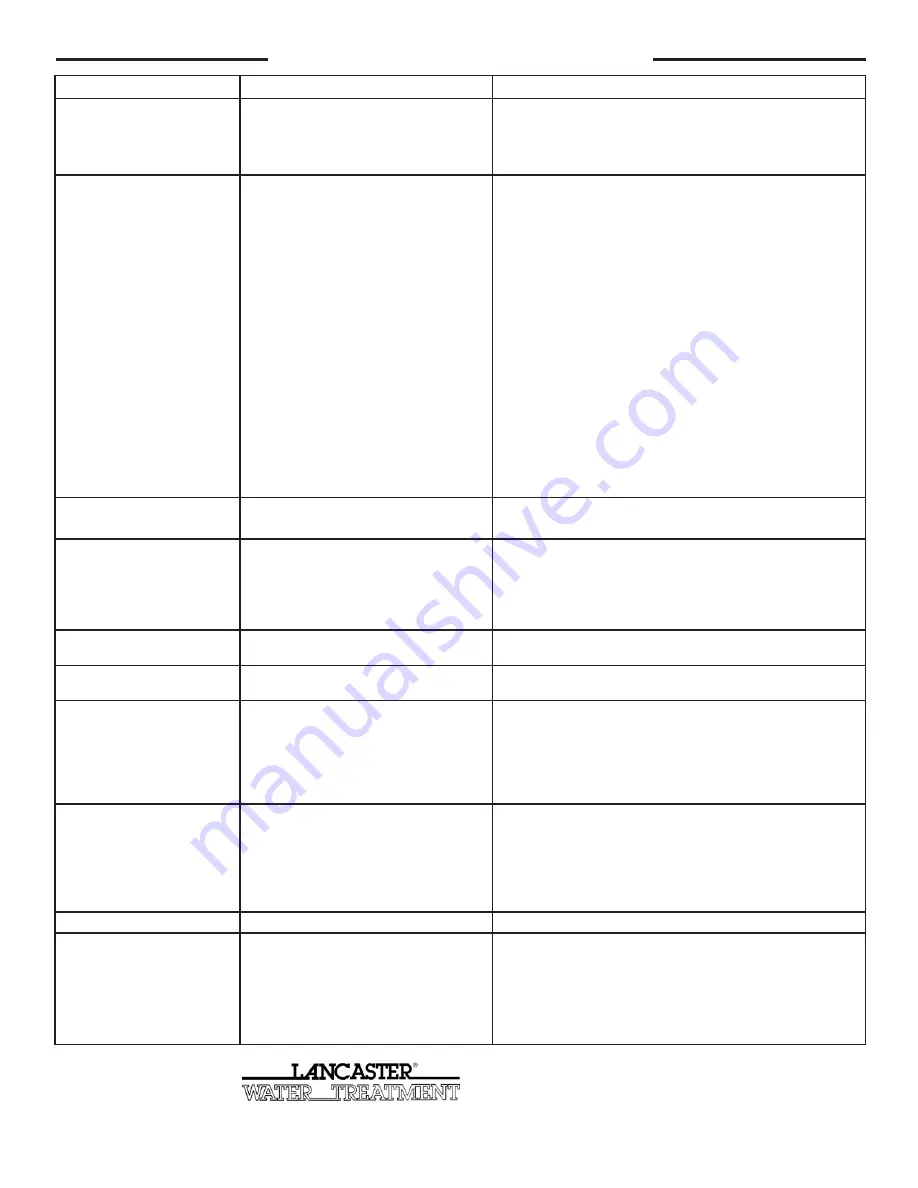
PAGE 8
A DIVISION OF C-B TOOL CO.
1340 MANHEIM PIKE ● LANCASTER PA 17601-3196 ● TEL:717-397-3521 ● FAX: 717-392-0266
www.lancasterwatertreatment.com ● E-mail: [email protected]
11/16
TROUBLESHOOTING PROCEDURES
PROBLEM
POSSIBLE CAUSE
SOLUTION
1. Softener fails to regenerate.
a. Electrical service to unit has been
interrupted.
a. Assure permanent electrical service.
b. Timer is defective.
b. Replace timer.
c. Power failure.
c. Reset time of day.
2. Softener delivers hard water.
a. By-pass valve is open.
a. Close by-pass valve.
b. No salt in brine tank.
b. Maintain salt level above water level.
c. Injectors or screen plugged.
c. Clean or replace injectors and screen.
d. Insufficient water flowing into brine tank.
d. Check fill time and clean brine line plug if clogged.
e. Hot water tank hardness.
e. Empty hot water tank.
f. Leak at distributor tube.
f. Make sure distributor tube is not cracked. Check O-Ring and
tube pilot.
g. Internal valve leak.
g. Replace seals and spacer and/or piston.
h. Reserve Capacity has been exceeded.
h. Check Salt dosage requirements and reset program wheel to
provide additional reserve.
i. Program wheel is not rotating with meter
output.
i. Pull cable out of meter cover and rotate manually. Program wheel
must move without binding and clutch must give positive “clicks”
when program wheel strikes regeneration stop. If it does not,
replace timer.
j. Meter is not measuring flow.
j. Check output by observing rotation of small gear on front of timer.
Note - program wheel must not be against regeneration stop for
this check). Each tooth to tooth is approximately 30 gallons. If
not performing properly, replace meter.
3. Unit uses too much salt.
a. Improper salt setting.
a. Check salt usage and salt setting.
b. Excessive water in brine tank.
b. See problem no. 7.
4. Loss of water pressure.
a. Iron buildup in line to water conditioner.
a. Clean line to water conditioner.
b. Iron buildup in water conditioner.
b. Clean control, increase frequency of regeneration and use a
resin cleaner.
c. Inlet of control plugged by foreign material. c. Remove piston and clean control.
5. Loss of resin out of drain line. a. Air in water system
a. Assure that well system has proper air eliminator control. Check
for dry well condition.
6. Iron in conditioned water.
a. Fouled resin bed.
a. Check backwash, brine draw and brine tank fill. Increase
frequency of regeneration and use a resin cleaner.
7. Excessive water in brine tank.
a. Plugged drain line flow control.
a. Clean flow control.
b. Plugged injector system.
b. Clean injector and replace screen.
c. Timer not cycling.
c. Replace timer.
d. Foreign material in brine valve.
d. Clean or replace brine valve.
e. Foreign material in brine line flow control.
e. Clean brine line flow control.
8. Softener fails to draw brine.
a. Drain line flow control is plugged.
a. Clean drain line flow control.
b. Injector is plugged.
b. Clean or replace injectors.
c. Injector screen plugged.
c. Replace screen.
d. Line pressure is too low.
d. Increase line pressure to at least 20 psi.
e. Internal control leak.
e. Change seals and spacers and/or piston assy.
9. Control cycles continuously.
a. Faulty timer mechanism
a. Replace timer.
10. Drain flows continuously.
a. Foreign material in control.
a. Advance control through various regeneration positions. Remove
foreign material in control.
b. Internal control leak.
b. Replace seals and/or piston assy.
c. Control valve jammed in brine or
backwash position.
c. Replace piston, seals and spacers.
d. Timer motor stopped or jammed.
d. Replace timer.