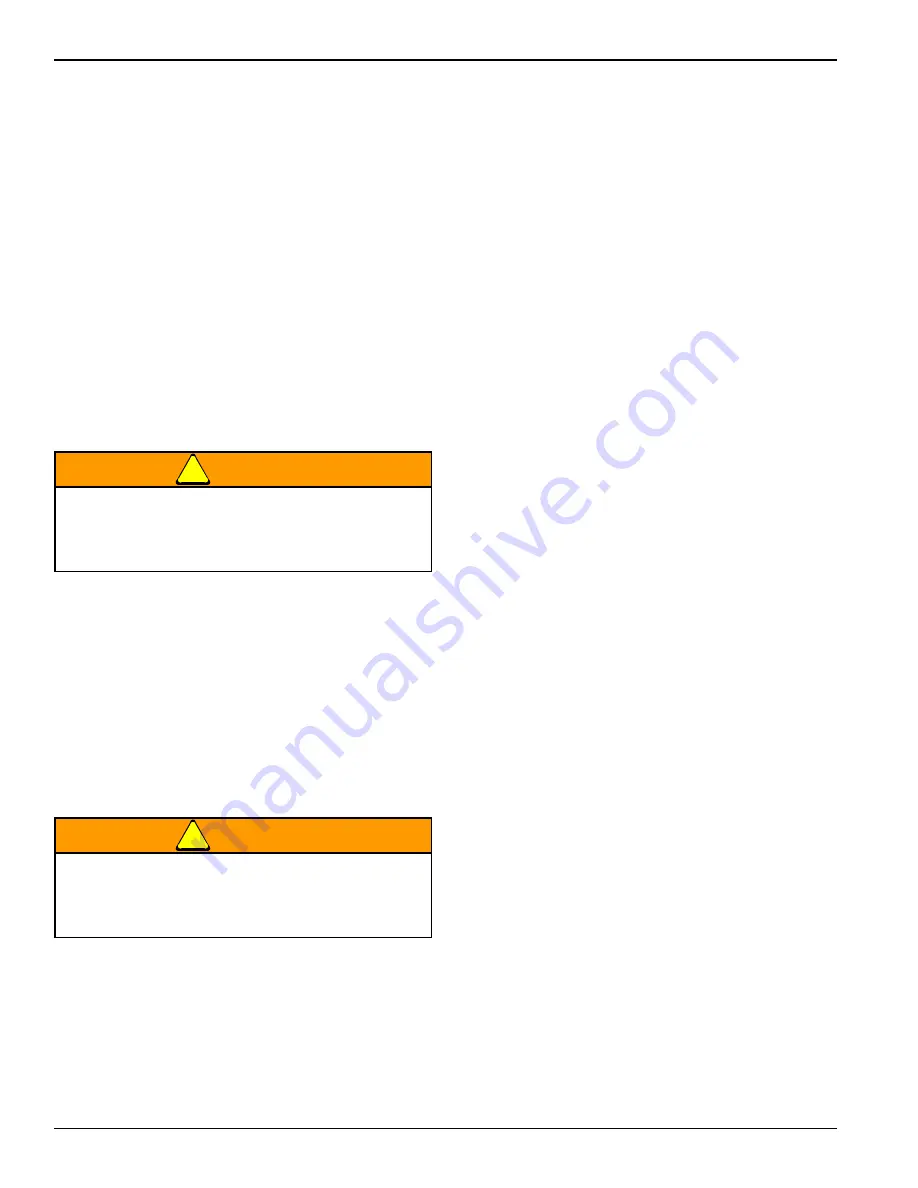
4-28
F-691-0913 Edition
MAINTENANCE AND LUBRICATION
Mounting Tire and Wheel (Hub Type)
1.
Make sure that all mounting surfaces are clean and
free of rust, dirt or paint. A wire brush may be used to
clean these surfaces
2.
Position the inner disc wheel over the studs, being
careful not to damage the stud threads. Make sure
that the disc wheel is flat against the mounting
surface and that there is clearance between the disc
wheel taper and brake drum.
3.
Position the outer disc wheel being careful not to
damage the stud threads. Be sure the valve stems for
both the inner and outer tire are accessible.
4.
Install the flange nut (pilot mount) and tighten to 50
foot-pounds using the sequence in
Then tighten to full torque of
450
to 5
0
0 foot-pounds.
5.
Torque will drop after the first 50 to 100 miles of
operation. Check the nuts for proper torque after this
interval and retighten them.
WARNING
Winches (Option)
Inspect the winch cable before and after
every
usage. If
frayed wires, nicks, kinks, worn spots, breaks or any
other sign of deterioration or damage is found, immediate
replacement is mandatory before further usage. If the
semitrailer is going to be out in the weather for any length
of time, it is advisable to oil the winch cable to prevent
untimely rusting and deterioration of the cable.
for lubrication specifications.
Inspect the winch mechanism thoroughly each week to
insure safe, efficient operation.
WARNING
Hydraulic Engine Package
(Option)
The hydraulic engine package should be inspected
weekly to insure continued proper operation. The
inspection should include:
1.
Check the hydraulic oil level weekly, or after any
leakage.
for proper hydraulic oil. With
all hydraulic cylinders in the retracted position and
with the engine stopped, check the hydraulic oil level.
2.
Check hoses weekly for cracks or leaks. If a valve or
line leaks, it should be replaced immediately.
3.
Check the engine oil each time before using. Oil level
should be maintained between the “ADD” and “FULL”
marks on the oil dip stick. For further maintenance
procedures and proper lubrication specifications,
please refer to the engine owner’s manual that was
supplied with the hydraulic engine package.
4.
Replace hydraulic filter with new filter at least every 6
months or more often under adverse conditions.
5.
Use the fuel recommended for the engine package
installed on you trailer.
Use a torque wrench to assure proper torque.
Insufficient torque can cause stud breakage and
damage wheel pilots. Overtorque can overstress
the studs and strip the threads.
Do not handle the winch cable when the winch is
in the engage position. Hands or clothing could
get caught in the cable and be pulled into the
spool causing serious personal injury.
Summary of Contents for 825D Series
Page 2: ......
Page 6: ...iv F 691 0913 Edition...
Page 14: ...2 6 F 691 0913 Edition STANDARD SPECIFICATIONS...
Page 40: ...3 26 F 691 0913 Edition OPERATING INSTRUCTIONS Page Intentionally Blank...
Page 60: ...4 20 F 691 0913 Edition MAINTENANCE AND LUBRICATION Figure 4 13 Axle and Brake Assembly...
Page 77: ...TROUBLESHOOTING GUIDE 5 9 Notes...
Page 78: ...5 10 F 691 0913 Edition TROUBLESHOOTING GUIDE...
Page 79: ......