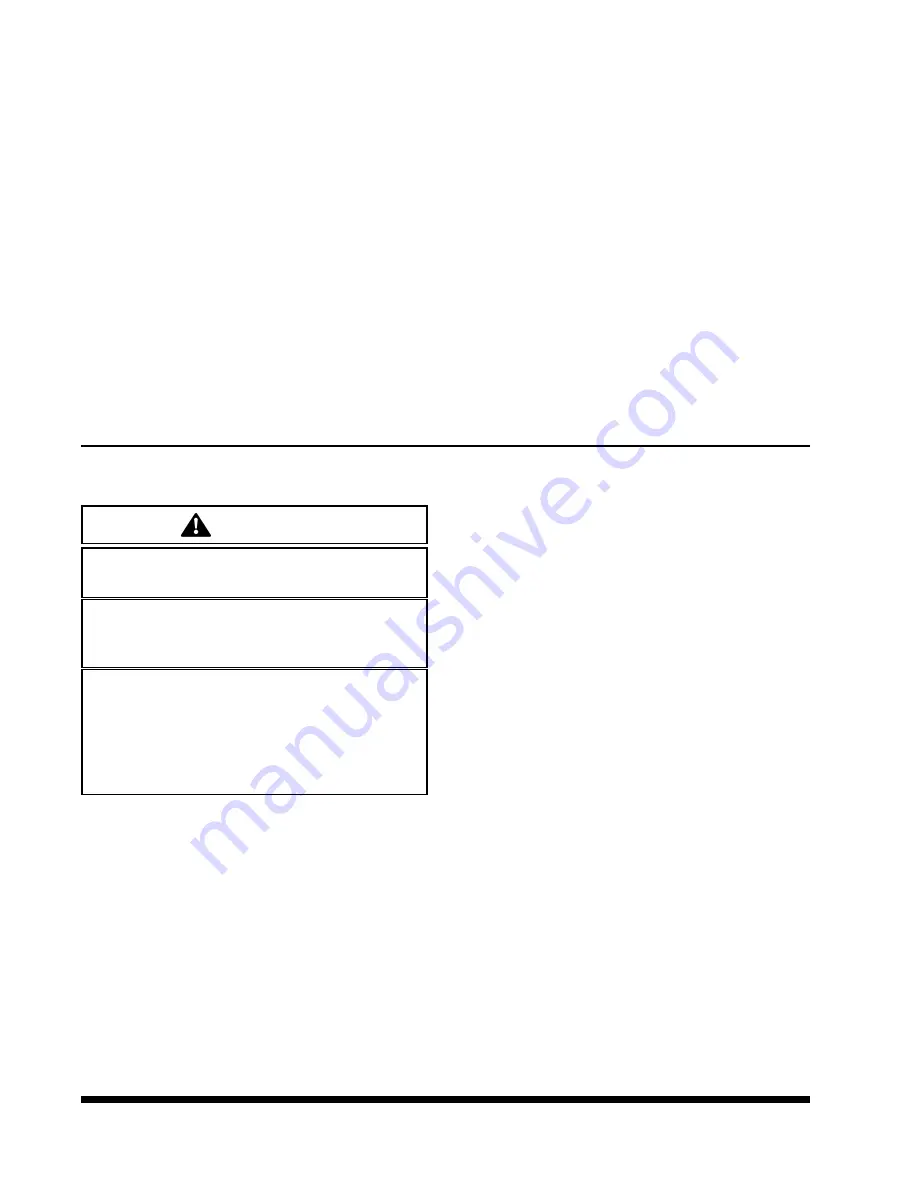
d.
Lower the trailer by exhausting air from the
air springs by moving the control arm to the
“down” position (about 45°) until the axle tube
is resting on the block.
e.
Check the ride height to make sure it is cor-
rect. Consult Landoll Service Center if correct
height cannot be obtained.
f.
Loosen the 1/4" adjusting lock nut located
on the adjusting block, allowing the control
arm to move approximately 1 inch. Move the
adjusting block until holes align, then insert lo-
cating pin.
(See Figure 4-4)
.
g.
Align the control arm linkage to the control
arm lower bracket and re-tighten the 1/4" ad-
justing lock nut to 2-4 ft.lbs. The ride height
valve should now be correctly adjusted.
h.
Remove the locating pin.
i.
The block can now be removed by using the
height control valve as an improvised jack by
disconnecting the control arm at the lower
bracket and pushing the control arm to an
“up” position.
j.
Remove the block and reconnect the link-
age. This allows the Automatic Height Control
Valve to resume normal operation.
k.
Check the air ride height. If necessary, go
through the adjustment procedure again until
the proper air ride height is achieved.
l.
Check the air ride height periodically and
adjust as needed.
4-7 ALIGNMENT
4-7.1
Wheel Alignment
DANGER
TO PREVENT A LIFE THREATENING
ACCIDENT:
1. SUPPORT TRAILER AND UNDER-
CARRIAGE SO TIRES ARE OFF THE
GROUND.
2. SUPPORT THE TRAILER AND UN-
DERCARRIAGE ON JACK STANDS
WITH SUFFICIENT CAPACITY TO SUP-
PORT THE TOTAL WEIGHT OF THE
TRAILER AND ANY LOAD WHICH IT
MAY BE CARRYING.
When trailer tires show signs of scuffing,
feather-edging or uneven wear, examine the trailer
for damaged suspension (frame, shocks, linkage,
etc.), axle, wheel bearings and wheels. Proper
wheel alignment and wheel bearing adjustment is
essential for proper tire wear. The simplest form of
checking wheel alignment “toe” is by running the
trailer over a “SCUFF GAUGE”. A scuff gauge
reading of 16 feet or less per mile is considered
satisfactory. If a scuff gauge is not readily avail-
able, or edge wear on one side of a tire is occur-
ring signifying positive or negative camber, align-
ment can be checked as follows:
a.
Remove wheel, hub and bearing assem-
blies.
b.
Place a 3-point axle gauge against the front
side of the axle, and adjust each axle gauge
point to the axle. (Double point end against
the inner and outer wheel bearing surfaces of
the spindle being checked and the other point
on the inner bearing surface on the other
spindle.)
(See Figure 4-6).
c.
Move the axle gauge and place against the
back side of the axle. If either of the points of
double point end fails to touch the axle sur-
face, a bent spindle is evident. A point gap of
.015" or more is considered excessive tire
“toe” and the axle must be replaced
(See Fig-
ure 4-6)
.
4-10
Summary of Contents for 345C
Page 3: ...MODEL 345C TRAILER OPERATOR S MANUAL PURCHASED FROM DATE ADDRESS PHONE NO SERIAL NO i...
Page 8: ......
Page 12: ......
Page 22: ...3 10 Figure 3 4 Steps for Loading and Unloading...
Page 26: ...3 14 Figure 3 7 Rear Impact Guard and Antilock Brake System...
Page 30: ......
Page 35: ...4 5 Figure 4 2 345C Wiring Diagram...
Page 36: ...4 6 Figure 4 3 Remote Wiring Diagram...
Page 41: ...4 11 Figure 4 5 Examples of Camber Figure 4 6 Checking Axle for Bend...
Page 46: ...4 16 Figure 4 10 Axle and Brake Assembly...
Page 63: ...5 9 NOTES...
Page 64: ......