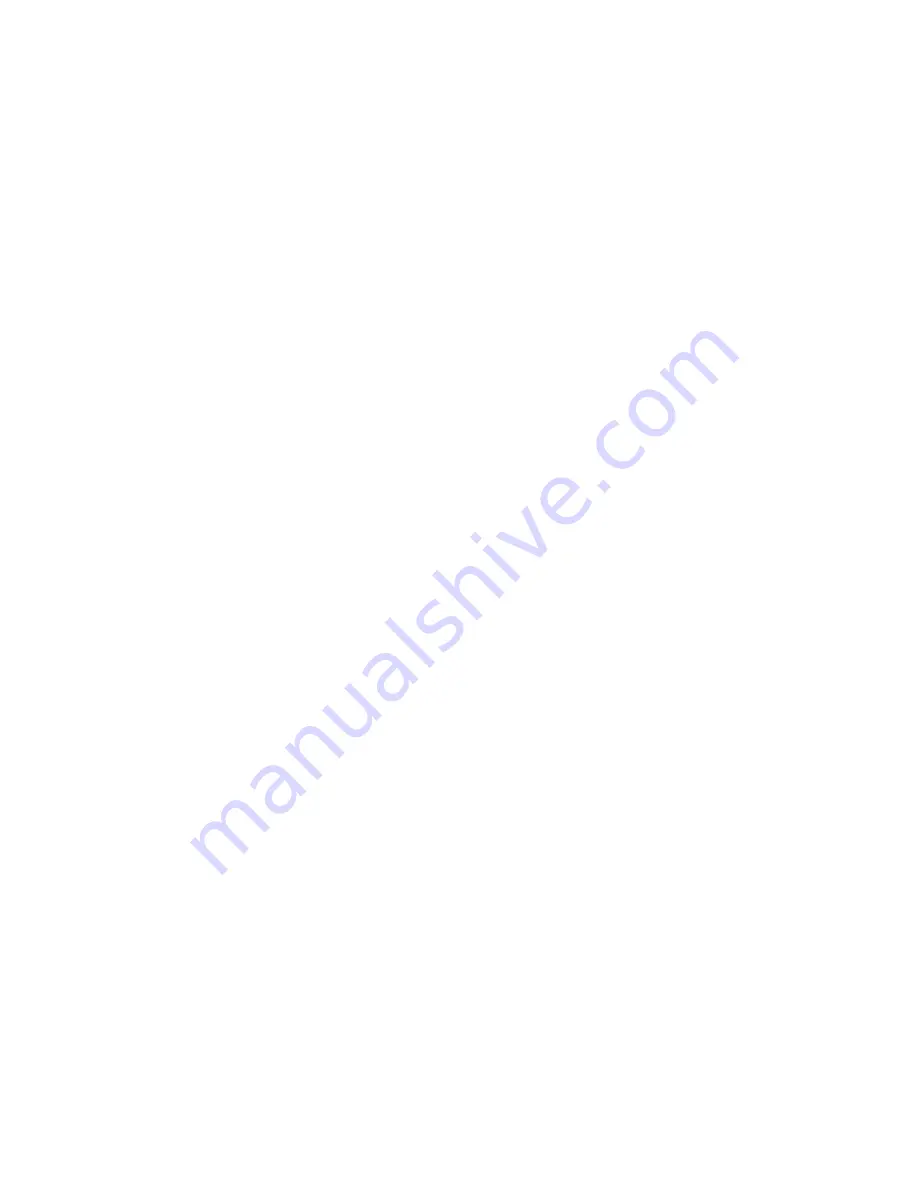
LANIER R/C
5. Score each side at the aft edge of
F3
. Bend each side inward until they
crack. This is to promote a sharp bend allowing a straight side from
F3
to the tail
so the turtledeck will fit properly.
6. Next, pull the tail together. It will be necessary to sand off some of the 1/4"
sq. at the tail to match the plans.
Tip
:
Using a thin piece of ply or metal,
cement some 100 grit paper on both sides. Holding the two sides in one
hand slide the double sided sanding stick in between and work it back and
forth while holding a slight amount of pressure on the sides. Sand enough
to match the plans and allow TW1 to fit. If done properly you should have a
good fit.
7. Z-Poxy the tail end together making sure there is no twist. Lay the fuselage
on a flat surface and check the tail post with a square. Push out two
TW1's
from
the diecut wood and laminate. Clean up edges and install with Z-Poxy.
8. Measure and cut the 1/4"sq. cross braces on the upper back of the fuselage.
Locate them from the plans. Add the 3/32" sheet to the bottom with the 36"
sheet supplied taking care not to displace the aft fuselage sides. Sheet all the
way back to the tail post.
9. Place the wing in the saddle on the fuselage. Pin it in proper alignment so
that it will not move. Match drill the dowel holes in the wing from
F2
former. Use
a long 1/4" drill. Glue in the 1/4" wing-hold-down dowels. They should protude
from
W1
no more than 5/16" with rounded ends.
10. Prepare
F1
by laminating three
F1's
together. When cured clean up the
edges and layout and drill the engine mount holes. It is much easier to do this
before installing, enabling you to use a drill press.
11. Glue in
F1
with Z-Poxy and the 1/4" x 3-3/4" x 9" ply bottom. Use Z-Poxy
here too. Add the rest of the 3/8" tri-stock where shown on the plans to complete
the front bracing. Pin the fuselage sides to
F1
, three places on each side with the
1/8" dowel supplied. Drill a 1/8" hole, apply glue to a short piece of dowel, drive in
flush with fuselage side.
12. Push out the two
FS2's
and
FS3's
from the diecut wood. Clean up the edges
and glue them in place between
F2
and
F3
on each side. Locate the
FS3
location from the plans. Cut to length and glue in the two servo rails from the
1/4" x 3/8" x 7-1/2" piece
13. Locate and glue in
HD1
, 1/4" x 1-1/4" x 3-1/2" ply, wing hold-down with Z-
Poxy. Add the 1/4" sq. pieces on each end on the bottom side to reinforce it.
Make sure it is flush with the top surface of the fuselage. Pin the fuselage sides
to
HD1
, two places on each side, with the 1/8" dowel supplied.
1995 Lanier R/C Inc.
7