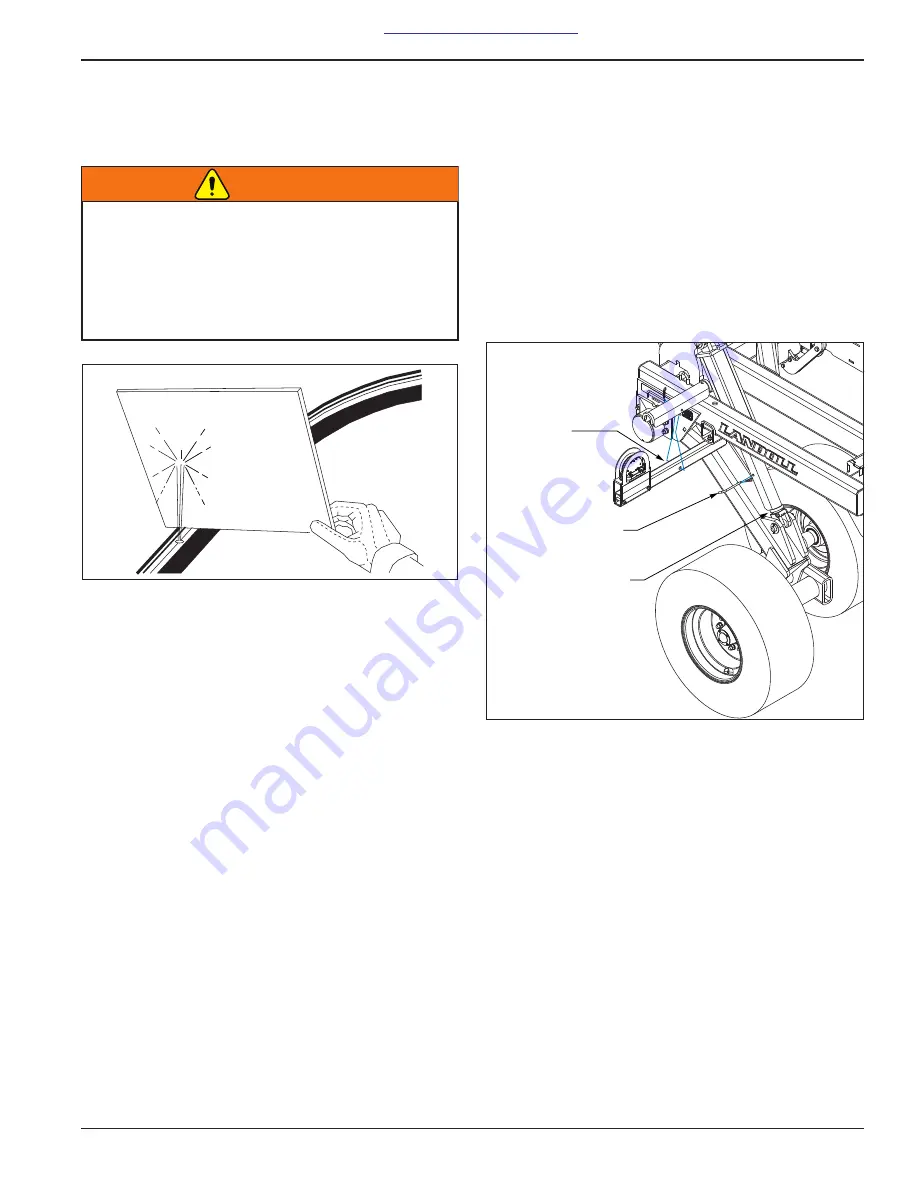
4-3
Hydraulic Lift System
The Weatherproofer is equipped with a hydraulic lift
system to raise and lower the unit in the field.
WARNING
Figure 4-2: Hydraulic Leak Detection
1.
The hydraulic lift system contains cylinders plumbed
together. It is important that the cylinders be
connected in the proper series for the lift system to
operate correctly.
2.
The hydraulic system is not filled with oil and should
be purged of air before transporting and field
operations. Carefully hitch the Weatherproofer to the
tractor and connect the hydraulic lift hoses. Check to
make sure the tractor hydraulic reservoir is full of the
manufacturer’s recommended oil. Slowly raise the
machine. With all cylinders fully extended remove the
transport lockouts
Store transport
lockouts on light bracket assemblies
.
Lower and raise
the
unit
to
verify
that
cylinders
are
working
simultaneously throughout the stroke. Do not loosen
any hoses or fittings. Recheck tractor reservoir to
make sure it is within operating limits.
Figure 4-3: Transport Locks
Escaping hydraulic fluid can cause serious
personnel injury. Relieve system pressure before
repairing, adjusting, or disconnecting. Wear
proper hand and eye protection when searching
for leaks. Use cardboard instead of hands
. Keep all components (cylinders,
hoses, fittings, etc.) in good repair.
TRANSPORT LOCK
STORED POSITION
LIGHT BRACKET
ASSEMBLY
TRANSPORT LOCK
INSTALLED POSITION
L PIN, 1/8 HAIRPIN
Summary of Contents for 2411
Page 4: ......
Page 25: ...2 7 TABLE OF CONTENTS Table provided for general use NOTES...
Page 39: ...3 5 TABLE OF CONTENTS Table provided for general use NOTES...
Page 47: ...3 13 TABLE OF CONTENTS Table provided for general use NOTES...
Page 53: ...3 19 TABLE OF CONTENTS Table provided for general use NOTES...
Page 72: ...3 38 F 1130 2304 TABLE OF CONTENTS Table provided for general use NOTES...
Page 83: ...3 49 TABLE OF CONTENTS Table provided for general use NOTES...
Page 85: ...3 51 TABLE OF CONTENTS Figure 3 1 3BCT Chopper Hydraulic Layout 2411 06...
Page 112: ...5 4 F 1130 2304 TABLE OF CONTENTS Table provided for general use NOTES...
Page 114: ...6 2 F 1130 2304 TABLE OF CONTENTS Table provided for general use NOTES...