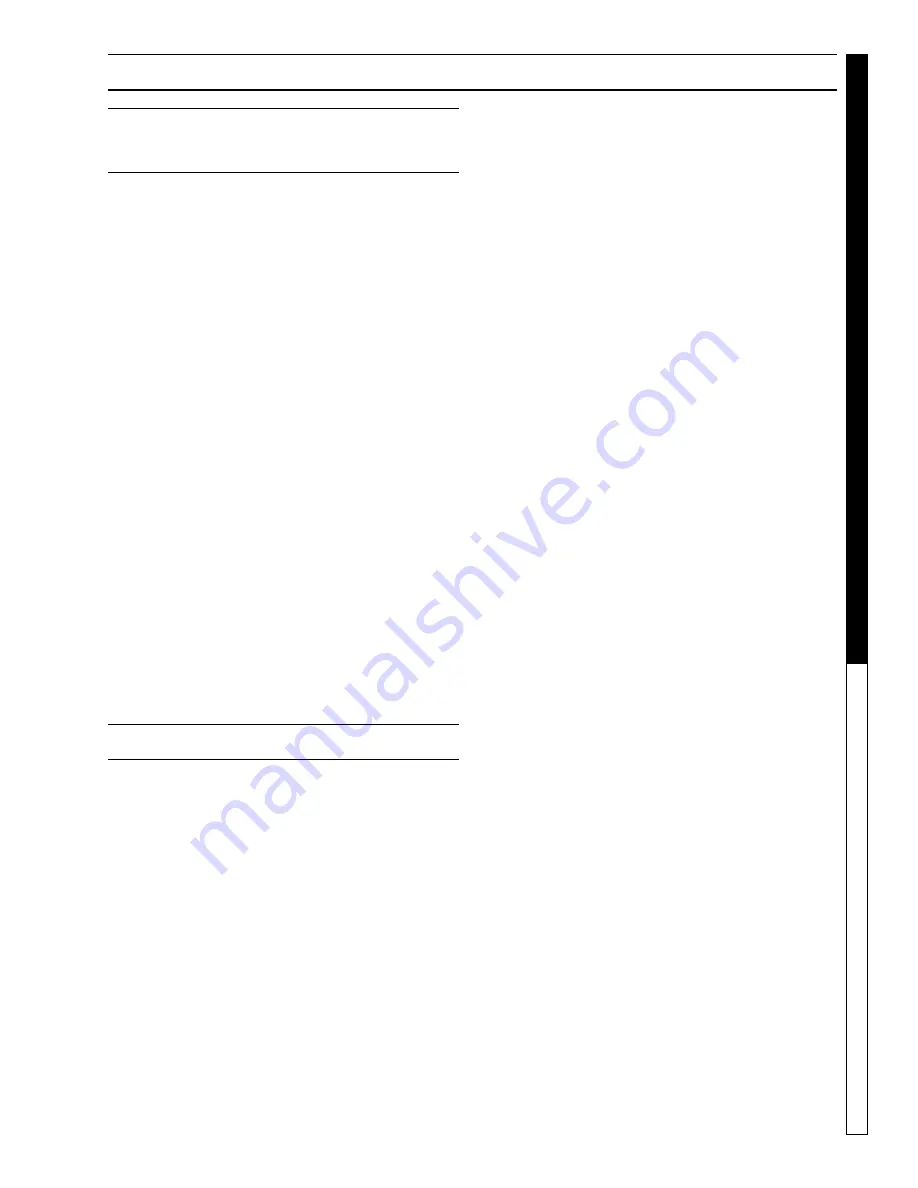
96-610 • LANDA VNG/VLP • REV. 9/05
15
PRESSURE
W
ASHER
OPERA
T
OR’S MANU
AL
MAINTENANCE
PREVENTATIVE
MAINTENANCE
1. Check to see that water pump is properly lubri-
cated.
2. Follow Winterizing Procedures to prevent freeze
damage to the pump and coils.
3. Always neutralize and flush detergent from sys-
tem after use.
4. If water is known to be high in mineral content, use
a water softener in your water system or de-scale
as needed.
5. Do not allow acidic, caustic or abrasive fluids to be
pumped through the system.
6. Always use high grade quality Landa cleaning prod-
ucts.
7. Never run pump dry for extended periods of time.
Shut off timer will be set for two minutes.
8. Periodically delime coils per instructions.
It is advisable, periodically, to visually inspect the
burner. Check air inlet to make sure it is not clogged or
blocked. Wipe off any oil spills and keep this equip-
ment clean and dry.
The areas around the Landa washer should be kept
clean and free of combustible materials, gasoline and
other flammable vapors and liquids.
The flow of combustion and ventilating air to the burner
must not be blocked or obstructed in any manner.
Note: Pump damage may occur if ran in bypass longer
than two minutes.
MAINTENANCE AND SERVICE
Spray Nozzles
Each machine is equipped with one or more spray
nozzles, depending on model. Different spray nozzles
are calibrated for each machine depending on the flow
and pressure of that particular model. Spray nozzles
vary in bore size and angle of spray. Popular spray
angles are 0°, 15°, 25°, 40°. When ordering, please
specify size and angle of nozzle. Nozzle size for each
machine is located on the serial plate.
Unloader Valves:
Unloader valves are preset and tested at the factory
before shipping. Occasional adjustment of the unloader
may be necessary to maintain correct pressure.
Winterizing Procedure:
Damage due to freezing is not covered by warranty.
Adhere to the following cold weather procedures when-
ever the washer must be stored or operated outdoors
under freezing conditions.
During winter months, when temperatures drop below
32°F, protecting your machine against freezing is nec-
essary. Siphoning a small amount of antifreeze into the
system is recommended. This is done by pouring a
50:50 mix of antifreeze and water into the float tank
and then siphoning 100% antifreeze through the de-
tergent line with the pump on. If compressed air is avail-
able, an air fitting can be screwed into the float tank
strainer fitting and by injecting compressed air, all wa-
ter will be blown out of the system. The use of a draft
diverter will prevent the wind chill factor from freezing
the coil.
Low Pressure Diagnosis
(Machines with shut-off spray gun)
Refer to the Troubleshooting Chart for low pressure. If,
after referring to the chart, the trouble is found to be
either the unloader or the pump, your next step is to
determine which one is the problem. This can be done
by eliminating the unloader from the system and at-
taching a 50' discharge hose directly to the pump. If
high pressure is developed in this manner the pump is
good, and the unloader needs to be repaired or re-
placed. If low pressure is still present the pump needs
repairing.
CAUTION: When using this procedure to test com-
ponents, keep the spray gun open at all times.
High Limit Hot Water Thermostat:
For safety, each machine is equipped with a high limit
control switch. In the event the temperature of the wa-
ter should exceed its operating temperature, the high
limit control will turn the burner off until the water cools.
Pumps:
Use only SAE 30 weight non-detergent oil. Change oil
after first 50 hours of use. Thereafter, change oil every
three months or at 500 hour intervals. Oil level should
be checked through use of the dipstick found on the
top of the pump or by the red dot visible through the oil
gauge window. Oil should be maintained at that level.
Summary of Contents for VNG4-2000
Page 2: ......
Page 54: ......
Page 56: ...Form 96 610 Revised 9 05 Printed in U S A WATER CLEANING SYSTEMS...