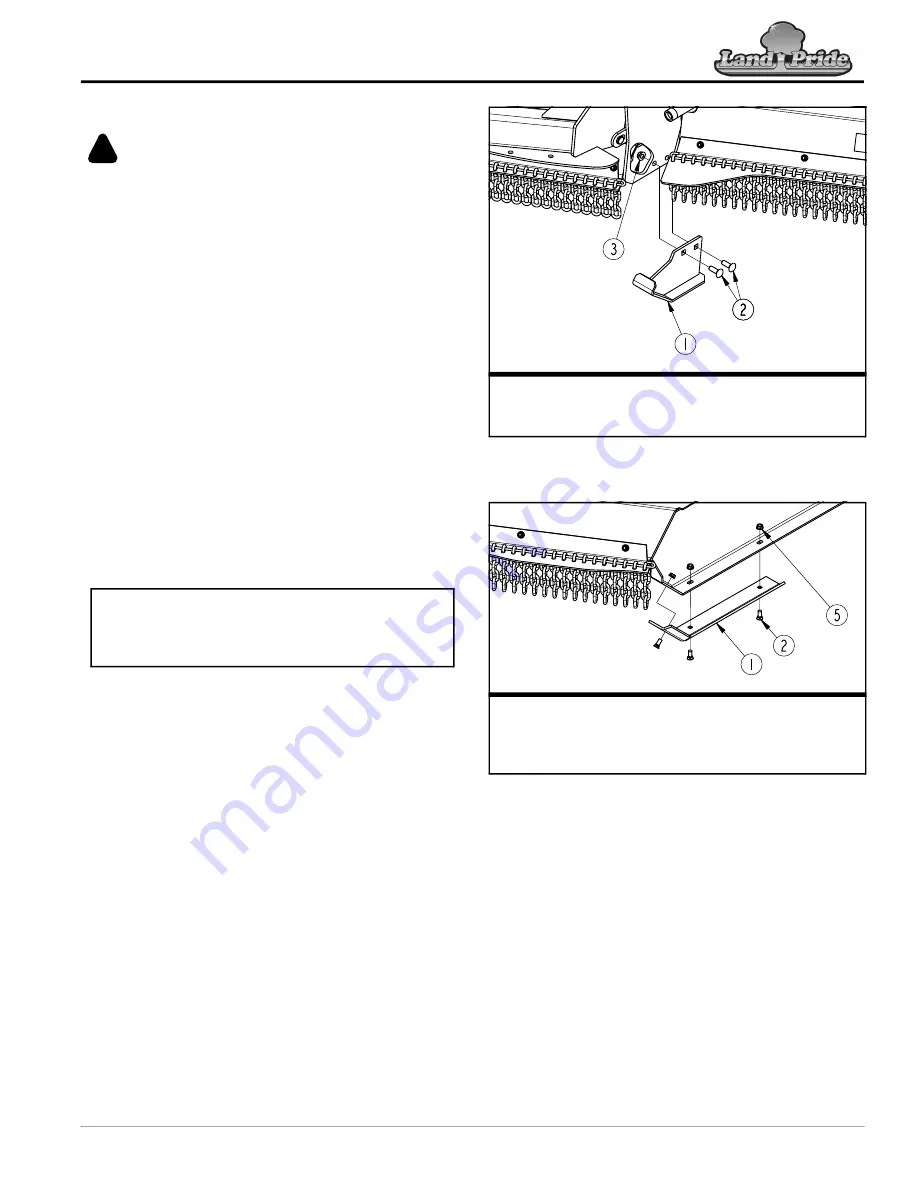
41
Section 5: Maintenance & Lubrication
10/7/21
RC2512 Series 2 S/N Rotary Cutters 330-725M
Skid Shoes
WARNING
!
To avoid serious injury or death:
Excessive wear on skid shoes may cause inadequate operation
of cutter and create a safety hazard.
Two skid shoes are mounted on the center section and
one skid shoe is mounted on each wing section. Check
all skid shoes for wear and replace if necessary. Order
only genuine Land Pride parts from your local Land Pride
dealer.
Center Deck Skid Shoes
Refer to Figure 5-7:
Replace skid shoes as follows:
1. Remove 1/2" hex whiz nuts (#3), 1/2" round head
square neck bolts (#2), and skid shoe (#1) from
cutter.
2. Attach new skid shoe (#1) to cutter with existing
1/2" round head square neck bolts (#2) and secure
with 1/2" hex whiz nuts (#3). Tighten hex whiz nuts to
the correct torque.
3. Repeat on opposite side of center deck.
Wing Skid Shoe
Refer to Figure 5-8:
Replace wing skid shoes as follows:
1. Remove 3/8" hex whiz nuts (#3), 3/8" plow bolts (#2),
and wing skid shoe (#1) as shown.
2. Plow bolts should be checked for wear and replaced
if necessary.
3. Attach new left-hand skid shoe (#1) to cutter with
3/8" -16 GR5 plow bolts (#2) and secure with 3/8" hex
whiz nuts (#3). Tighten hex whiz nuts to the correct
torque.
4. Repeat steps 1 through 3 on opposite wing section
for the right-hand skid shoe (#1).
IMPORTANT:
Excessive wear on skid shoes can
weaken cutter side panels and cause damage that
will require extensive repairs. Always replace skid
shoes at the first sign of wearing thin.
Center Skid Shoes
Figure 5-7
Wing Skid Shoe
Figure 5-8
37534
Item Part No.
Part Description
1
330-697H SKID SHOE
2
802-106C RHSNB 1/2-13X1 1/2 GR5
3
803-169C NUT HEX FLG LOCK 1/2-13 PLT
37535
Item Part No.
Part Description
1
331-347D SKID SHOE RIGHT-HAND
1
331-348D SKID SHOE LEFT-HAND (shown)
2
802-603C PLOW BOLT, 3/8" - 16 x 1" grade 5
3
803-198C HEX WHIZ NUT, 3/8"-16 PLT