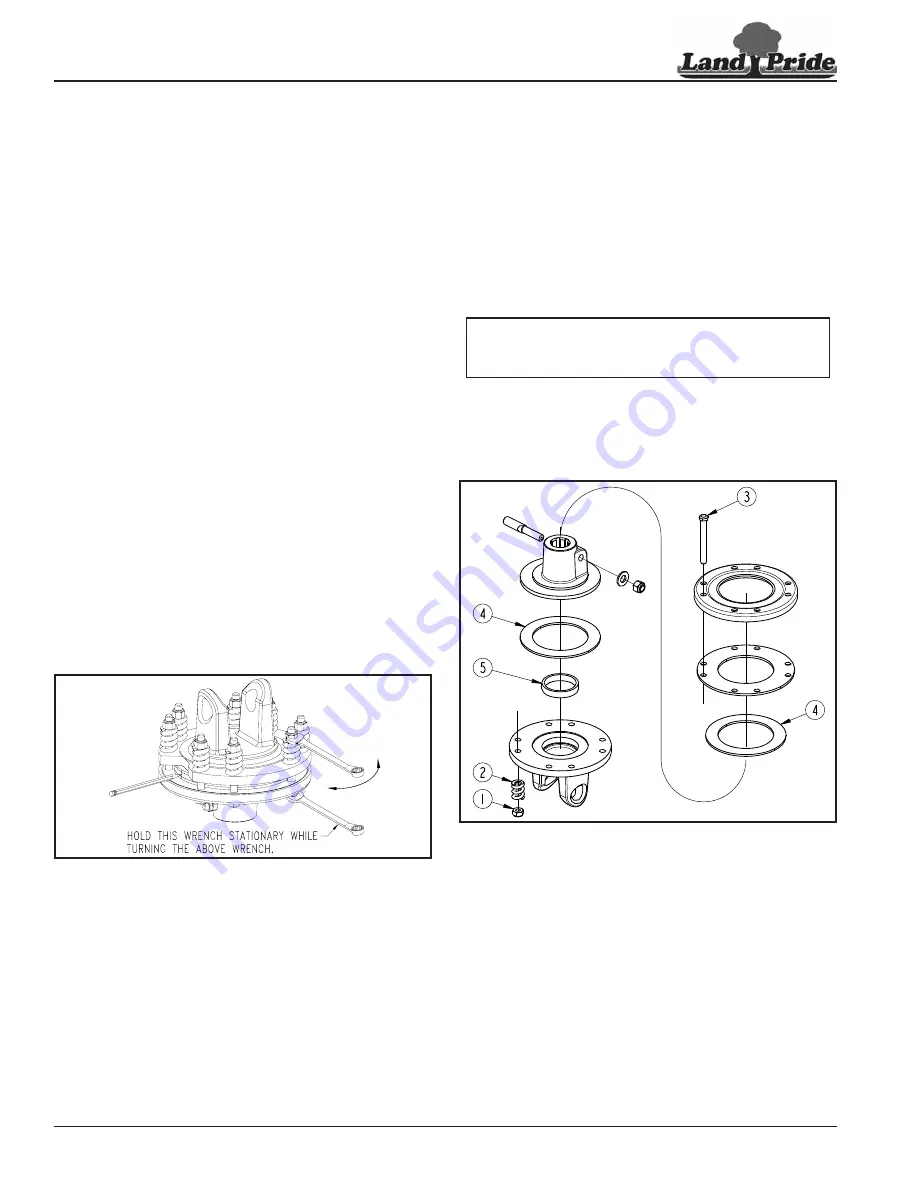
Section 4: Maintenance and Lubrication
RGR12 & RGA12 Series Rotary Tillers 311-948M
1/7/19
24
Driveline Protection
Tiller drive components are protected from shock loads
with a two plate friction clutch.
Friction clutches should be “run-in” prior to initial
operation and after long periods of inactivity to remove
any oxidation that may have accumulated on the friction
surfaces. Repeat “run-in” instructions at the beginning of
each season and when moisture and/or condensation
seizes the inner friction plates.
Clutch Run-In
The clutch must be capable of slippage during operation
to protect gearbox, driveline and other drivetrain parts.
Friction clutches should be “run-in” prior to initial
operation and after long periods of inactivity. To prevent
driveline and gearbox damage, repeat clutch “run-in” at
the beginning of each season and when moisture and/or
condensation seizes the inner friction plates.
1.
Using a pencil or other marker scribe a line across the
exposed edges of the clutch plates and friction disks.
2. Carefully loosen each of the 8 spring retainer nuts by
exactly 2 revolutions. It will be necessary to hold the
hex end of the retainer bolt in order to count the exact
number of revolutions.
3. Start tractor and engage driveline for 2-3 seconds to
permit slippage of clutch plate and disk surfaces.
Disengage driveline and re-engage a second time for
2-3 seconds.
4. Shut tractor down before dismounting using
Clutch Run-In
Figure 4-3
5. Inspect clutch and ensure that the scribed markings
made on the clutch plates have changed position.
Slippage has not occurred if any two marks on the
friction disk and plate are still aligned. A clutch that
has not slipped must be disassembled to separate
the clutch plates from the friction disks. See
instructions below.
6. Tighten each of the 8 spring retainer nuts on the
clutch housing exactly 2 revolutions to restore clutch
to its original setting pressure.
30560
7.
The clutch should be checked during the first hour of
operation and periodically each week. An additional
set of scribe marks can be added to check for
slippage. See
to adjust for
proper spring length.
Clutch Disassembly
If the clutch run-in procedure, (See
page 24), indicated that one or more of the friction disks did
not slip, the clutch must be disassembled to separate the
friction discs.
Refer to Figure 4-4:
See
IMPORTANT NOTE
above before disassembling
clutch. After measuring and recording each spring
length, remove spring retainer nuts (#1), springs (#2) and
bolts (#3). Each friction disc (#4) must then be separated
from the metal surface adjacent to it.
Clutch Disassembly/Assembly
Figure 4-4
Inspection
Inspect all parts for excessive wear and condition. Clean
all parts that do not require replacement.The original
friction disk thickness is 1/8" and should be replaced if
the thickness falls below 3/32". If the clutch has been
slipped to the point of “smoking”, the friction disks may be
damaged and should be replaced. Heat build-up may
also affect the yoke joints.
30557