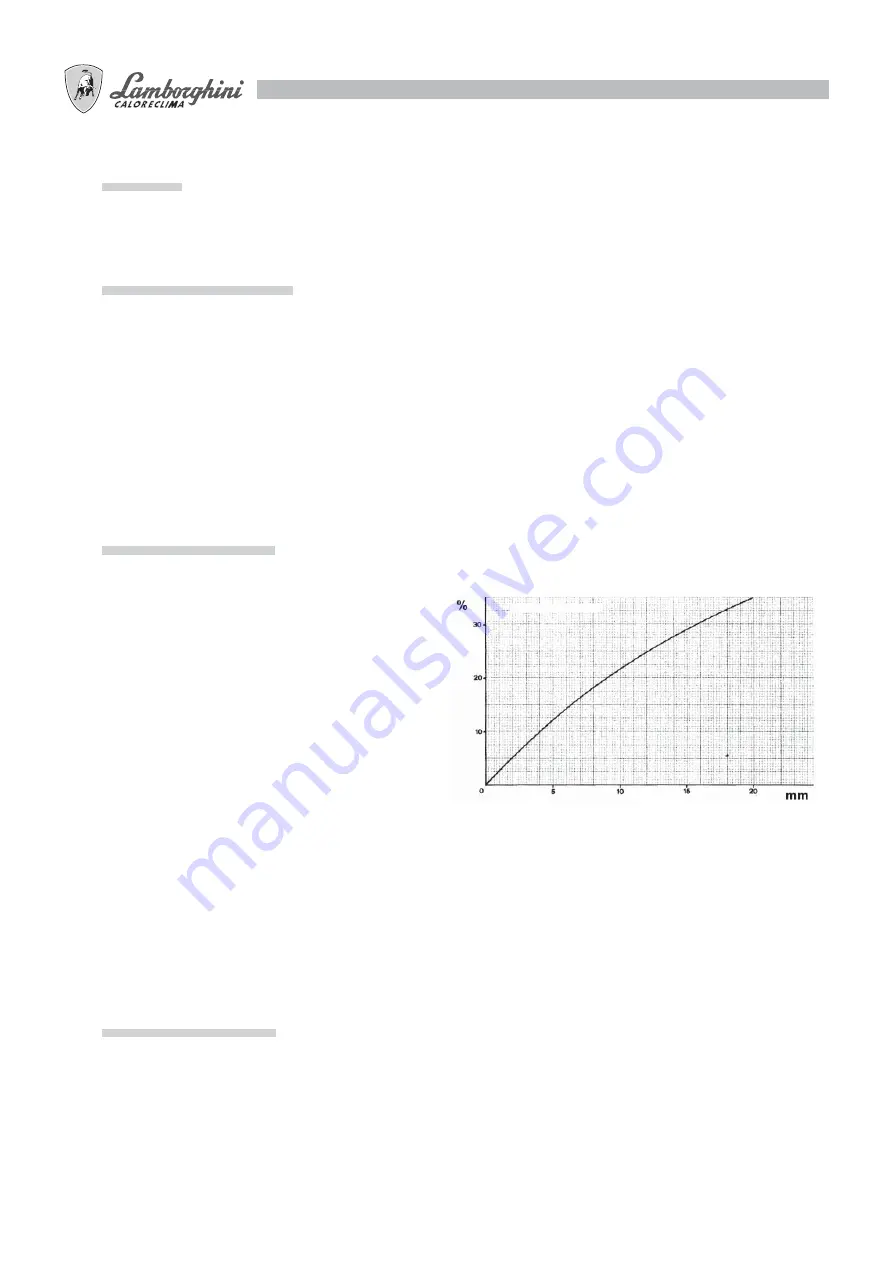
START UP
WARNING
Before start up insert wholly turbolators into the smoke tubes ensuring that they have been pushed inside for at least 100 mm.
START UP
Before starting the boiler, check that:
- the
rating plate
specifications and power supply network (electricity, water, gas or fuel oil) specifications correspond;
- the burner
power range
is compatible with the power of the boiler;
- the boiler room also contains the instructions for the burner;
- the
flue gas exhaust pipe
is operating correctly;
- the
air inlet supply
is well dimensioned and free from any obstacle;
- the
manhole
, the
smokebox
and the
burner plate
are closed in order to provide a complete flue gas seal;
- the system is
full of water
and that any
air pockets
have therefore been eliminated;
- the
anti-freeze
protections are operative;
- the water
circulation pumps
are operating correctly.
- The expansion vessel and the safety valve(s) have been connected correctly (with no interception) and are properly operating.
- Check the electrical parts and thermostat operation.
PRELIMINARY CHECKS
The most common phenomena that occur in heating
systems are:
-
Scaling
Scale obstructs heat transfer between the combustion
gases and the water, causing an abnormal increase in
the temperature of the metal and therefore reducing the
life of the boiler.
Scale is found mostly at the points where the wall tem-
perature is highest and the best remedy, at construction
level, is to eliminate areas that overheat.
Scale creates an insulating layer which reduces the
thermal transfer of the generator, affecting system effi-
ciency.
This means that the heat produced by burning the fuel
is not fully exploited and is lost to the flue.
WATER TREATMENT
The water must enter the system as slowly as possible and in a quantity proportional to the air bleeding capacity
of the components involved. Filling times vary depending on the capacity and characteristics of the system but
should never be less than 2 or 3 hours.
In the case of a system with closed expansion vessel, water must be let in until the pressure gauge indicator reaches the
static pressure value pre-set by the vessel. Heat the water to maximum temperature and never over 90°C. During this
operation the air contained in the water is released through the automatic air separators or through manual bleed valves.
The water discharged from the system with elimination of the air is made up by the automatic or manual filling valve.
FILLING THE SYSTEM
-
Corrosion on the water side
Corrosion of the metal surfaces of the boiler on the water side is due to the passage of dissolved iron through its ions
(Fe+). In this process the presence of dissolved gases and in particular of oxygen and carbon dioxide is very important.
Corrosion often occurs with softened or demineralised water which has a more aggressive effect on iron (acid water
with Ph <7): in these cases, although the system is protected from scaling, it is not protected against corrosion and the
water must be treated with corrosion inhibitors.
Scale diagram
%
fuel not used
mm
mm
scale
Scale diagram
- 24
-
Summary of Contents for MEGA PREX BT 100
Page 2: ...2 ITALIANO 3 ENGLISH 15 FRAN AISE 27 ESPA OL 39...
Page 51: ...51...