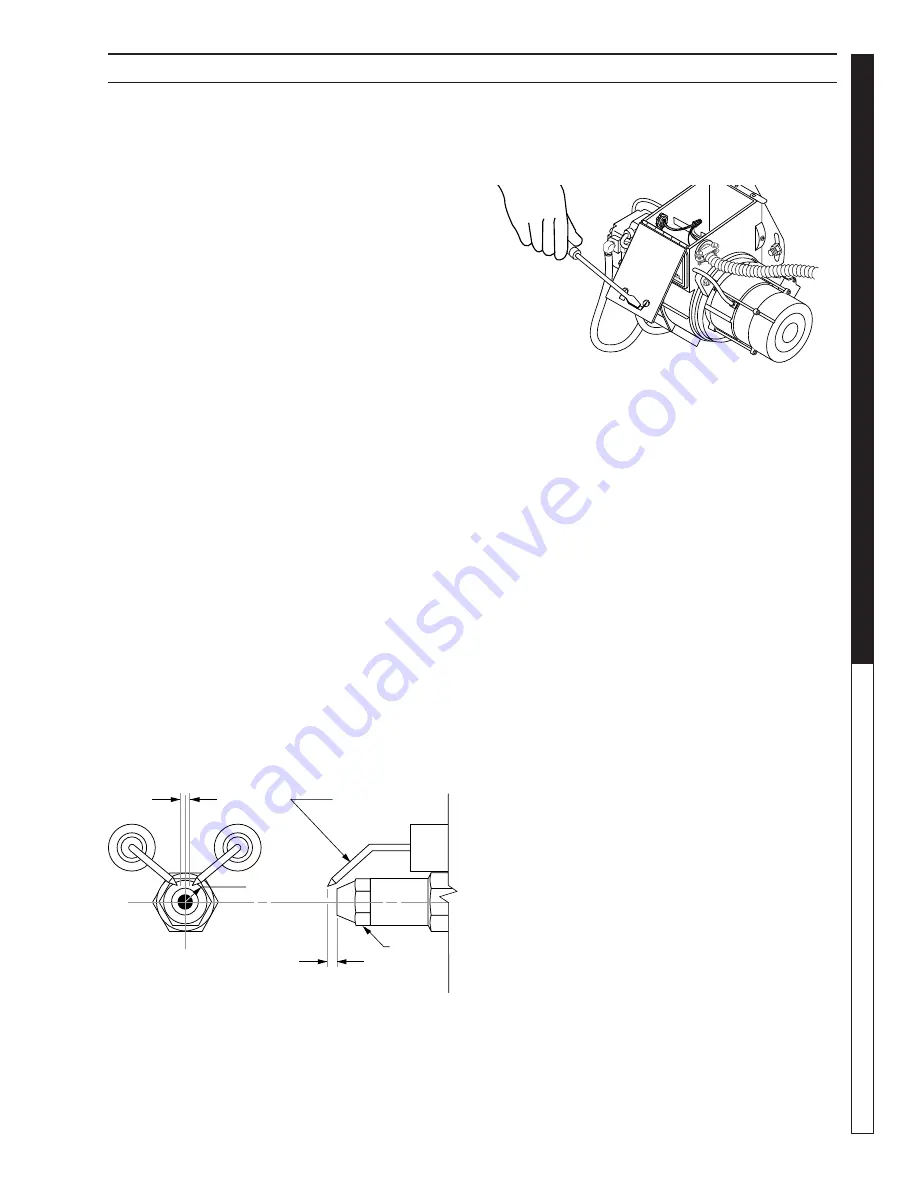
8.917-208.0 • HOT Operator Manual • Rev. 03/12
13
PRESSURE W
ASHER
OPERA
T
OR’S MAN
U
AL
MAINTENANCE & SERVICE
Step 3
Attach a short section (3-5 ft.) of garden hose
to machine to siphon solution from an el e vat ed
con tain er. Turn machine on, allowing solution
to be pumped through coils back into the con -
tain er. So lu tion should be allowed to circulate
2-4 hours.
Step 4
After circulating solution fl ush entire system with
fresh water. Reinstall high pressure noz zle into
wand.
Rupture Disk
If pressure from pump or thermal expansion should
ex ceed safe limits, the rupture disk will burst, allow-
ing high pressure to be discharged through hose
to ground. When the disk ruptures it will need to be
replaced. Torque the re place ment rupture disk to 35
foot pounds.
Fuel
Use clean fuel oil that is not contaminated with water
and debris. Replace fuel fi lter and drain tank every
100 hours of operation. Use No. 1 or No. 2 Heating
Oil (ASTM D306) only.
NEV ER
use gasoline in your
burn er tank. Gas o line is more com bus ti ble than fuel
oil and could re sult in a se ri ous ex plo sion.
NEVER
use crank case or waste oil in your burn er. Fuel unit
mal func tion could re sult from con tam i na tion.
Biodiesel fuels are becoming more popular as alter-
native fuels under the Green Initiative. Landa en-
dores the use of fuels that are blended with biodies-
els meeting ASTM D6751 and petroleum
fuels meeting ASTM D396. Landa offers no
opinion regarding the combustion characteristics
of B5 blends. B5 biodiesel fuels are 5% ASTM
D6751 biodiesel and 95% ASTM D396 fuel oil blend.
Electrode Setting
(See illustration below.)
Ignition Circuit
Pe ri od i cal ly inspect wires, spring contact and elec-
trodes for condition, security and proper spacing.
Trans form er test:
(CAU TION 10,000 VOLTS)
use
defect free in su lat ed screw driv er and keep fi ngers
Side View
Top View
1/16"
7/16"
5/32" Gap
Electrode
Nozzle
off blade! Lay blade across one contact: OK if arc
will span 1/2" between end of blade and other
contact (see illustration below).
Transformer Check
Burner Nozzle
Keep the tip free of sur face de pos its by wip ing it with
a clean, sol vent-sat u rat ed cloth, being care ful not to
plug or en large the nozzle. For max i mum ef fi
cien cy,
re place the nozzle each sea son.
Fuel Control System
These machines utilize a fuel solenoid valve located
on the fuel pump to control the fl ow of fuel to the
com bus tion chamber. This solenoid, which is nor-
mally closed, is ac ti vat ed by the unloader's pressure
switch. When an op er a tor re leas es the trigger on the
spray gun, the un load er goes into a by-pass mode,
thus stop ping elec tri cal cur rent to the fuel solenoid
coil. With the solenoid closed, the fuel supply to the
combustion cham ber ceas es. Pe ri od ic in spec tion to
insure that the fuel so le noid valve func tions properly
is rec om mend ed. This can be done by op er at ing the
machine and check ing to see that when the spray
gun is in the OFF po si tion the burn er is not fi ring.
Fuel Pressure Adjustment:
To ad just fuel pres sure, turn the ad just ing screw
(lo cat ed at the reg u la tor port) clock wise to in crease,
coun ter clock wise to decrease. Do not exceed 200 psi.
NOTE:
When chang ing fuel pump, a by-pass plug
must be in stalled in return line port or fuel pump
will not prime.
Beckett Burner Air Adjustment
The oil burner on this machine is preset for opera-
tion altitudes below 1000 feet. If operated at higher
altitudes, it may be necessary to adjust the air band
setting. Adjust air band for a #1 or #2 smoke spot
on the Bacharach scale.
If a smoky or eye-burn ing ex haust is being emit ted
from the stack, two things should be checked. First,
check the fuel to be cer tain that ker o sene or No. 1
home heating fuel is be ing used. Next, check the air
ad just ment on the burn er. An oily, black, smoky fi re
indicates a lack of air and the air band should be