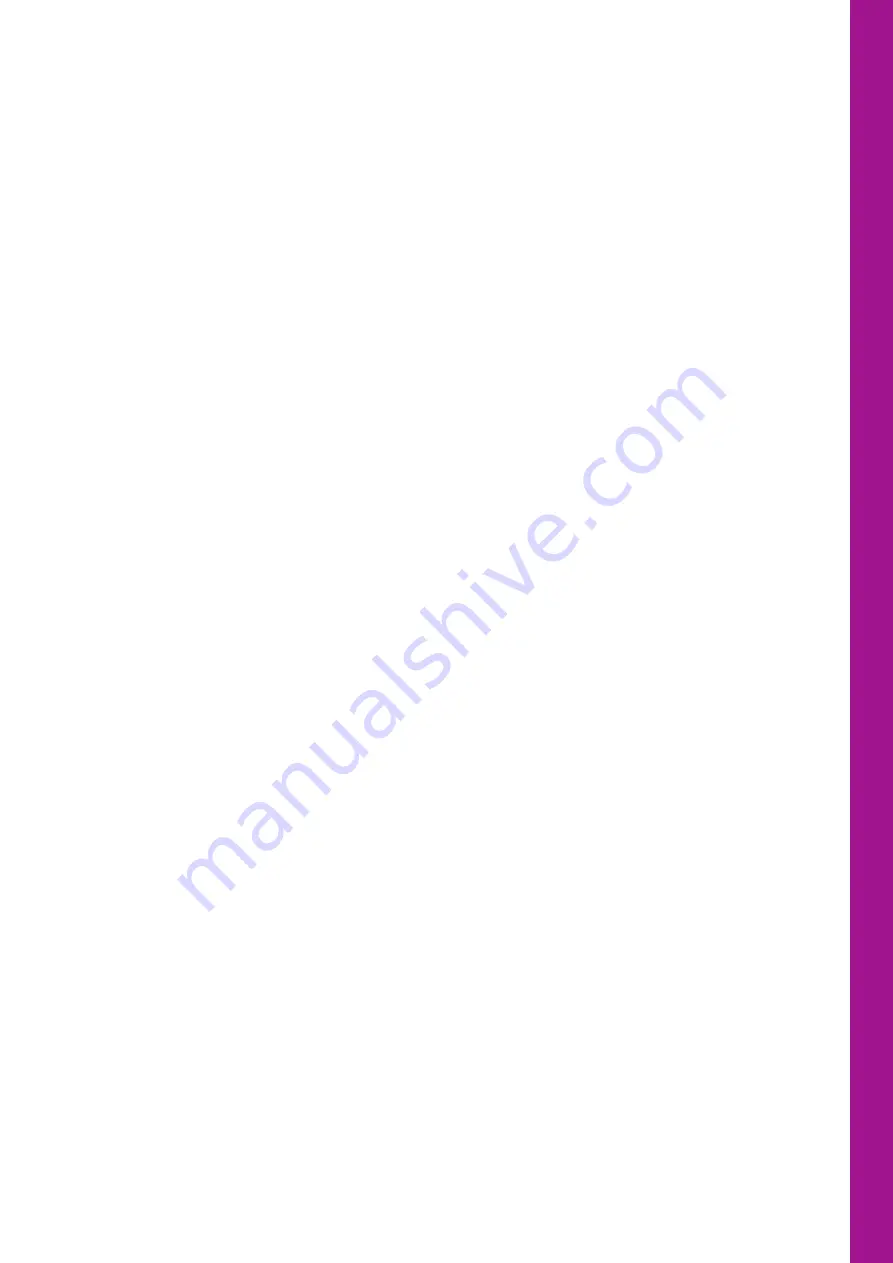
4
1 Rules
1.1 Introduction
These instructions describe the installation, operation and maintenance of the mechanical arrest
system for lifgo
®
, lifgo
®
linear and lean SL
®
units of sizes 5.0, 5.1 and 5.3.
The mechanical arrest system is a mechanism designed to prevent the uncontrolled descent of
components, elements in components or heavy weights and also to prevent the unwanted ap-
plication of forces.
These instructions contain important details relating to the mechanical arrest system. To ensure the
long-term, trouble-free operation of the system, it is essential that the instructions set out here are
adhered to during all phases of the component lifecycle.
Read the current instructions carefully!
In the event of any doubt, contact LEANTECHNIK AG.
The manufacturer of the component is not liable for any environmental harm, damage to property
or personal injury arising out of modifications or operations that do not conform to the present
manual.
© Copyright
The reproduction of texts, images or drawings, either in whole or in part, is prohibited without
LEANTECHNIK AG‘s written approval!
This also applies to the production of copies, translations, microfilming and storage in electronic
systems.
1.2 Machine designation
The component is manufactured and marketed under the name ‘Mechanical arrest system for
lifgo
®
, lifgo
®
linear and lean SL
®
, sizes 5.0, 5.1 and 5.3‘ (see type plate).
This designation should be used in communications and any requests for information. In the re-
mainder of this manual, the mechanical arrest system will be referred to as ‘ASS’, ‘component’
or ‘system’.
LEANTECHNIK AG is the manufacturer of the mechanical arrest system.
1.3 Contact address
LEANTECHNIK AG
Im Lipperfeld 7c
46047 Oberhausen
Germany
Telefon ..49 (0) 208 · 495 25 - 0
Telefax ..49 (0) 208 · 495 25 -18
E-Mail [email protected]
www.leantechnik.com
CE coordinator: Lukas Piofczyk
1 Rules