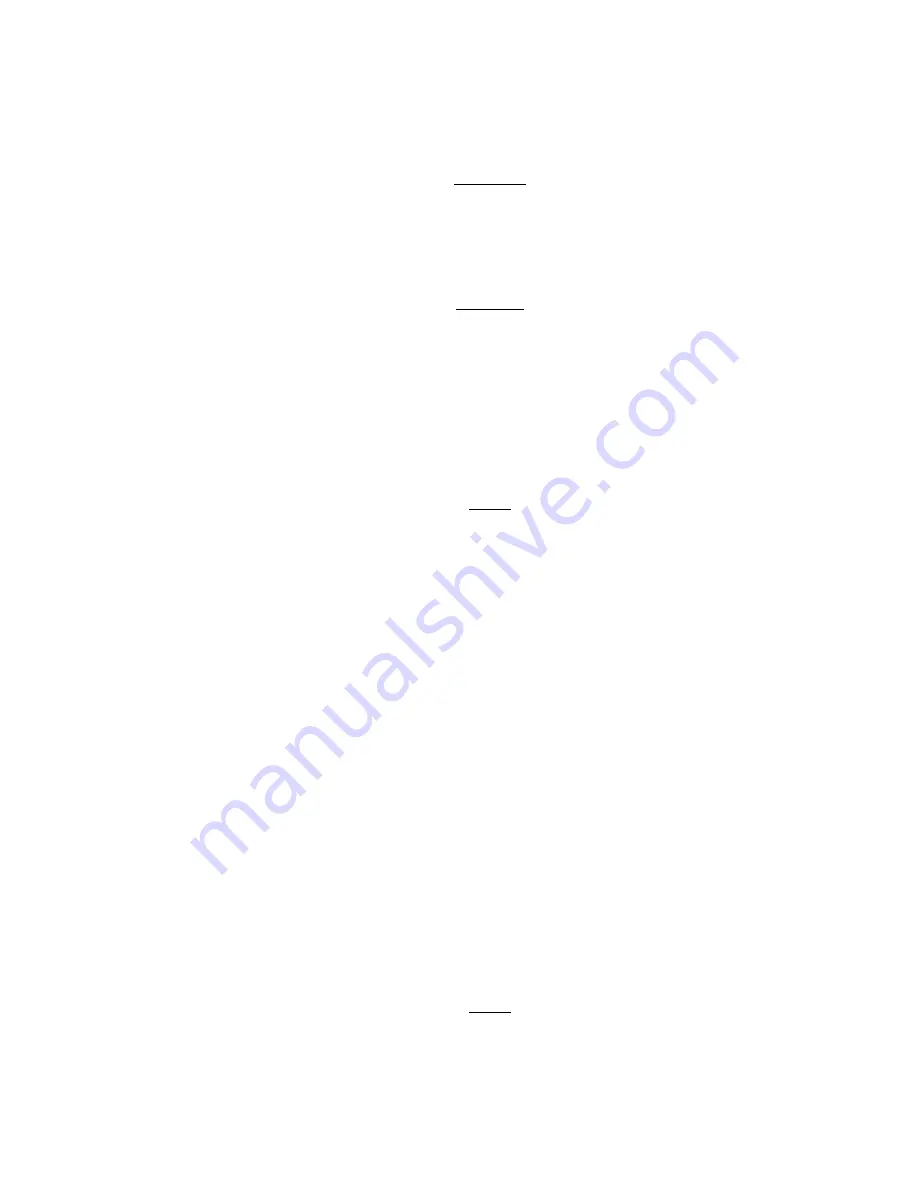
Use bottled drinking water where hard water problems exist.
Do not use distilled water in
units which are equipped with electronic ice bank controls (EIBC).
D. Replace the yellow plug.
1.6
CONNECTING TO ELECTRICAL POWER
WARNING
THIS UNIT MUST BE PROPERLY ELECTRICALLY GROUNDED TO AVOID POSSIBLE FATAL
ELECTRICAL SHOCK OR SERIOUS INJURY TO THE OPERATOR. THE POWER CORD IS
PROVIDED WITH A THREE PRONG GROUNDED PLUG. IF A THREE-HOLE GROUNDED
ELECTRICAL OUTLET IS NOT AVAILABLE, USE AN APPROVED METHOD TO GROUND THE
UNIT.
CAUTION
FAILURE TO DISCONNECT THE MOTOR POWER SUPPLY WILL DAMAGE THE CARBONATOR
MOTOR AND PUMP AND VOID THE WARRANTY.
A. Check the dispenser serial number plate for unit’s correct electrical requirements. Do not plug
into electrical outlet unless serial number plate electrical specifications are compatible with local
electric utility.
B. Route the power supply cord to a grounded electrical outlet of the proper voltage and amperage
rating, and plug the unit in. All USA/domestic models are equipped with a power kill switch
located on the left side of the condenser, in the bonnet.
Kill switch must be on before the unit
will operate.
Allow unit to run and start cooling while completing remainder of the installation.
NOTE
Units equipped with an electronic ice bank control contain a five (5) minute delay
. Compressor
will not begin running until five (5) minutes after unit is energized.
1.7
CONNECTING TO PRODUCT SUPPLY (see Page ii)
A. Using proper beverage tubing and fittings, connect to product inlet with a clamp (PN 07-0437).
B. Mark syrup tube assemblies with product ID tape.
C. Route through cutout in counter or through access hole in back of unit.
D. Leave approximately 12 inches (300 mm) of extra tubing length below the counter for servicing
and moving the dispenser.
E. Connect to appropriate figal pre-mix tanks using clamps to secure the connection.
F.
Pressurize system.
G. Activate each valve until product is observed.
H. Check for leaks.
2.
SCHEDULED MAINTENANCE
2.1
DAILY
A. Remove the cup rest and wash in warm soapy water.
B. Pour warm soapy water into the drip tray and wipe with a clean cloth.
C. With a clean cloth and warm water, wipe off all of the unit’s exterior surfaces. DO NOT USE
ABRASIVE SOAPS OR STRONG DETERGENTS.
D. Replace the cup rest.
2.2
WEEKLY
A. Taste each product for off tastes.
B. Remove the bonnet and check the level of water in the water bath. Replenish as required, and
replace the bonnet.
NOTE
Use bottled drinking water where hard water problems exist.
Do not use distilled water in units
which are equipped with electronic ice bank controls (EIBC).
2.3
MONTHLY
A. Unplug the dispenser from power source.
2