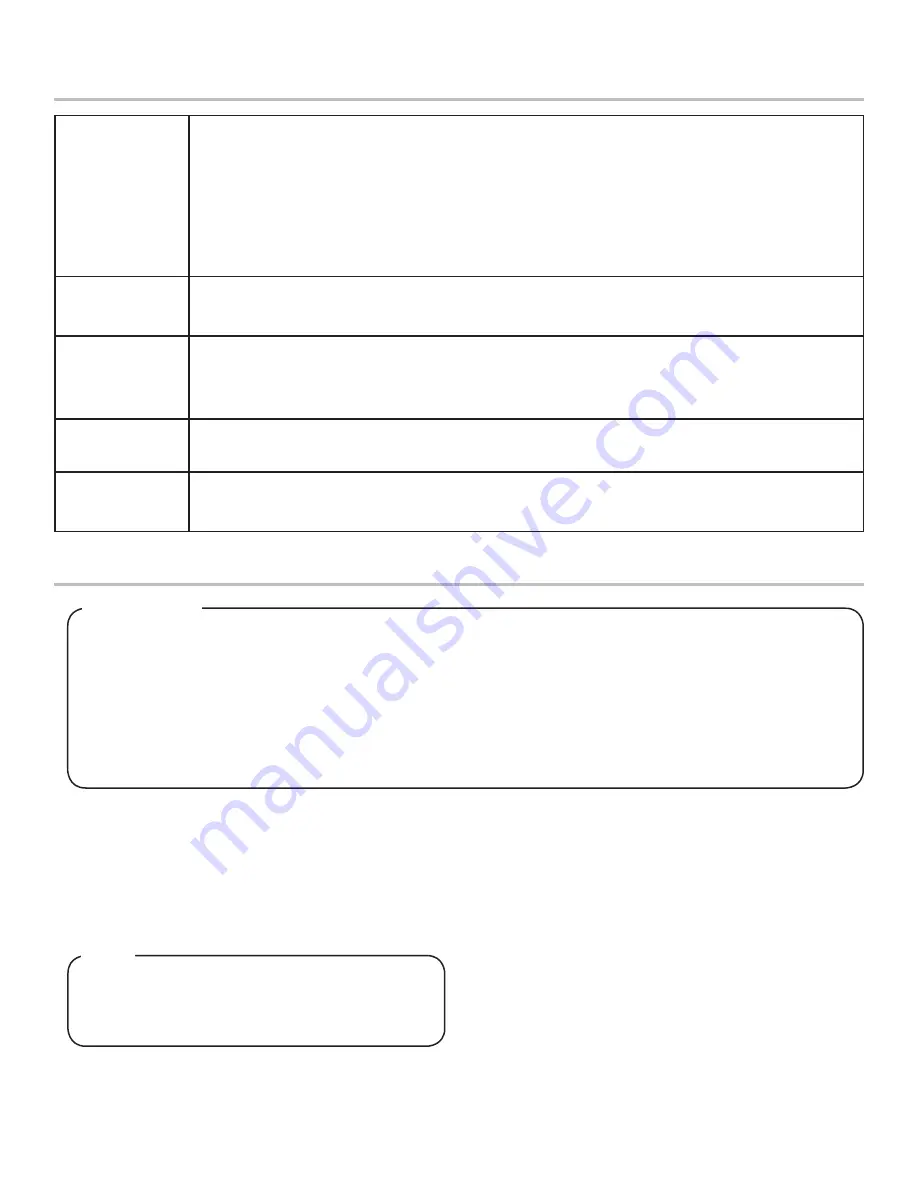
8
SCHEDULED MAINTENANCE
•
Use sanitary gloves when cleaning the unit and observe all applicable safety precautions.
• DO NOT
use a water jet to clean or sanitize the unit.
• DO NOT
disconnect water lines when cleaning and sanitizing syrup lines, to avoid contamination.
• DO NOT
use strong bleaches or detergents; These can discolor and corrode various materials.
• DO NOT
use metal scrapers, sharp objects, steel wool, scouring pads, abrasives, or solvents on the dispenser.
• DO NOT
use hot water above 140° F (60° C). This can damage the dispenser.
• DO NOT
spill sanitizing solution on any circuit boards. Insure all sanitizing solution is removed from the system.
!
ATTENTION
The cleaning procedures provided herein pertain to the
Lancer equipment identified by this manual. If other
equipment is being cleaned, follow the guidelines
established by the manufacturer for that equipment.
NOTE
CLEANING AND SANITIZING
General Information
•
Lancer equipment (new or reconditioned) is shipped from
the factory cleaned and sanitized in accordance with NSF
guidelines. The operator of the equipment must provide
continuous maintenance as required by this manual and/
or state and local health department guidelines to ensure
proper operation and sanitation requirements are
maintained.
•
Cleaning should be accomplished only by trained personnel.
Sanitary gloves are to be used during cleaning operations.
Applicable safety precautions must be observed. Instruction
warnings on the product being used must be followed.
Cleaning Solution
Mix a mild, non-abrasive detergent (e.g. Sodium Laureth
Sulfate, dish soap) with clean, potable water at a temperature
of 90°F to 110°F (32°C to 43°C). The mixture ratio is one ounce
of cleaner to two gallons of water. Prepare a minimum of five
gallons of cleaning solution. Do not use abrasive cleaners or
solvents because they can cause permanent damage to the unit.
Ensure rinsing is thorough, using clean, potable water at a
temperature of 90°F to 110°F. Extended lengths of product lines
may require additional cleaning solution.
Sanitizing Solution
Prepare the sanitizing solution in accordance with the
manufacturer’s written recommendations and safety guidelines.
The type and concentration of sanitizing agent recommended in
the instructions by the manufacturer shall comply with 40 CFR
§180.940. The solution must provide 100 parts per million (PPM)
chlorine (e.g. Sodium Hypochlorite or bleach) and a minimum of
five gallons of sanitizing solution should be prepared.
Daily
•
Remove each nozzle and rinse well in warm water.
DO NOT
use soap or detergent. This will cause foam-
ing and off tast in finished product.
•
Remove cup rest and wash in warm soapy water.
•
Pour warm soapy water into the drip tray and wipe with a clean cloth.
•
With a clean cloth and warm water, wipe off all of the unt’s exterior surfaces.
DO NOT USE ABRASIVE
SOAPS OR STRONG DETERGENTS.
•
Replace the cup rest and nozzles.
Weekly
•
Taste each product for off tastes.
•
Remove cup rest and splash plate to view water level tube indicator, replenish as required.
Monthly
•
Unplug the dispenser from the power source.
•
Remove the bonnet and clean the dirt from the condenser using a soft brush.
•
Replace the bonnet and plug in the unit.
Every Six Months
•
Clean and sanitize the unit using the appropriate procedures outlined in the Cleaning and Sanitizing
section of this guide.
Yearly
•
Clean water bath interior, including evaporator coils and refrigeration components.
•
Clean the entire exterior of the unit