints
•
Sandwich panels, 48 mm thickness, galvanized sheet metal inner skin and precoated (RAL 9002) sheet metal outer
skin; 45 kg/m3 density foamed polyurethane as heat and sound insulation
•
Filtering sections at both air intakes and already fitted with pressure switch, complete with 98 mm thickness ISO
16890 ePM10 50% (G4 EN 779) efficiency cell prefilters and (on fresh air intake); ISO 16890 ePM1 50% (F7 EN
779) efficiency rigid bag filters, extractable from side removable panels.
•
EC motor direct driven backward curved plug fans; speed control electronics already fitted in the motor
•
First step of energy recovery by enthalpic rotative high efficiency heat recovery, with hygroscopic surface (molecolar
sieve), already equipped with thermal by-pass management by switching off the wheel, for free-cooling / heatingmode
•
Second step of energy recovery (dynamic type) by air-to-air R410A heat pump system composed of two electric
driven scroll compressors (each on/off controlled), evaporating and condensating reversible Cu/Al finned coils,
electronic expansion valves, liquid receivers, 4-way reversible valves, high and low pressure switches, biflow freon
filters, liquid indicators; single variable flow inverter driven scroll compressor as an option in place of standard ones
•
Built-in electric box to control power loads, NTC temperature sensors on both air circuits, electronic controller to
control room temperature (supply temperature in case of variable flow compressor), free-cooling, heating/cooling
mode and defrost cycles; on board control panel.
With SCMB option, Modbus RTU protocol for Building Management System