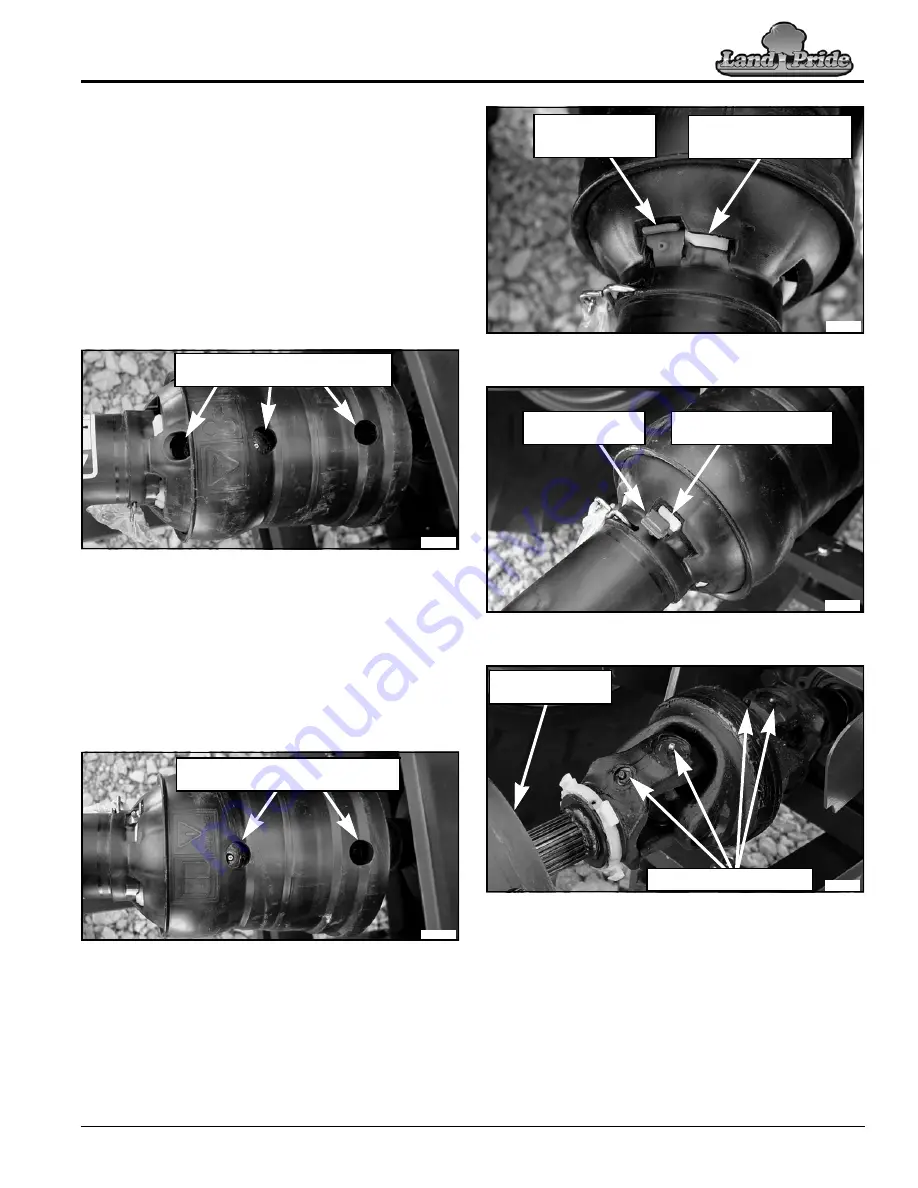
Section 5: Maintenance & Lubrication
8/22/23
RC4615 & RCM4615 Rotary Cutters 331-644M
55
Accessing CV Driveline Joints
Refer to Figure 5-13 on page 54:
There are two ways the constant velocity driveline joints
shown in Figure 5-13 can be accessed for lubrication.
One is through holes in the driveline shield and the other
is to slide the shields back to expose the grease zerks.
Lubrication Through Access Holes
1.
Refer to
Rotate driveline shield until
holes in shield align with grease zerks in CV joint.
2.
Apply proper amount and type of lubrication. Refer to
on page 54 for
quantities and type of lubrication.
Lubrication Through Three Holes In Driveline Shield
Figure 5-14
3.
Refer to
Rotate driveline shield 180
o
until holes on opposite side of shield aligns with
remaining grease zerks in CV joint.
4.
Repeat step 2 above on any grease zerks that were
not greased in step 2.
5.
Steps 1 to 2 can be repeated to lubricate universal
joint on opposite end of driveline. (Opposite end of
driveline has only one grease zerk.)
Lubrication Through Two Holes In Driveline Shield
Figure 5-15
Lubrication By Sliding Driveline Shields Back
1.
Refer to
With a flat bladed screwdriver
or similar tool, pry top of red locking tab up.
2.
Refer to
Rotate white locking ring fully
counterclockwise to the position shown.
3.
Refer to
Pull back on driveline shielding
until CV joint is exposed.
Rotate Driveline Shield to Align
3-Holes in Shield With Grease Zerks
33992
33993
Rotate Driveline Shield to Align
2-Holes in Shield With Grease Zerks
Locked Driveline Shield
Figure 5-16
Unlocked Driveline Shield
Figure 5-17
Slide Driveline Shield Back To Expose Grease Zerks
Figure 5-18
4.
Apply proper amount and type of lubrication. Refer to
on page 54 for
quantities and type of lubrication.
5.
Slide driveline shield back to its operating position.
6.
Refer to
Rotate white locking ring
clockwise and press locking tab down until it snaps in
place as shown.
7.
Steps 1 to 6 can be repeated to lubricate universal
joint on opposite end of driveline.
Red Locking Tab
Snapped Down
Into Position
White Locking Ring
Positioned On Right Side
of Red Locking Tab
33994
Red Locking Tab
Pried Up
White Locking Ring
Rotated Counterclockwise
33995
Driveline Shield
Pulled Back
Exposed CV Grease Zerks
33996