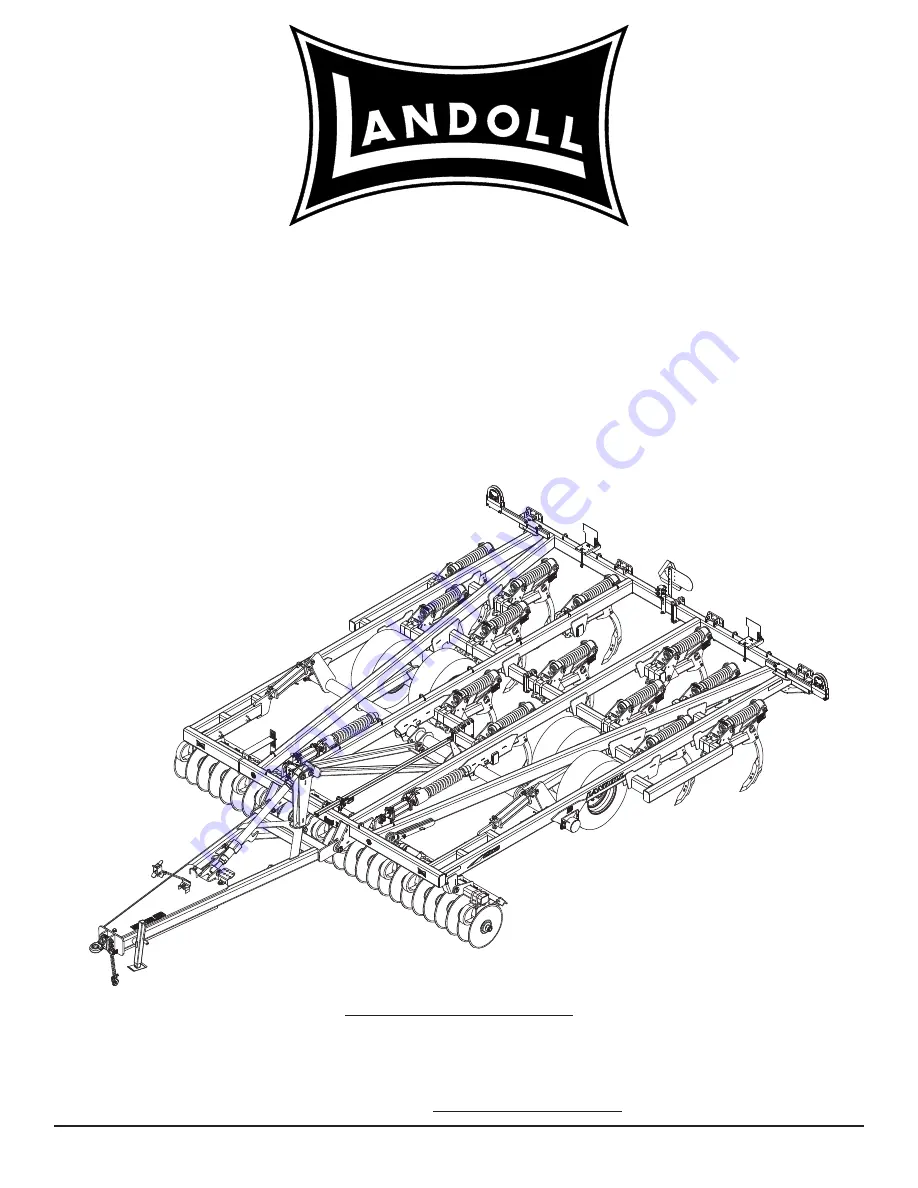
®
Model 2112
Coulter Chisel
Operator’s Manual
LANDOLL COMPANY, LLC
1900 North Street
Marysville, Kansas 66508
800-428-5655 ~ WWW.LANDOLL.COM
F-2112-0721
07/2021-Present
Summary of Contents for Coulter Chisel 2112
Page 15: ...STANDARD SPECIFICATIONS 2 7 Table provided for general use NOTES...
Page 38: ...2 30 F 1102 0721 STANDARD SPECIFICATIONS Table provided for general use NOTES...
Page 53: ...ASSEMBLY INSTRUCTIONS 3 15 Table provided for general use NOTES...
Page 61: ...ASSEMBLY INSTRUCTIONS 3 23 Table provided for general use NOTES...
Page 64: ...3 26 F 1102 0721 ASSEMBLY INSTRUCTIONS Table provided for general use NOTES...
Page 99: ...OPERATION AND MAINTENANCE 4 13 Table provided for general use NOTES...
Page 106: ...5 2 F 1102 0721 TROUBLESHOOTING GUIDE Table provided for general use NOTES...