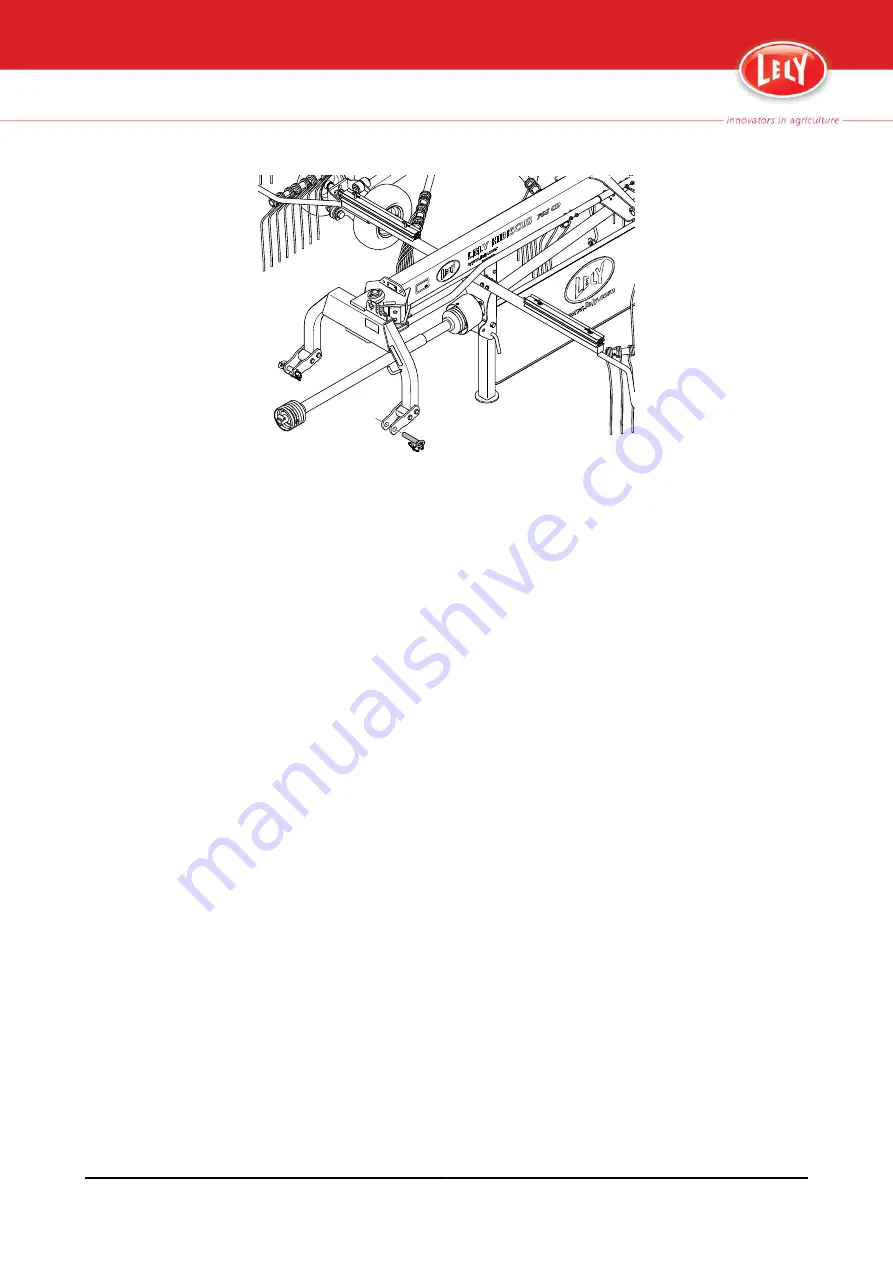
Figure 9. Connect Hibiscus to Tractor
3.3
Disconnect the Hibiscus from the tractor
Procedure
1.
Unlock the parking jack, swing down the parking jack to the bottom
position and lock it in this position
2.
Put the wheel wedges in front of the transport wheels and behind the
transport wheels.
3.
Use the tractor hydraulic system to lower the headstock until the
parking jack is on the ground.
4.
Switch off the tractor engine.
5.
Release the pressure from the tractor hydraulic system.
6.
Disconnect the Hibiscus PTO shaft from the tractor PTO.
7.
Attach the PTO shaft to the mount provided.
8.
Disconnect the hydraulic hoses from the tractor hydraulic system.
9.
Install the dust caps on the hydraulic hoses.
10.
Attach the hydraulic hoses to the support on the headstock.
11.
Disconnect the lighting electrical cable from the tractor.
12.
Disconnect the two lower arms from the linkage pins on the
headstock.
13.
Remove the tractor from the area.
3-4
Operation
R-H014-1210EN
Summary of Contents for Hibiscus 745 CD Vario
Page 1: ...Lely Hibiscus 745 CD Vario R H014 1210EN Operator Manual...
Page 6: ...vi...
Page 14: ...1 6 Introduction R H014 1210EN...
Page 17: ...2 5 Position of the decals Figure 6 Position of the safety decals Safety 2 3 R H014 1210EN...
Page 18: ...2 4 Safety R H014 1210EN...
Page 54: ...5 16 Maintenance R H014 1210EN...
Page 58: ...6 4 Diagrams and tables R H014 1210EN...
Page 60: ...7 2 Troubleshooting R H014 1210EN...
Page 62: ...8 2 Specifications R H014 1210EN...