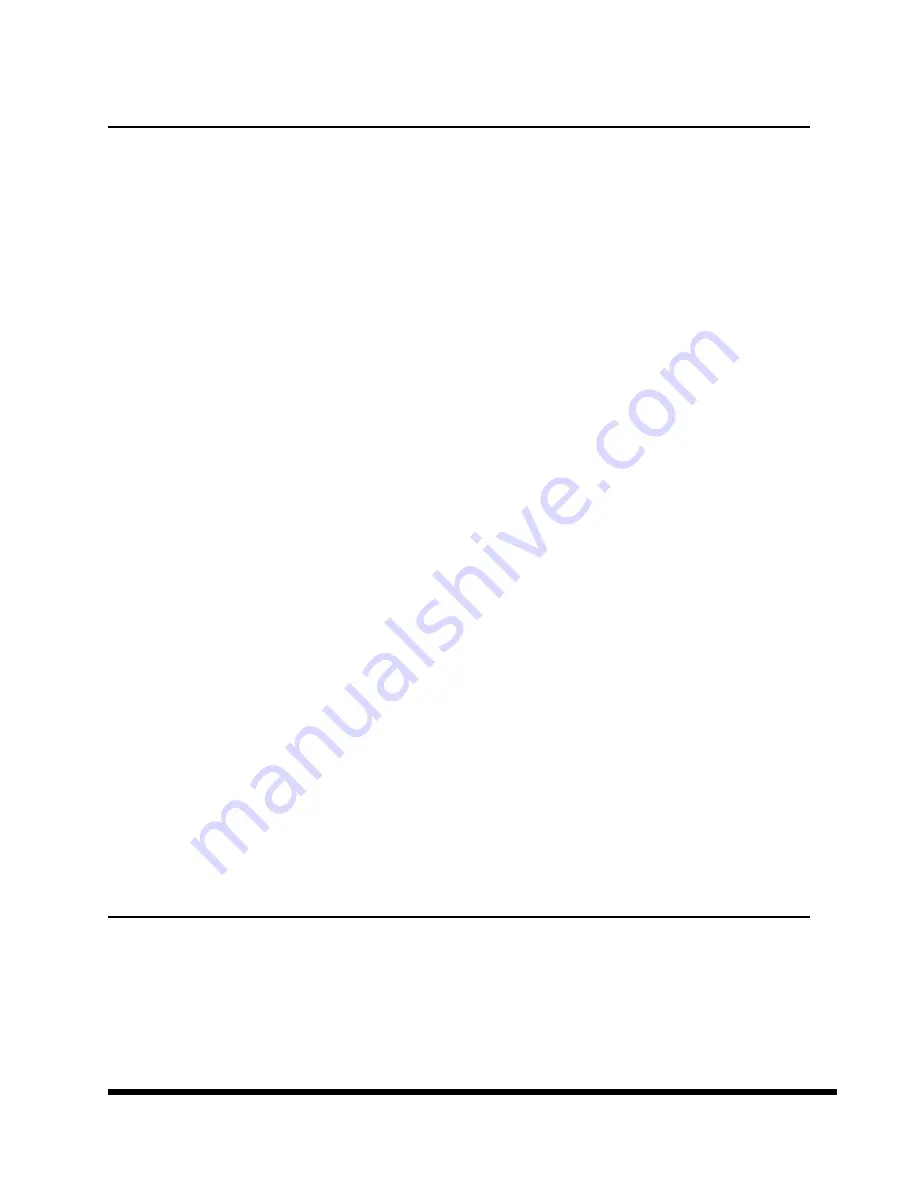
HYDRAULIC SYSTEM (CONTINUED)
SYMPTOM
PROBLEM: REMEDY
OVER HEATING OF
OIL IN SYSTEM
Oil passing through relief valve for excessive time:
return
control valve to neutral when not in use.
Incorrect, low, dirty oil:
use recommended oil. Fill reservoir
with clean oil. Replace filter.
Engine running too fast:
reduce engine speed.
Excessive component internal leakage:
repair or replace
component as necessary.
Restriction in filters or lines:
clean and/or replace filter or
lines.
Insufficient heat radiation:
clean dirt and mud from
reservoir and components.
Malfunctioning component:
repair or replace.
Excess oil going to dock level circuit:
adjust flow divider for
2.5 to 3.1 GPM flow.
FOAMING OF OIL
Incorrect, low, dirty oil:
replace, clean or add oil as needed.
Air leaks:
check suction line and component seals for suction
leaks. Replace defective parts.
NOISY PUMP
Low, incorrect, foamy oil:
replace, clean, or add oil as
needed.
Suction line plugged:
clean out obstruction or replace line.
Flush system, replace filter.
LEAKY PUMP
Damaged or worn shaft seal:
Replace seal and check
for misalignment.
Loose or broken parts:
Tighten or replace.
CYLINDERS MOVE WITH
CONTROL VALVE IN
NEUTRAL POSITION
Leaking cylinder seals or fittings:
Replace worn seals or fit-
tings.
Control valve not centering when released:
Check
linkage for
binding and repair.
Valve damaged:
Repair or replace.
CONTROL VALVE LEAKS
Seals damaged or worn:
Replace.
CYLINDER LEAKS
Seals worn or damaged:
Replace.
Rod damaged:
Replace.
Barrel damaged:
Replace.
CYLINDERS DO NOT
FUNCTION, OR CREEP
WITH PTO DISENGAGED
Leaking fittings or cylinder seals:
Tighten loose fittings.
Replace worn seals or fittings.
Piloted check valve or O-ring leak:
Replace defective compo-
nent.
5-6 HYDRAULIC POWER SUPPLY ENGINE PACKAGE
To troubleshoot the engine in the hydraulic engine package, please refer to the owners manual that
was provided with the engine package.
5-7
Summary of Contents for 345C
Page 3: ...MODEL 345C TRAILER OPERATOR S MANUAL PURCHASED FROM DATE ADDRESS PHONE NO SERIAL NO i...
Page 8: ......
Page 12: ......
Page 22: ...3 10 Figure 3 4 Steps for Loading and Unloading...
Page 26: ...3 14 Figure 3 7 Rear Impact Guard and Antilock Brake System...
Page 30: ......
Page 35: ...4 5 Figure 4 2 345C Wiring Diagram...
Page 36: ...4 6 Figure 4 3 Remote Wiring Diagram...
Page 41: ...4 11 Figure 4 5 Examples of Camber Figure 4 6 Checking Axle for Bend...
Page 46: ...4 16 Figure 4 10 Axle and Brake Assembly...
Page 63: ...5 9 NOTES...
Page 64: ......