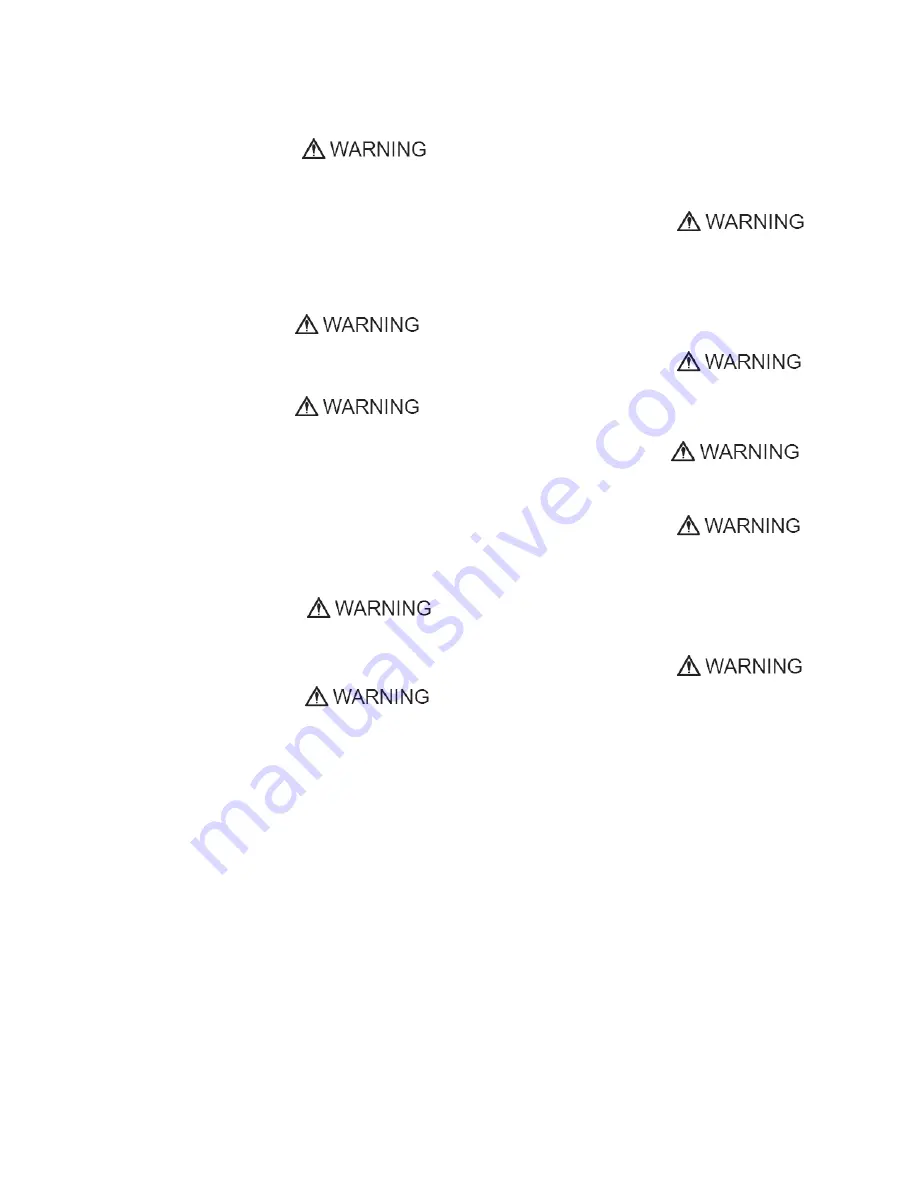
Superabrasive
User
Manual
Original
Language
Lavina®
20
‐
S
6/2013
5
the
machine
easily.
In
order
to
keep
the
electrical
cable
from
being
damaged,
no
vehicle
should
cross
the
zone
where
electrical
cables
are
situated.
PROTECTION
DEVICES
The
machine
is
equipped
with
several
protection
devices
including
the
following:
An
emergency
stop
button
A
protection
skirt
and
a
hood
for
protecting
the
tool
plates.
These
devices
protect
the
operator
and/or
others
persons
from
potential
injuries.
Do
not
remove
them.
On
contrary,
before
using
the
machine,
please
ensure
that
all
protection
devices
are
mounted
and
function
properly.
The
Security
plate
avoid
the
Quickchange
pads
to
loose
during
work
ARREST
FUNCTIONS
Functions
of
arresting
of
the
machine
are
following:
Button
to
stop
the
motor
(category
1)
Emergency
button
(category
1)
SAFE
USE
The
Lavina®
S
is
designed
to
eliminate
all
risks
correlated
with
its
use.
However,
it
is
not
possible
to
eliminate
the
risks
of
an
accident
with
the
machine.
An
unskilled
or
uninstructed
operator
may
cause
correlated
residual
risks.
Such
risks
are:
Position
Risks
due
to
operator’s
incorrect
working
position
Tangling
up
Risks
due
to
wearing
inappropriate
working
clothes
Training
Risks
due
to
lack
of
operational
training
NOTE
:
In
order
to
reduce
all
consequences
of
the
above
‐
mentioned
risks,
we
advise
that
machine
operators
will
follow
the
instructions
in
the
manual
at
all
times.
RESIDUAL
RISKS
During
the
normal
operating
and
maintenance
cycles,
the
operator
is
exposed
to
few
residual
risks,
which
cannot
be
eliminated
due
to
the
nature
of
the
operations.
BEFORE
YOU
BEGIN
Working
area
must
be
clear
from
any
debris
or
objects.
A
first
‐
time
operator
must
always
read
the
manual
and
pay
attention
to
all
safety
instructions.
All
electric
connections
and
cables
must
be
inspected
for
potential
damages.
Ground
wire
system
of
the
power
supply
must
be
also
inspected.
Perform
general
daily
inspections
of
the
machine
and
inspect
the
machine
before
each
use.
Always
inspect
the
safety
devices:
Mount
the
Security
plate
for
the
Quickchange
pads.
The
emergency
break
must
be
clear
and
working
The
tool
protector
must
be
working
The
machine
must
be
clean
Never
operate
the
machine
in
the
rain!
Confirm
that
there
are
no
missing
parts
especially
after
transportation,
repair,
or
maintenance.
Before
filling
the
water
tank
with
water
make
sure
the
machine
is
not
working
and
the
main
switch
is
turned
off.
Before
turning
on
the
machine
make
sure
that
the
base
is
placed
on
the
floor,
the
machine
MUST
NOT
be
in
an
upright
position
when
turned
on!
OPERATING
MACHINE
When
operating
the
Lavina®
S,
make
certain
that
there
is
no
one,
but
you
around
the
machine.
Never
leave
the
machine
unattended
while
working.
The
electrical
cable
must
move
freely
and
must
be
damage
‐
free.
The
water
hose
must
move
freely
and
must
be
damage
‐
free.
Check
if
the
floor,
you
work
on,
is
not
too
uneven.
If
this
is
the
case,
it
may
damage
the
machine.
AFTER
WORK
IS
COMPLETED
Clean
the
machine
and
its
surroundings
properly
Empty
and
clean
the
water
tank
Unplug
the
machine
and
wind
up
the
electrical
cable
Store
the
machine
in
a
safe
place
THE
WORK
AREA
Make
certain
that
people
or
vehicles
do
not
enter
the
work
area.
Avoid
cables
and
hoses
being
in
the
way.
Always
check
the
floor
for
debris
PERSONAL
PROTECTIVE
EQUIPMENT
(PPE)
Always
wear
safety
shoes
when
working
with
the
machine.
Always
wear
ear
protectors
when
working
with
the
machine.
All
personnel
in
the
immediate
work
area
must
wear
safety
glasses
with
side
shields.
Always
wear
safety
gloves
when
changing
the
tools.
Always
wear
clothes
suitable
for
the
work
environment.
OPERATOR
The
Lavina®
S
machine.
The
operator
must
know
the
machine’s
work
environment.
Only
one
operator
at
a
time
can
work
with
the
machine.
The
operator
must
be
properly
trained
and
well
instructed
prior
operating
the
machine.
The
operator
must
understand
all
the
instructions
in
this
manual.
The
operator
must
understand
and
interpret
all
the
drawings
and
designs
in
manual.
The
operator
must
know
all
sanitation
and
safety
regulations
pertaining
to
the
operation
of
the
machine
The
operator
must
have
floor
grinding
experience.
The
operator
must
know
what
to
do
in
case
of
emergency.
The
operator
must
have
an
adequate
technical
knowledge
and
preparation.