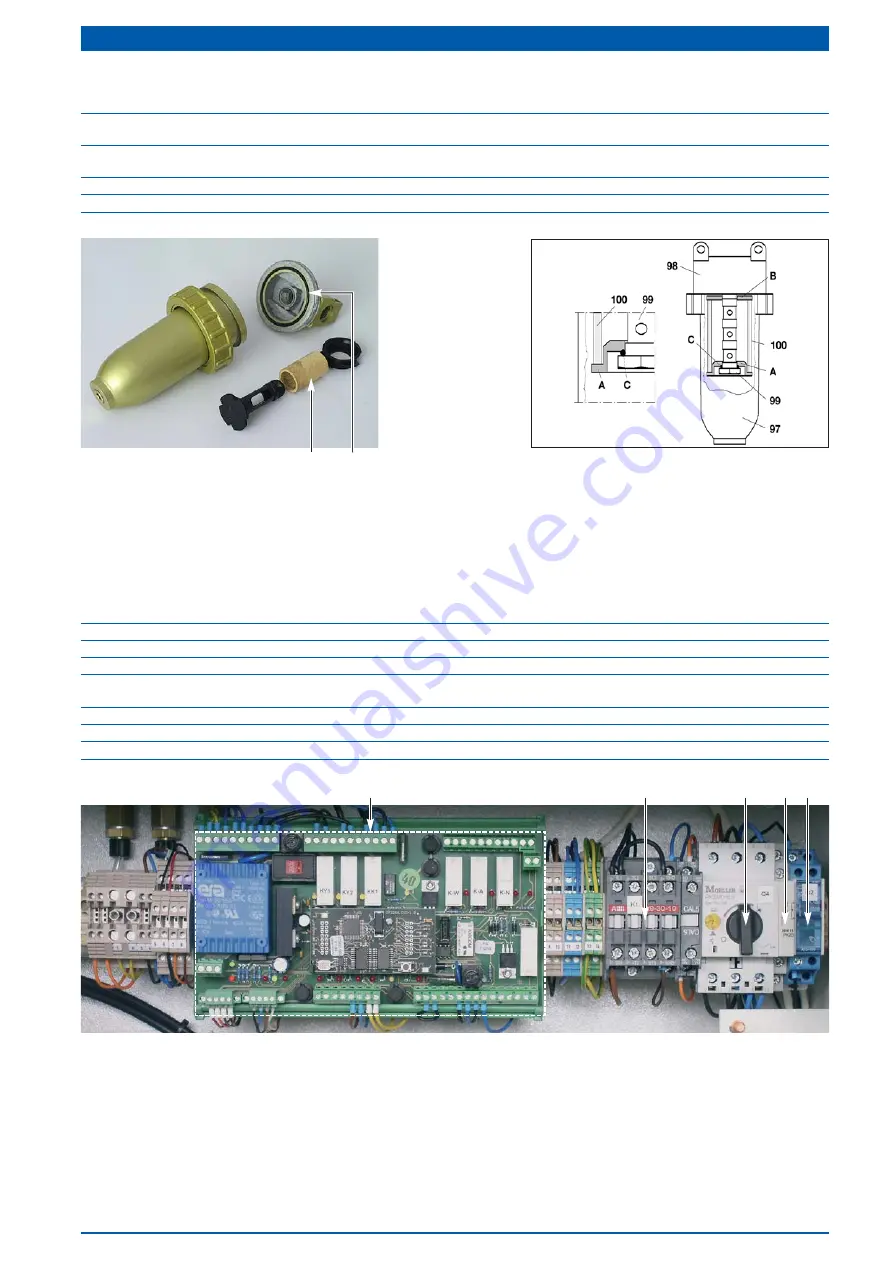
Page 55
Micro filter
Item Name
Order no.
Micro filter compl. (
33
)
RTS 1000D u. RTS 2600D
056358.000
Micro filter compl. (
33
)
RTS 5200D
057411.000
1*
Micro filter element (
96
)
RTS 1000D u. RTS 2600D
056359.000
Micro filter element (
96
)
RTS 5200D
057412.000
2
Seal (
97
) (
B
)
056360.000
C
O-Ring (
RTS 5200D
only) (
C
)
034390.000
1
2
Electrics
Item Name
Order no.
1
Auxiliary switch (
42
) of motor protective switch [Q4] (
5
)
067955.000
2
Motor contacter / switch [K1] (
56
)
073610.000
Auxiliary switch (
42
) of motor contacter / switch
073611.000
3
Motor protective switch [Q4] (
5
)
RTS 2600D
067950.000
Motor protective switch [Q4] (
5
)
RTS 1000D u. RTS 5200D
067951.000
4
Main switch signal voltage DC [Q2] (
6
)
073370.000
5
Multifunktional relay MFR (
73
)
073285.000
6
Power pack 230 V AC/60 DC (Option, no illustration)
071662.000
5
2
3
1
4
Summary of Contents for RTS 1000D
Page 43: ...Page 43 Compressor VD 7 2 RTS 1000D and VD 28 2 RTS 2600D B...
Page 45: ...Page 45 Compressor VD 50 4 RTS 5200D...
Page 57: ...Compressor VD 7 2 and VD 28 2 Page 57...
Page 59: ...Page 59 Compressor VD 50 4...
Page 61: ...Page 61 Pneumatics diagram RTS 1000D RTS 2600D and RTS 5200D no 073445 072...
Page 63: ...Page 63 Circuit and wiring diagram RTS 1000D RTS 2600D und RTS 5200D no 073659 000...
Page 65: ...Page 65 Circuit and wiring diagram RTS 1000D RTS 2600D und RTS 5200D no 073586 000...
Page 66: ...Page 66...
Page 67: ...Page 67...