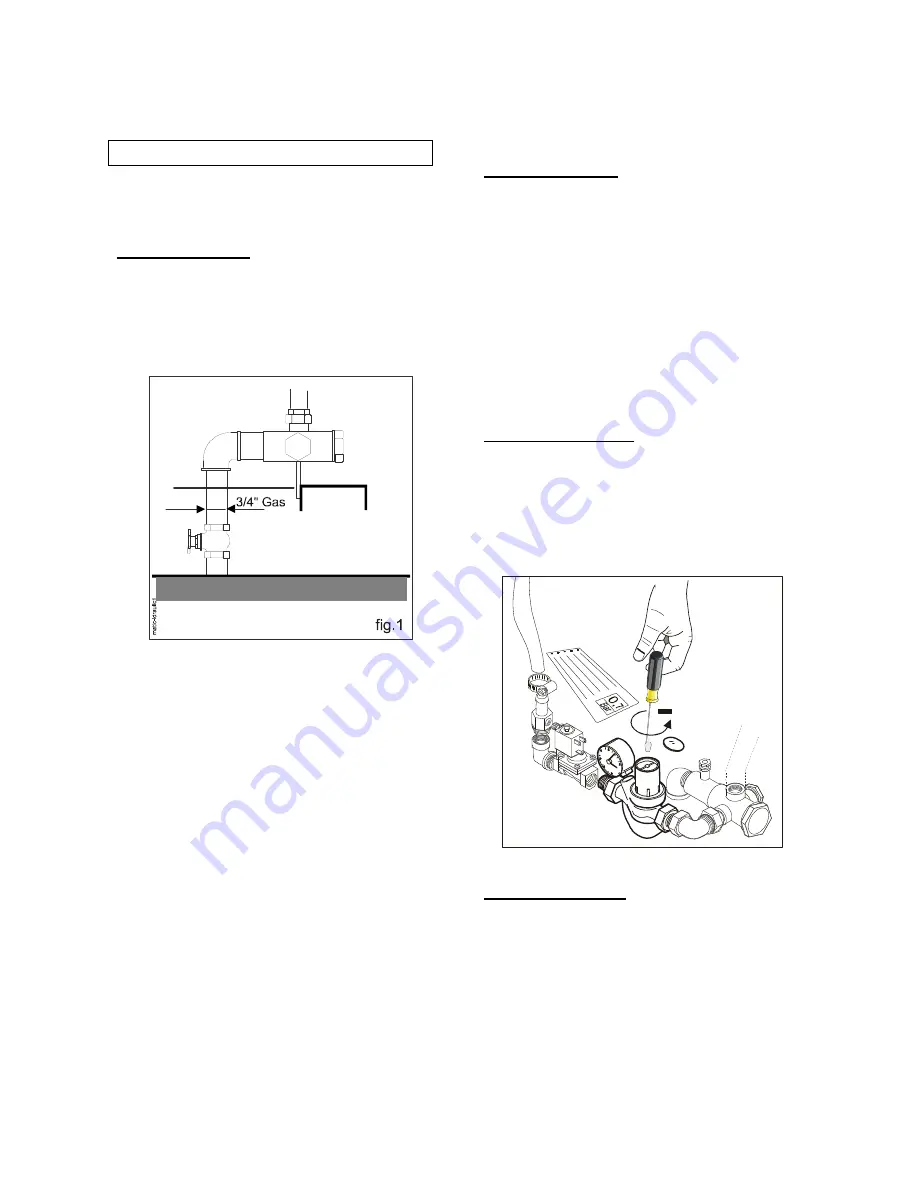
30
WATER CONNECTIONS
Carefully comply with any national or
regional regulations in force.
Hot water supply
Arrange a gate valve in an easily
accessible place, with a tap having a
3/4"gas thread spout at its end and connect
to the water inlet valve (fig.1)
-
temperatur
between 55° and 60°C,
-
Dynamic Pressure
2÷4 bar (200÷400
kPa),
-
Hardness
between
7,2 and 12,5 °F
N.B.:
Each machine is equipped with a
pressure reducer. In order to obtain an
excellent rinsing, it shall be calibrated
according to the data reported on the plate
located in connection with the reducer
itself.
N.B.:
Each machine is equipped with a
pressure reducer near the water inlet
valves.
In order to obtain an optimum rinse it is
necessary to adjust it from 0,6 to 1 bar
according to inlet water pressure and
temperature.
(remember that the required dynamic
pressure must be 2÷4 bar (200÷400kPa)
and that inlet water temperature must be
55÷60°C for standard machines).
If a variation of rinse pressure is required
while installing, proceed as follows:
1: make the machine work and check that
the rinse is activated;
2: Take away the upper protection plug on
the reduction gear and turn the proper
adjusting screw anti-clockwise in order to
decrease pressure or clockwise in order to
increase it or to restore the optimum
working conditions (see picture 1A).
PIC.1A- PRESSURE REDUCER
Cold water supply
This connection is required only for
machine with
steam condenser .
Water shall be supplied at a temperature
ranging from 10÷15°C and at a dynamic
pressure of 2÷4 bar (200÷400 kPa).
Summary of Contents for M115
Page 1: ...DISHWASHERS WITH PULL THROUGH RACK INSTRUCTIONS MANUAL M115 R06 2012...
Page 2: ......
Page 5: ...5 WASHING RINSING M O D E L M O D E L M115 left right M115 right left...
Page 13: ...INSTRUCTIONS FOR THE USER...
Page 26: ...26...
Page 42: ...42...