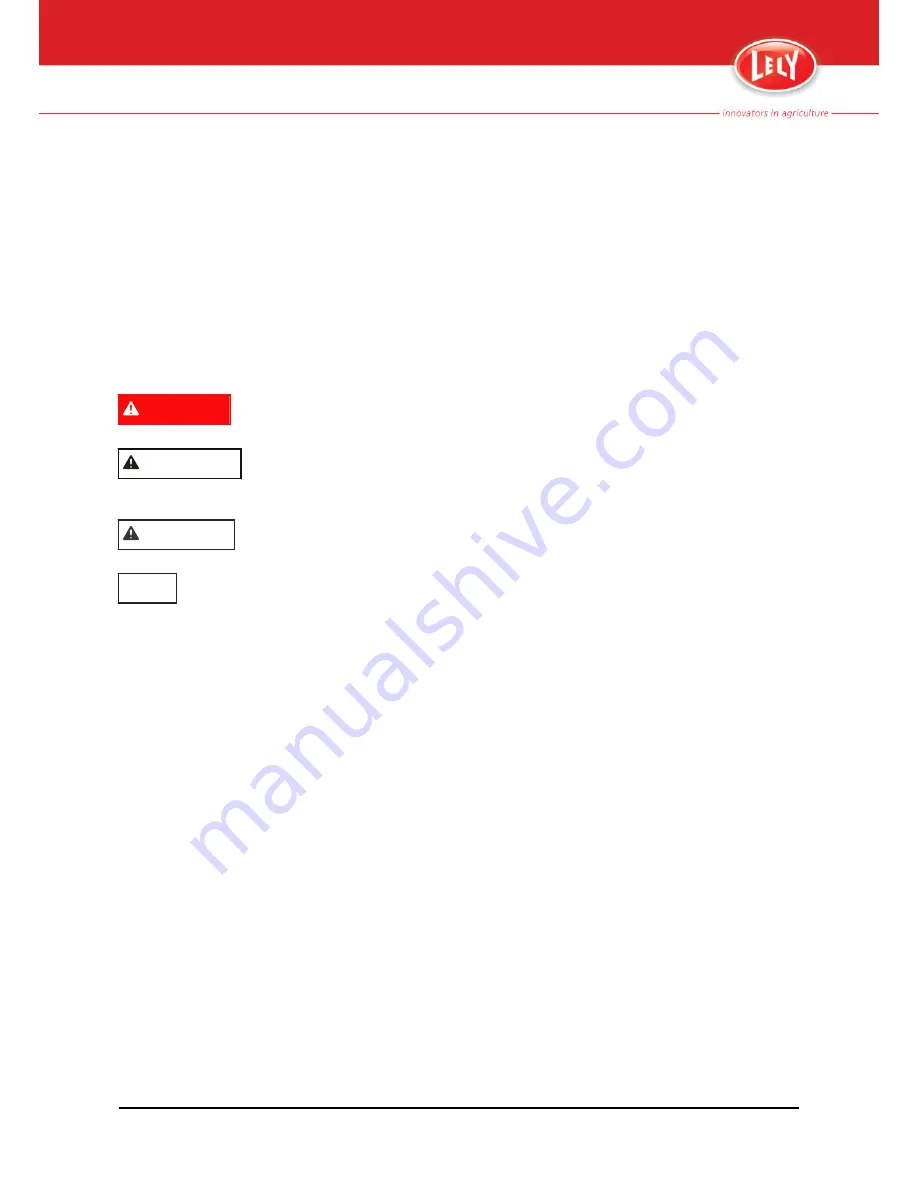
2.
SAFETY
This chapter contains safety instructions you must obey when you use or do
maintenance on your Lely Attis. It also explains the safety decals on the Lely
Attis.
2.1
Signal words
Note the use of the signal words DANGER, WARNING and CAUTION. The
signal word for each message uses the following guidelines:
Danger: Indicates an imminently hazardous situation that,
if not avoided, will result in death or serious injury.
Warning: Indicates a potentially hazardous situation that, if not
avoided, could result in death, serious injury or product damage, and
includes hazards that are exposed when guards are removed.
Caution: Indicates a potentially hazardous situation that, if not avoided, may
result in minor or moderate injury or damage to the product or property.
Note: This shows extra information that may help the reader.
2.2
Safety instructions
2.2.1
Safety instructions
• Use the Attis only for the purpose for which it was designed.
• Read and understand the operator manual before you operate the Attis.
• Follow all safety regulations, including those in this manual and
instructions or warnings indicated on the machine.
• Operate the Attis in a safe manner.
• The Attis must only be operated by authorised persons.
• Be alert and observe all safety precautions.
• Make sure all safety guards and protection devices are installed and
function correctly.
• Keep people and objects away from moving parts.
• Make sure no persons are within a 10 m (11 yd) radius of the Attis during
operation.
• Make sure that the electronic control panel and oil supply are switched off
when you drive on a public road.
• Obey local legislation when you drive on a public road.
• Do not transport a bale on public roads.
• Use flashing lights or other safety signs, when necessary.
• Do not remain on the Attis during operating or transport.
• Only use genuine LELY parts.
DANGER
WARNING
CAUTION
Note:
Safety
2-1
W-H003.1403EN
Summary of Contents for Attis PT 130
Page 1: ...Lely Attis PT 130 Operator Manual W H003 1403EN English Original...
Page 2: ...ii...
Page 4: ...2 Trademarks copyright and disclaimer W H003 1403EN...
Page 8: ...4 Preface W H003 1403EN...
Page 20: ...1 10 Introduction W H003 1403EN...
Page 25: ...2 5 Position of the decals Figure 10 Positions of decals Safety 2 5 W H003 1403EN...
Page 27: ...hold 6 Next instruction 7 Last instruction Up Safety 2 7 W H003 1403EN...
Page 28: ...2 8 Safety W H003 1403EN...
Page 52: ...Figure 21 Unload and tip a bale on its end 3 24 Operation W H003 1403EN...
Page 53: ...Figure 22 Unload a bale Operation 3 25 W H003 1403EN...
Page 68: ...4 10 Operation adjustments W H003 1403EN...
Page 80: ...5 12 Maintenance W H003 1403EN...
Page 82: ...6 2 Troubleshooting W H003 1403EN...
Page 84: ...7 2 Hydraulic diagram 7 2 Diagrams and tables W H003 1403EN...
Page 90: ...8 2 Specifications W H003 1403EN...