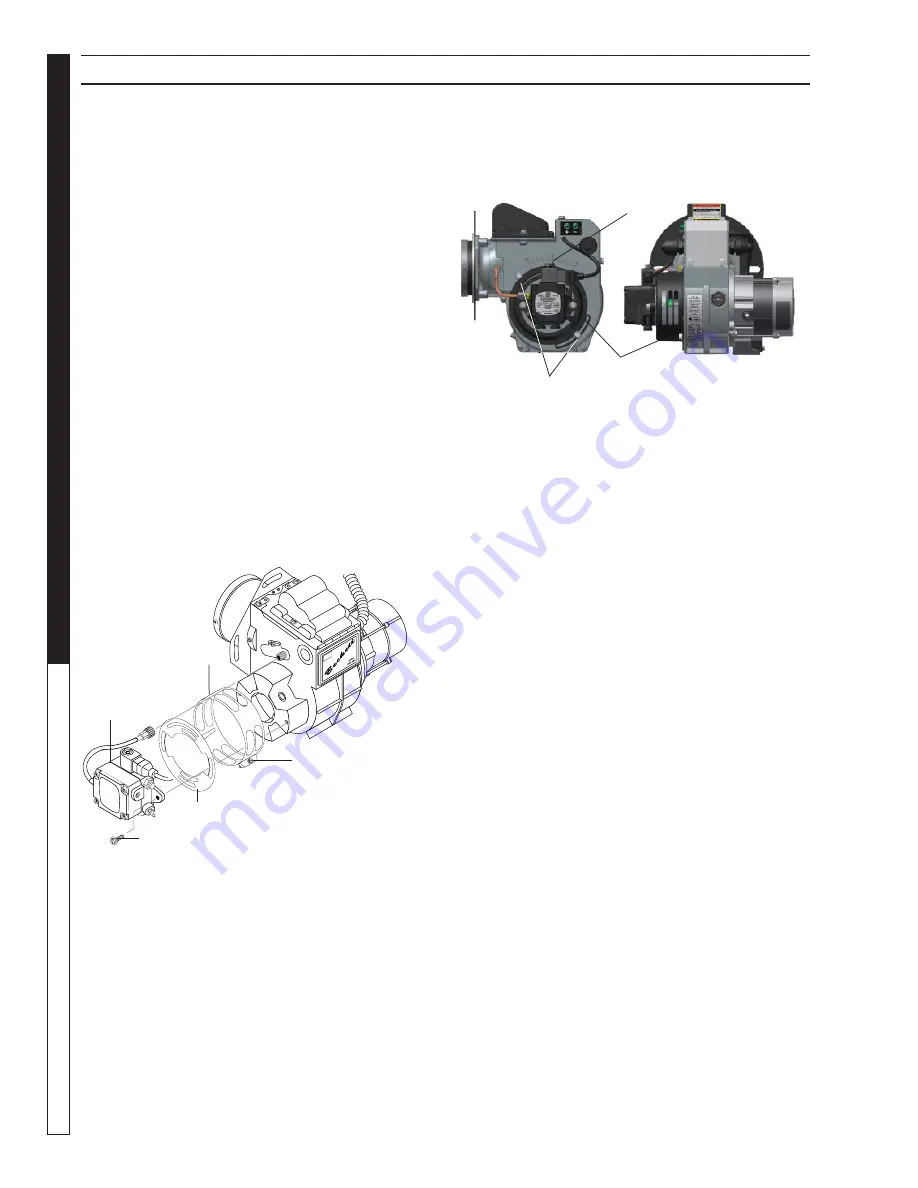
8.917-208.0 • HOT Operator Manual • Rev. 03/12
OPERA
T
OR’S MANU
AL
PRESSURE W
ASHER
14
moved to allow the air to fl ow through the burner.
Sharp eye-burn ing white fumes indicate too much
air fl owing through the com bus tion chamber. The
air band should be moved to al low less air to fl ow
through the burn er.
To Adjust:
Start machine and turn burner ON.
Loosen two locking screws found in the air shutter
openings (re fer to illustration) and close air shutter
until black smoke ap pears from burner exhaust vent.
Note air band po si tion. Next, slow ly open the air
shutter until white smoke just starts to appear. Turn
air shutter halfway back to the black smoke position
previously noted. Tight en lock ing screws.
If the desired position cannot be obtained using
only the air shutter, lock the air shutter in as close a
position as can be obtained, then repeat the above
procedure on the air band setting.
Initial Air Adjustments:
Allow suffi cient air to obtain
a clean burning fl ame by loosening the lock screws
and moving the air shutter and if necessary the bulk
air band.
Reduce the air supply until the fl ame tips appear
slight ly smoky, then increase the air just enough to
cause the fl ame tips to appear absolutely clean.
Landa Sure Fire Oil Burner
Burner Air Adjustment:
The oil burner on this
machine is preset for operation at altitudes below
1000 feet. If operated at higher altitudes, it may
be necessary to adjust the air band for a #1 or #2
smoke spot on the bacharach scale.
To adjust, start machine and turn burner ON. Loosen
two locking screws found on the air band and close
air band until black smoke appears from burner
exhaust vent. Note air band position. Next, slowly
open the air band until white smoke just starts to
appear. Turn air band halfway back to the previously
noted position. Tighten locking screws.
CAUTION: If white smoke appears from burner
exhaust vent during start-up or operation,
discontinue use and readjust air bands.
NOTE: If a fl ue is installed, have a professional
serviceman adjust your burner for a #1 or #2
smoke spot on the Bacharach scale.
Removal of Soot and Heating Coil
In the heating process, fuel residue in the form of
soot deposits may develop between the heat ing
coil pipe and block air fl ow which will affect burner
combustion. When soot has been de tect ed on visual
observation, the soot on the coil must be washed off.
Follow these steps to re move the coil.
1. Disconnect hose from pump to inlet side of the coil.
2. Disconnect electrical connection to the ther mo stat.
3. Remove quick coupler from inlet and discharge side
of coil.
4. Re move bur n er as sem bly from combustion
cham ber.
5. Re move the 3-3/8" bolts from each side of coil and
tank as sem bly (these bolts are used to fasten tank
and handles to chassis).
6. Dis con nect 1/2" pipe nipples from inlet and dis charge
side of coil.
7. Re move top tank wrap exposing in su la tion and coil
and fold back in su la tion.
8. Re move bolts that hold down coil to bot tom wrap.
9. Re move coil.
10. Replace or repair any insulation found to be torn or
broken.
Coil Reinstallation
Reinstall new or cleaned coil by reversing Steps 9
through 1 above.
MAINTENANCE & SERVICE
Air
Band
Beckett
Fuel
Pump
Air Adjustment
Screw
Air Shutter
Locking Screws
Reference Numbers
Air Band Locking Screws
Air Band